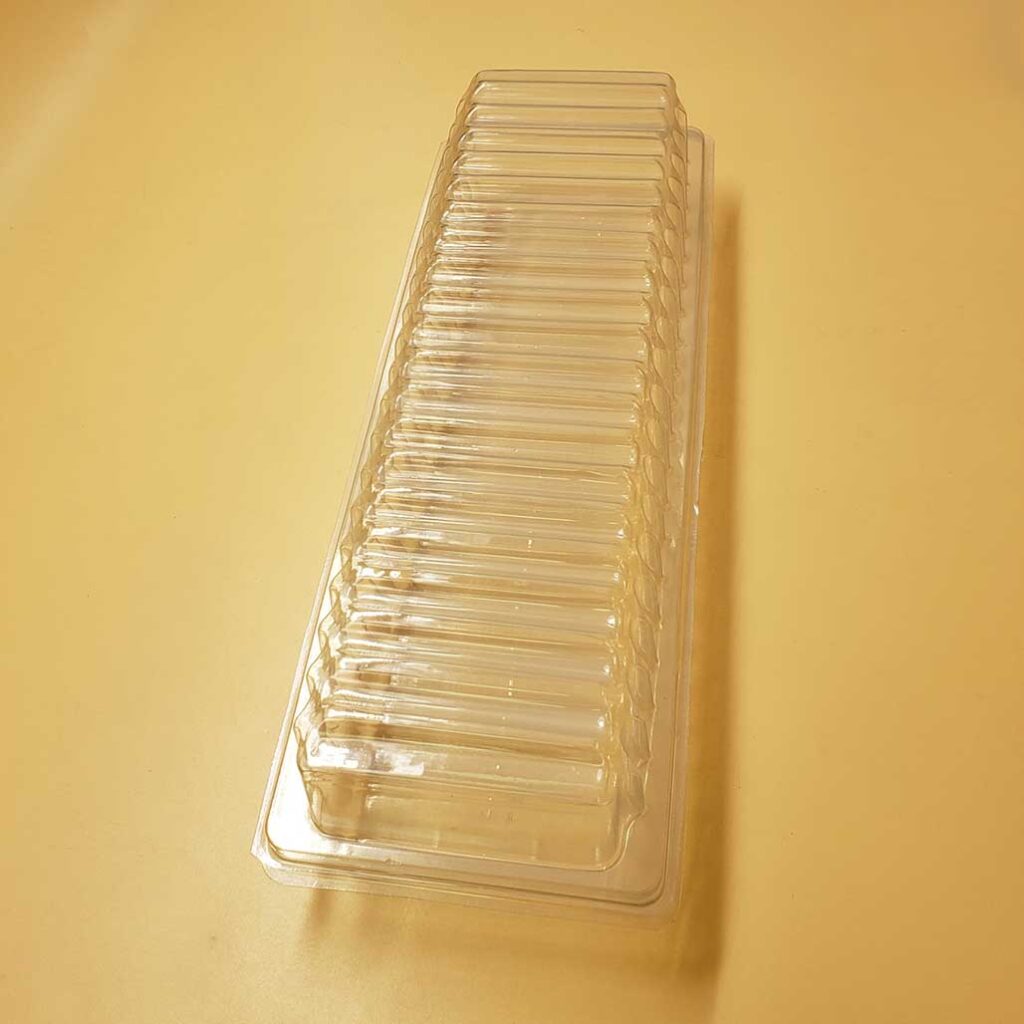
The size of vacuum molding can be divided into three types: copying according to customer samples (making molds is called duplicate molds), making molds according to drawings, and designing according to the actual product.
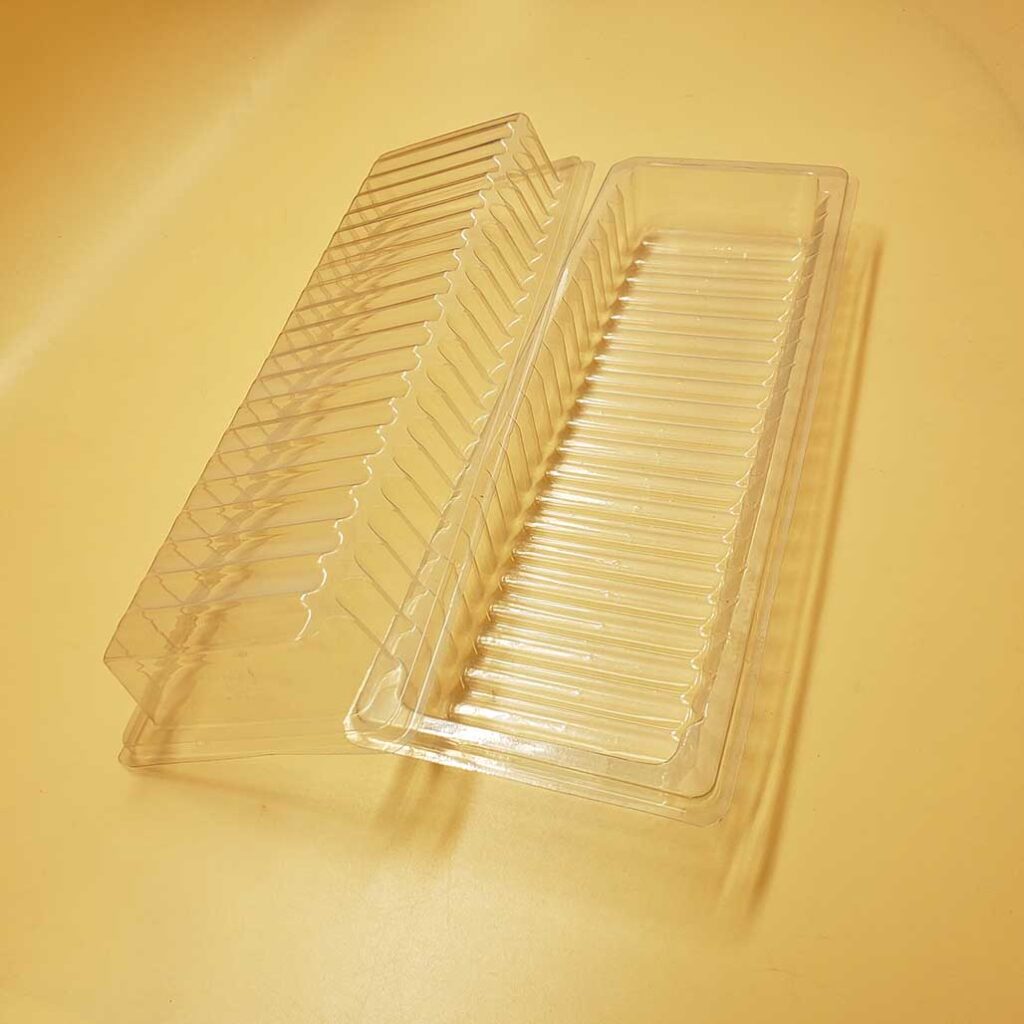
Because the shape of vacuum molding is usually customized based on the actual product, the shape is often irregular, and there are many dimensions that are inaccurate or cannot be marked during drawing production, resulting in significant deviations when making according to the drawing. For accuracy, it must be accompanied by a physical trial assembly.
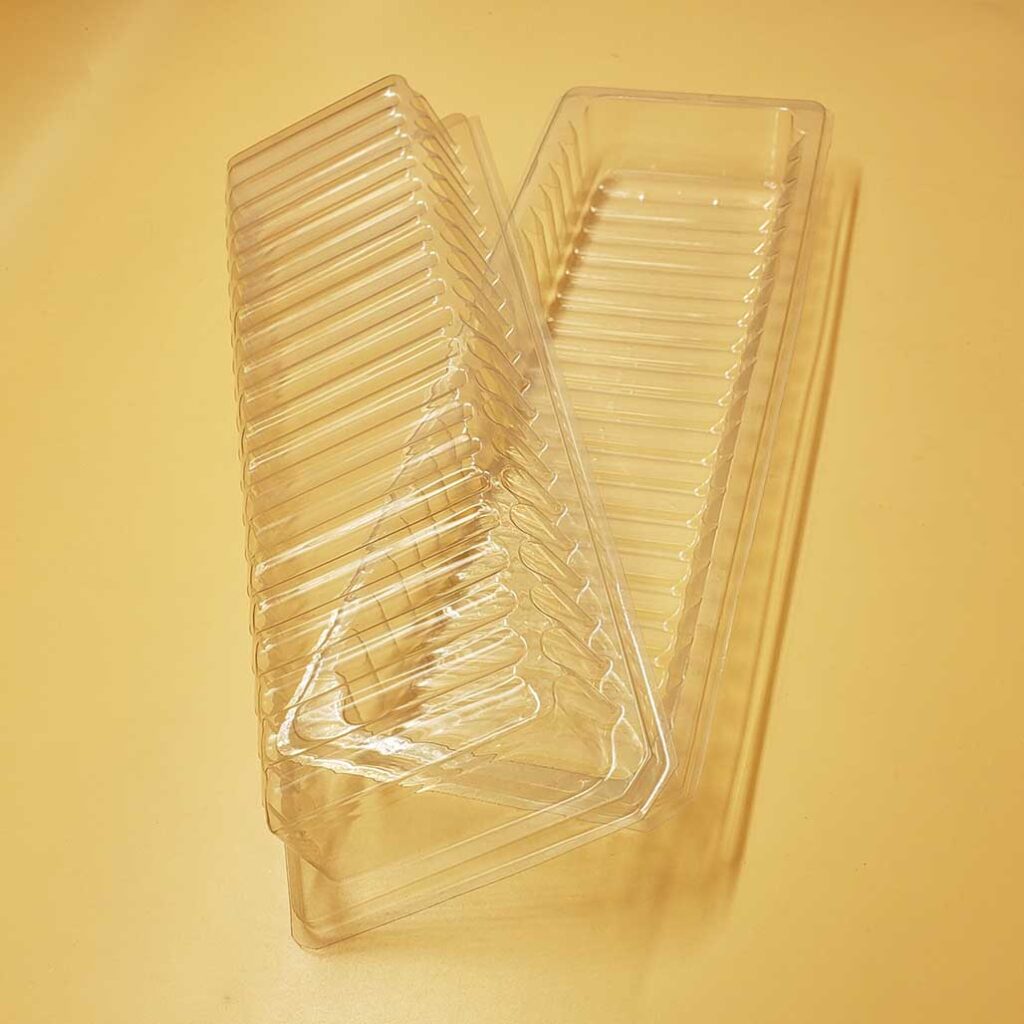
The size deviation of the product produced by replicating the sample is not significant.

The general thickness tolerance is 0.1mm, and the product deviation is ± 2mm. The main reasons for the occurrence of tolerances are:

Deviation caused by manual mold lifting. This deviation is generally less than 2mm.
The deviation generated when copying sub models. This deviation is relatively small, generally less than 0.5mm.

Thickness deviation of the same mold due to different materials and blister temperatures. This deviation is relatively small, generally less than 0.1mm.
The thickness tolerance depends on the specific situation, and the larger the same area is pulled, the thinner the thickness of the block becomes. Different operators and temperatures can also result in different thicknesses of the same part.

Among the above reasons, the first one is the main cause of dimensional tolerance, but since the mold can be modified and corrected, the deviation of vacuum molding can generally be controlled within 2mm.
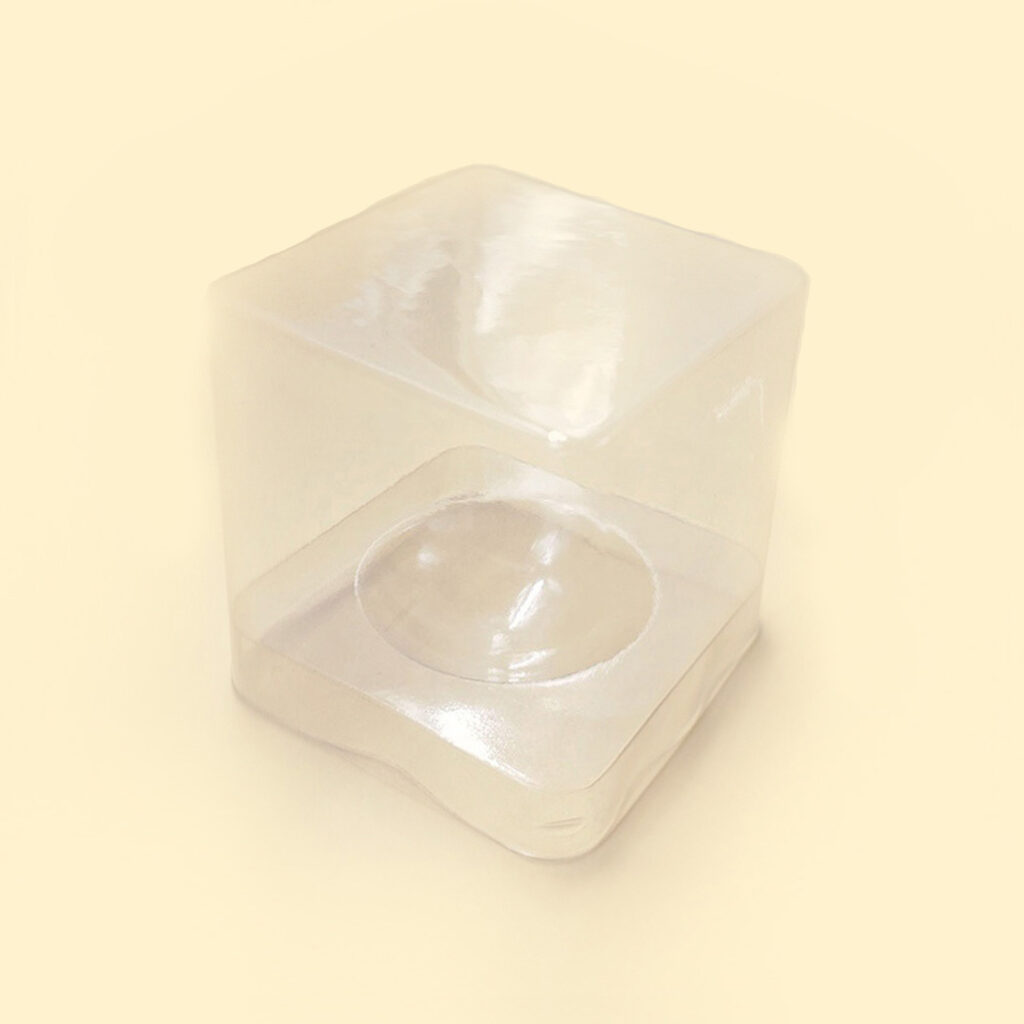
It should be noted that the material thickness is two sizes smaller than the finished product thickness (0.05mm). Although there are phenomena where the surface area of the finished product is much larger than that of the material, the thickness of the finished product is much smaller than that of the material, and the surface area of the finished product is much larger than that of the material, the thickness of the finished product is much smaller than that of the material. However, overall, the difference is generally 0.05mm. Vacuum molding is a very clear “tailor-made” product, and if you want the size to be suitable, you must take a physical sample to try and install.
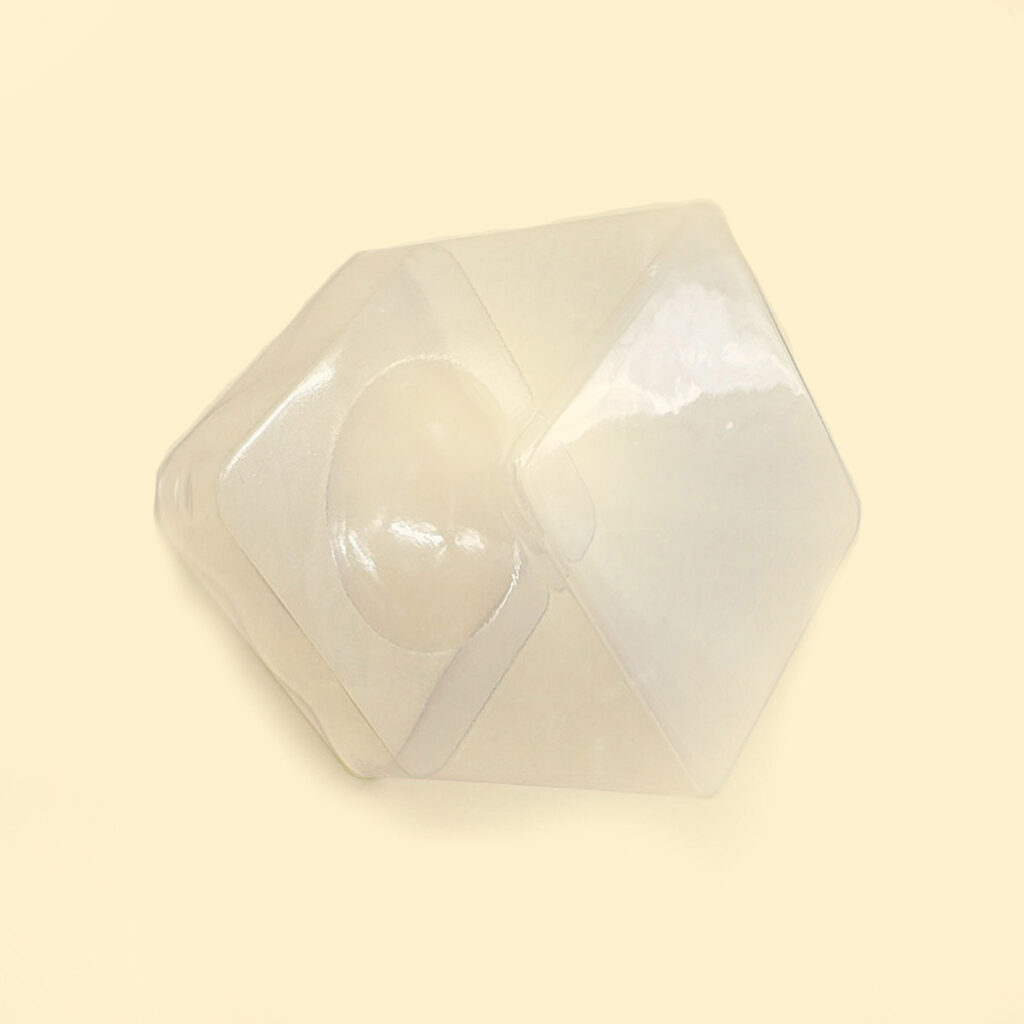