PP sheets are mainly made of polypropylene resin as the main raw material, with various process color masterbatches, toughening agents, and brighteners added.
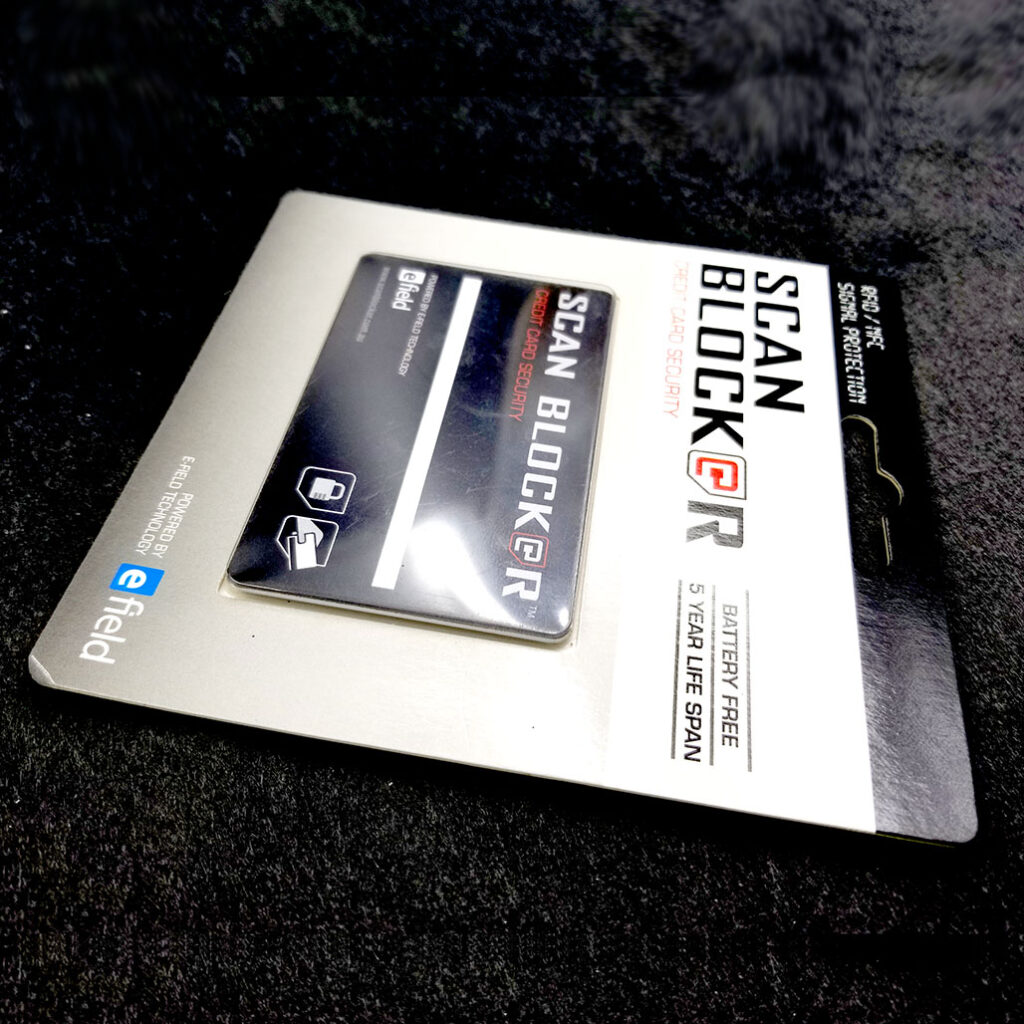
They are made through mixing, plasticizing extrusion, three roll calendering, cooling, traction, and winding processes. PP sheets have the characteristics of being non-toxic, odorless, hygienic, with high mechanical strength and good barrier properties, and can be used for packaging in industries such as industry, agriculture, and fruits. The surface of the tray made of PP anti slip sheets is smooth and beautiful, which is highly welcomed by users. PP sheet is also suitable for packaging of high cold resistant frozen foods, such as ice cream boxes, dumplings boxes, dumplings boxes, etc
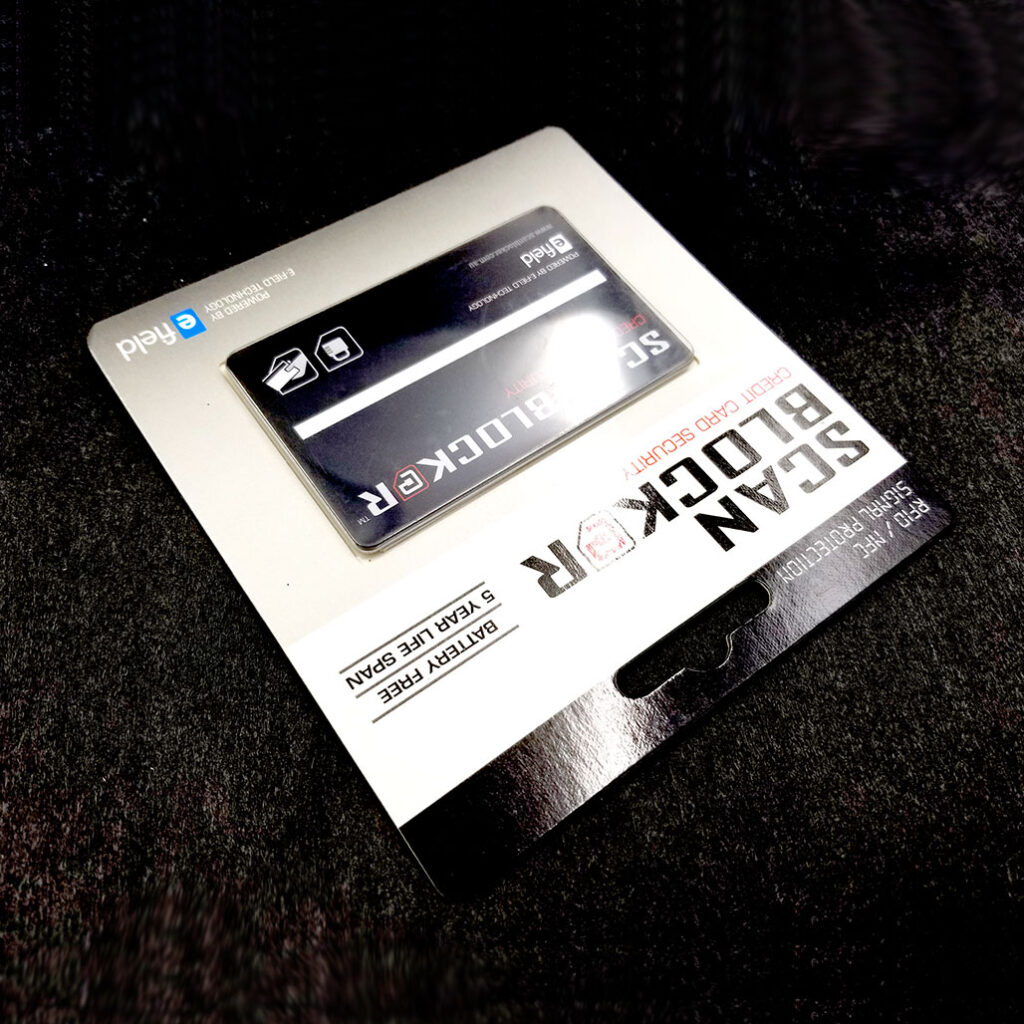
PP vacuum molding has the advantages of environmental protection, aesthetics, silk screen printing, offset printing, hot stamping, high temperature resistance, low temperature resistance, high transparency, resistance to bending and easy folding, product compliance with food testing standards (or not required), and microwave capability.
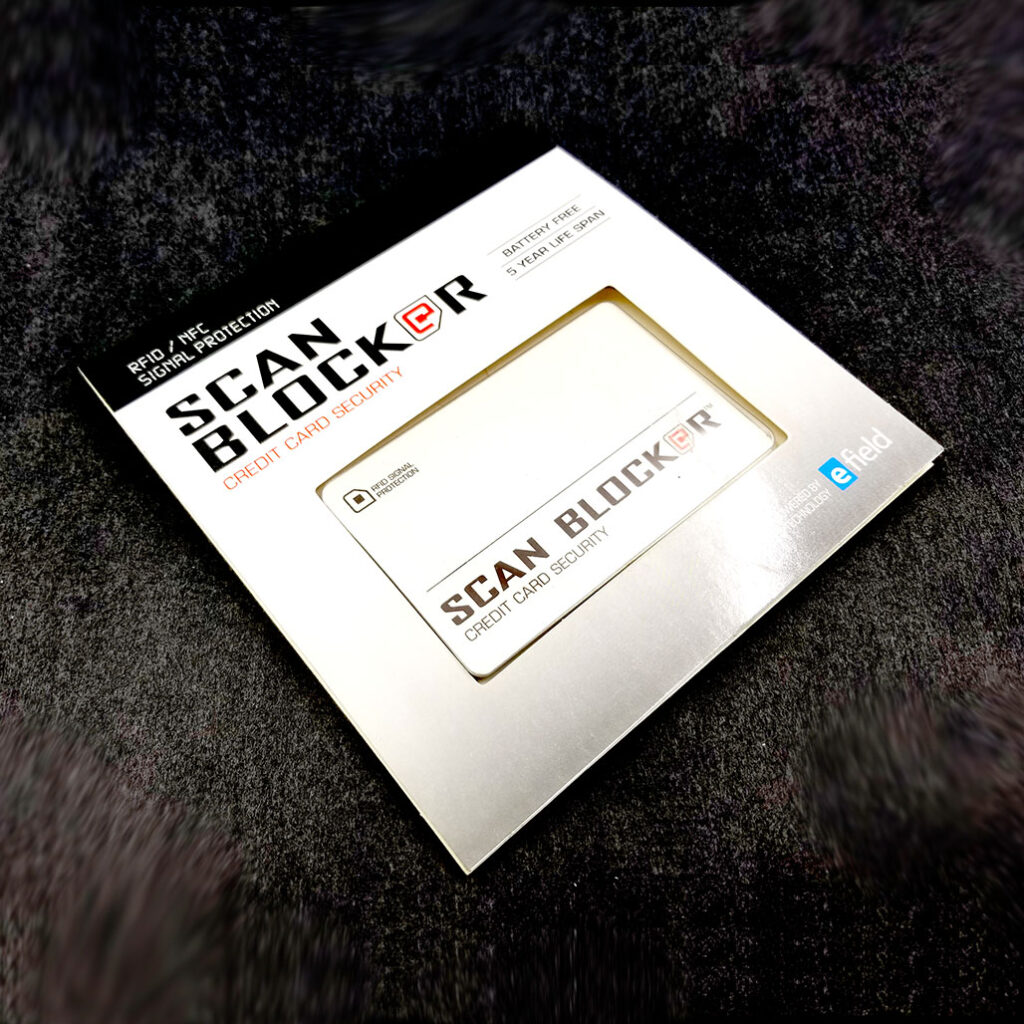
The disadvantages of PP include low dimensional accuracy, insufficient rigidity, poor weather resistance, and susceptibility to copper damage. It exhibits post shrinkage and is prone to aging, brittleness, and deformation after demolding.
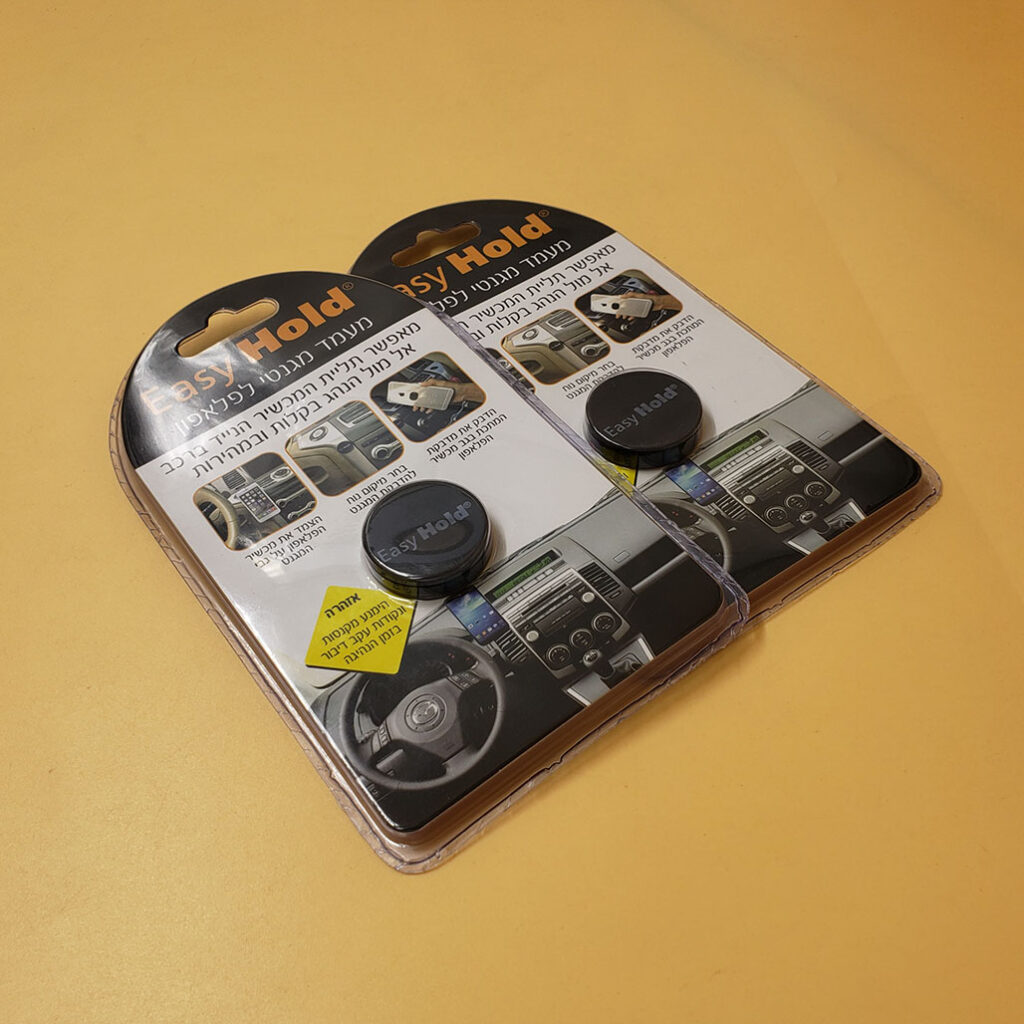
The color of materials is generally determined based on customer requirements, such as PANTON color codes, color drafts, color separation standards, etc., or rough colors can be specified by the customer and provided to the customer based on product inventory. If the customer has no requirements, colorless, transparent, and easiest to produce materials can generally be used.
If you order colored sheet materials, it usually needs to be at least 2 tons to be customized. Colored materials have a higher density than transparent materials. Flocking materials generally use PS materials with lower density. If the density is high, it is easy to produce a lack of fuzz on some surfaces after stretching.
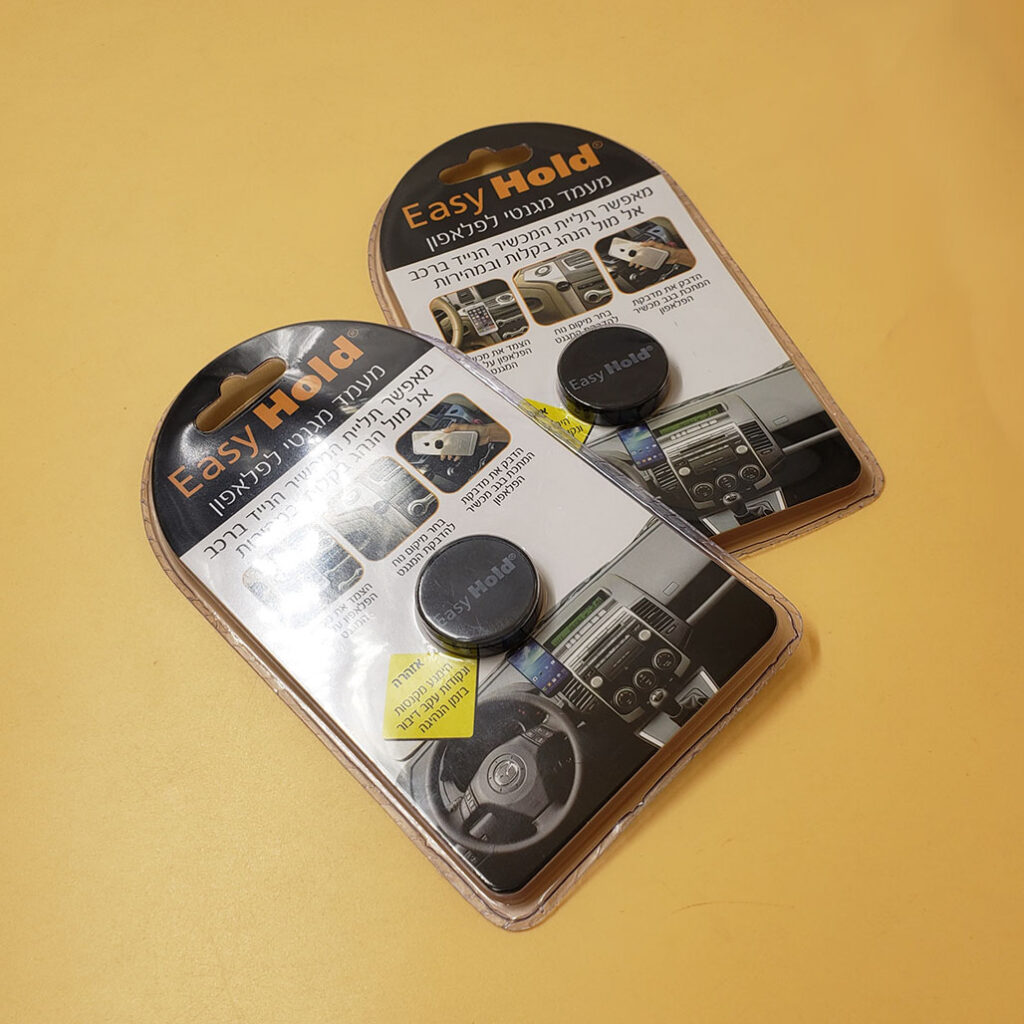
Generally, materials with bright colors are easier to produce and do not have high packaging requirements. Scratches on light colored materials are easily noticeable, and strict packaging requirements are required.

Generally, flocking materials need to be protected from scratches and indentations. When products are placed together, they are prone to friction and whitening in tight contact areas.
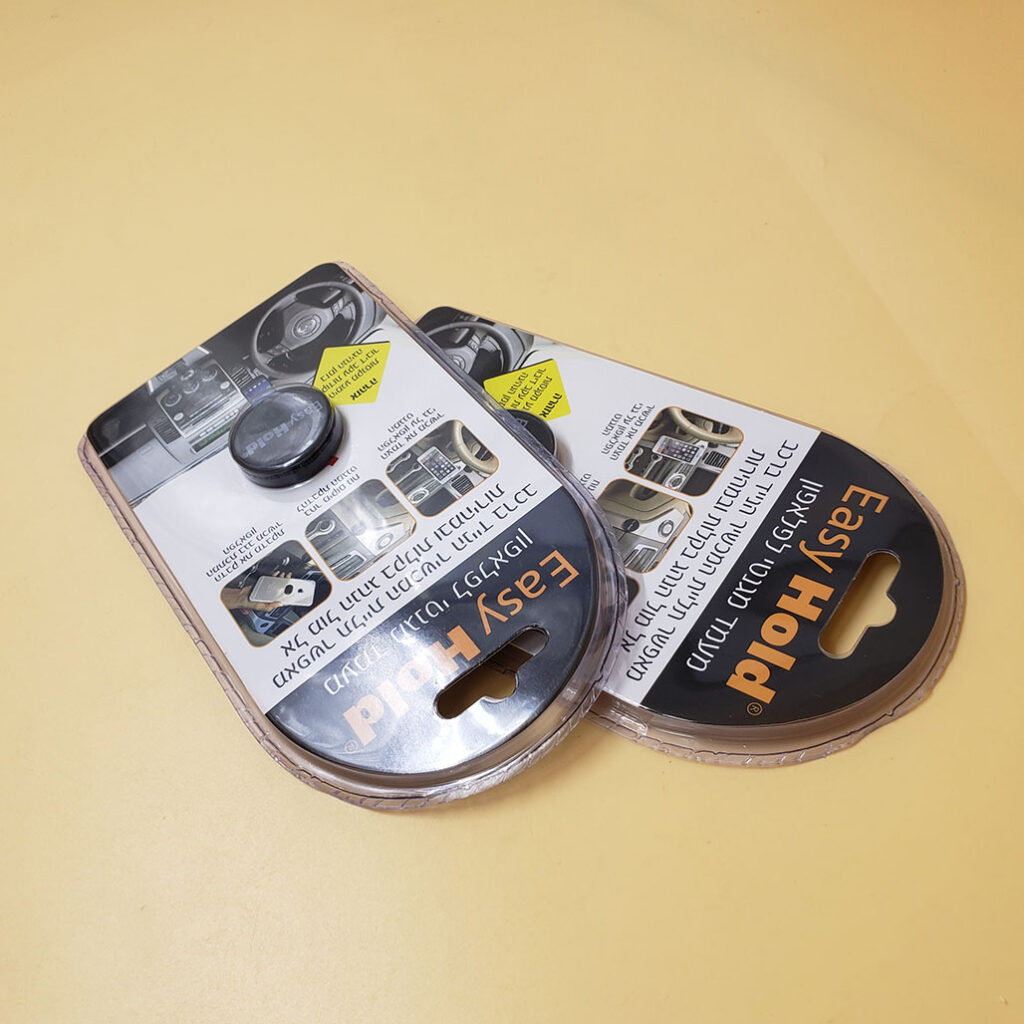
For places like this, special attention should be paid when packaging. If strict requirements are required, methods such as using plastic bags or separating copy paper should be considered for protection. Flocking materials are generally ordered based on length (meters).
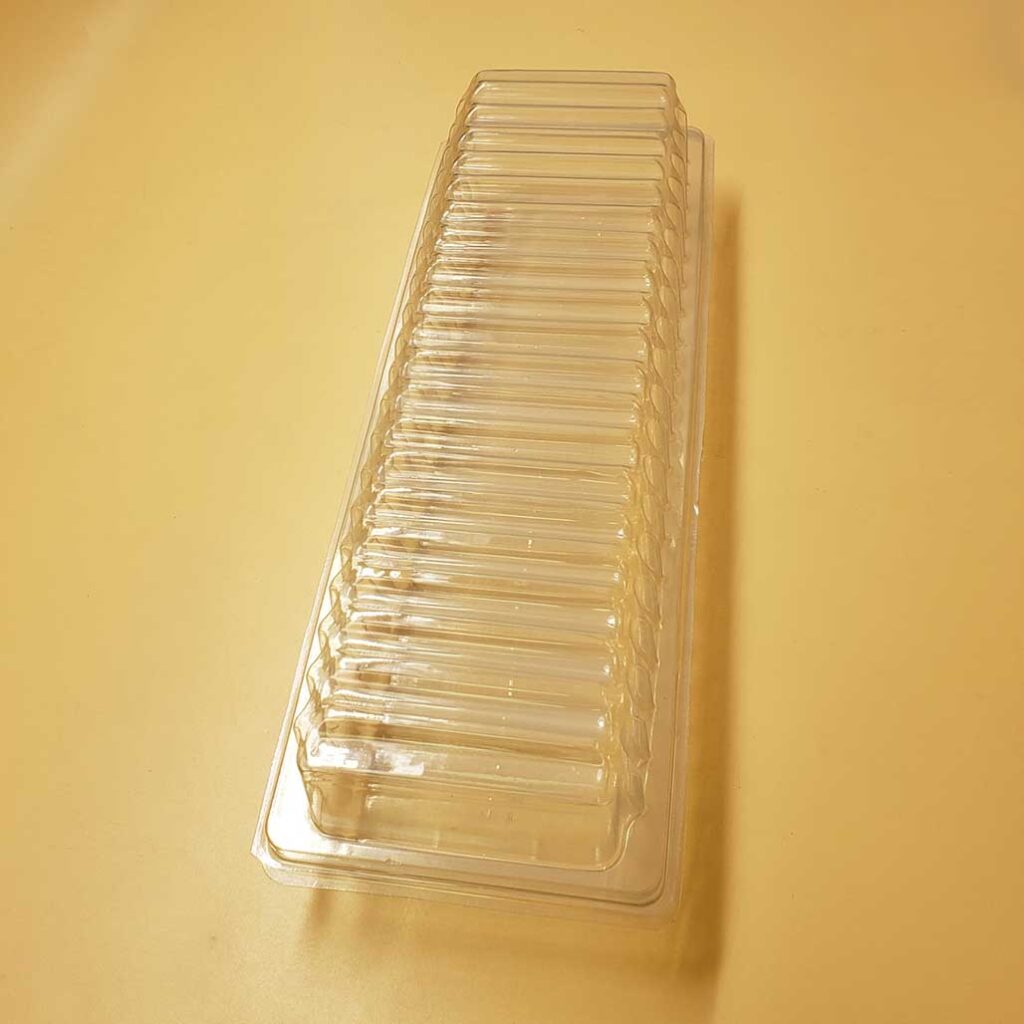