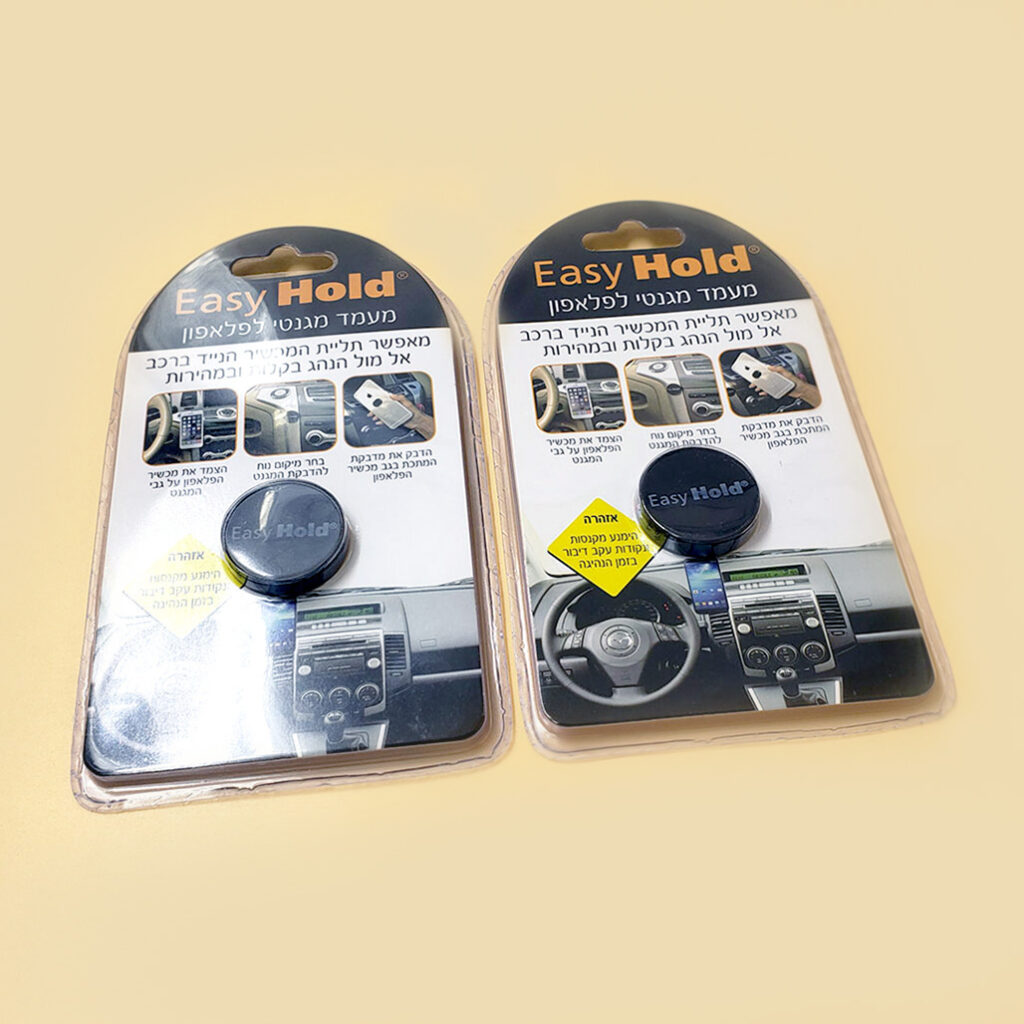
Phenomenon 1: Analysis of the causes of bubbling in the groove:
1 The temperature or pressure does not meet the requirements, resulting in false suction;
2. Insufficient glue amount, insufficient spraying amount, or glue leakage from the board;
3. Insufficient preheating (softening PVC film) or vacuum forming time (molding time);
4.After vacuum forming, remove the pressure before the temperature drops.
5. The heat resistance of the adhesive itself is insufficient.
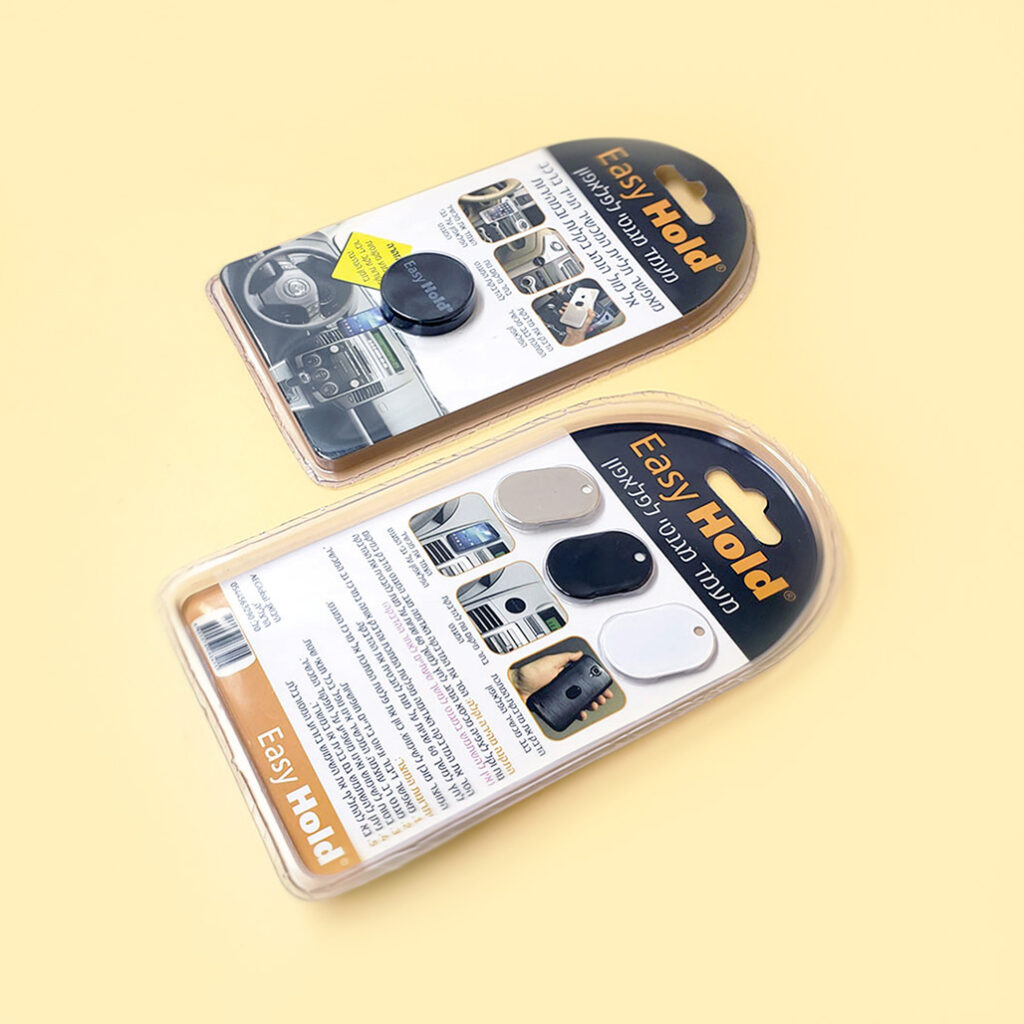
Solution:
1 Increase temperature or vacuum degree;
2. Increase the amount of glue applied and choose high-quality boards;
3. Increase preheating or forming time;
4.After vacuum forming, the temperature should be cooled to room temperature or slightly higher before withdrawing from the vacuum.
5. Use curing agent.
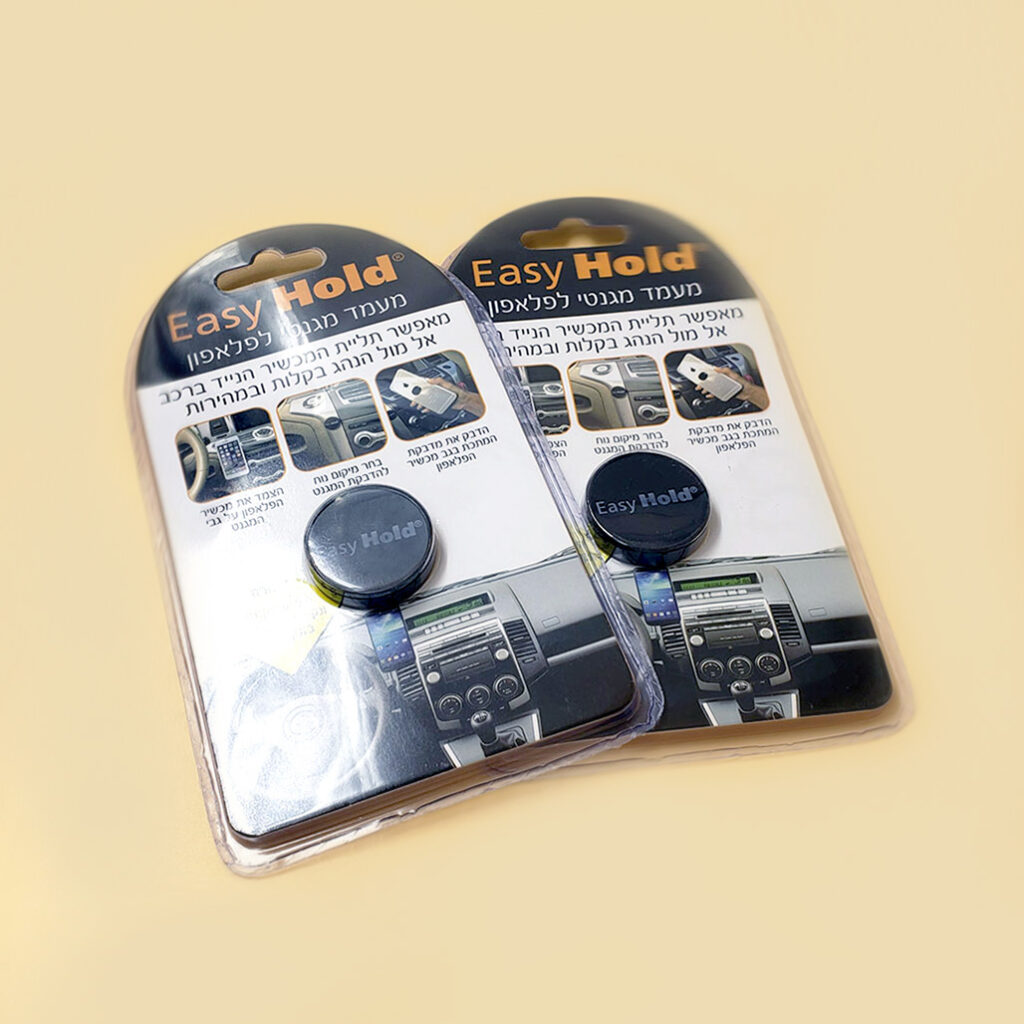
Phenomenon 2: Analysis of Local Bubbling Causes:
1 Uneven spraying of glue results in insufficient glue in certain areas, leading to a decrease in bonding strength;
2. The problem with PVC film is that it contains plasticizers, which are prone to migrate to the surface during aging or heating, affecting the bonding strength;
3. There is a problem with the heating tube inside the vacuum forming machine, causing uneven temperature.
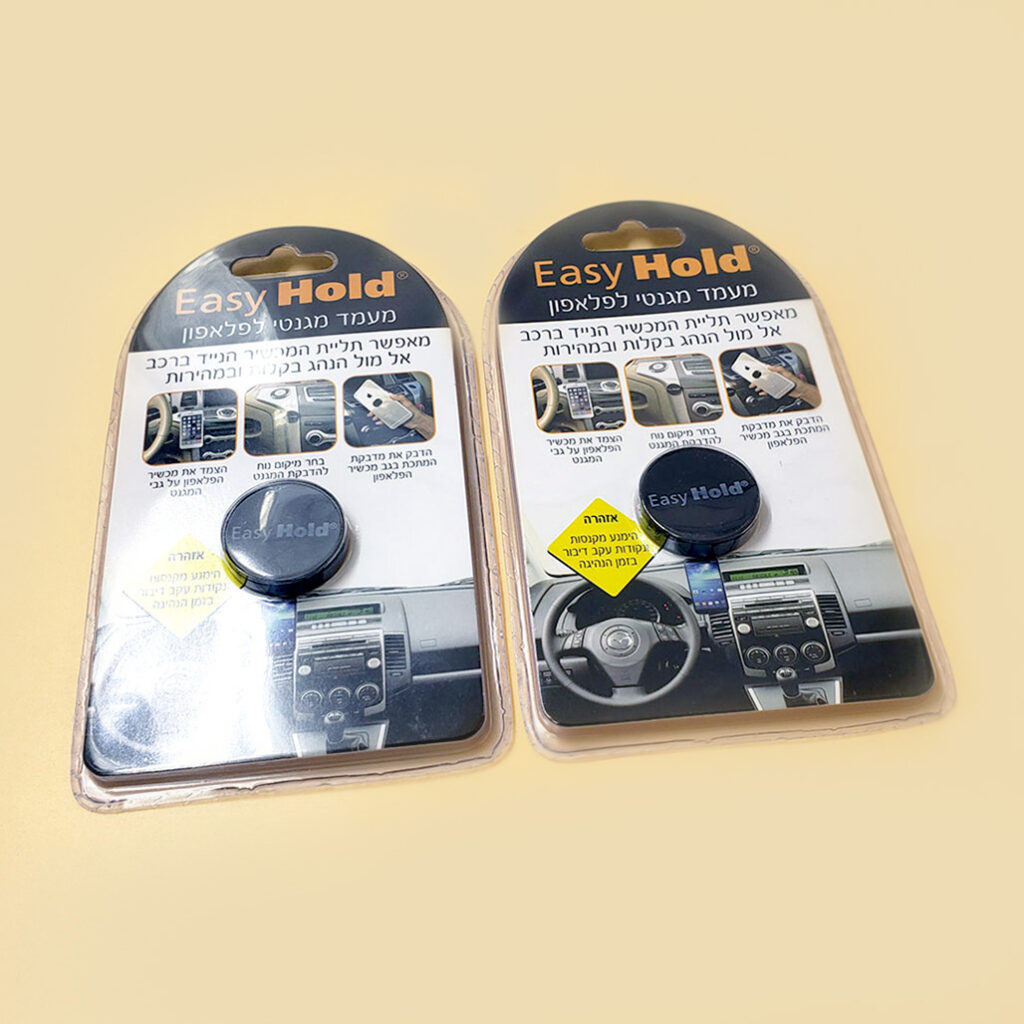
Solution:
1 Try to make the spraying amount uniform as much as possible; 2. Use high-quality PVC film; 3. Timely maintenance of equipment.
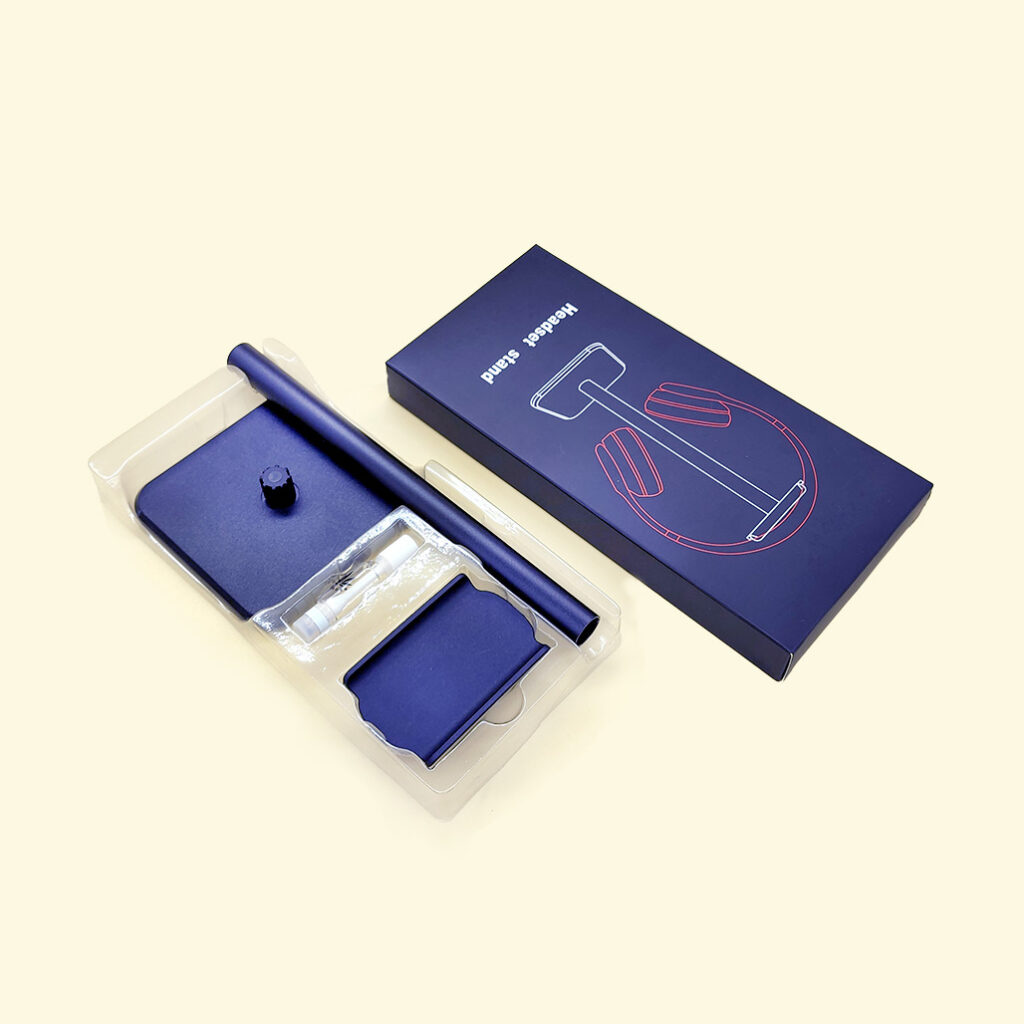
Phenomenon 3: Unable to absorb or shrink the edge.
Reason analysis:
1 When vacuum forming, the side temperature is too low or the vacuum degree is insufficient;
2. Insufficient temperature resistance of the adhesive;
3. After vacuum forming, remove the pressure before the temperature drops.
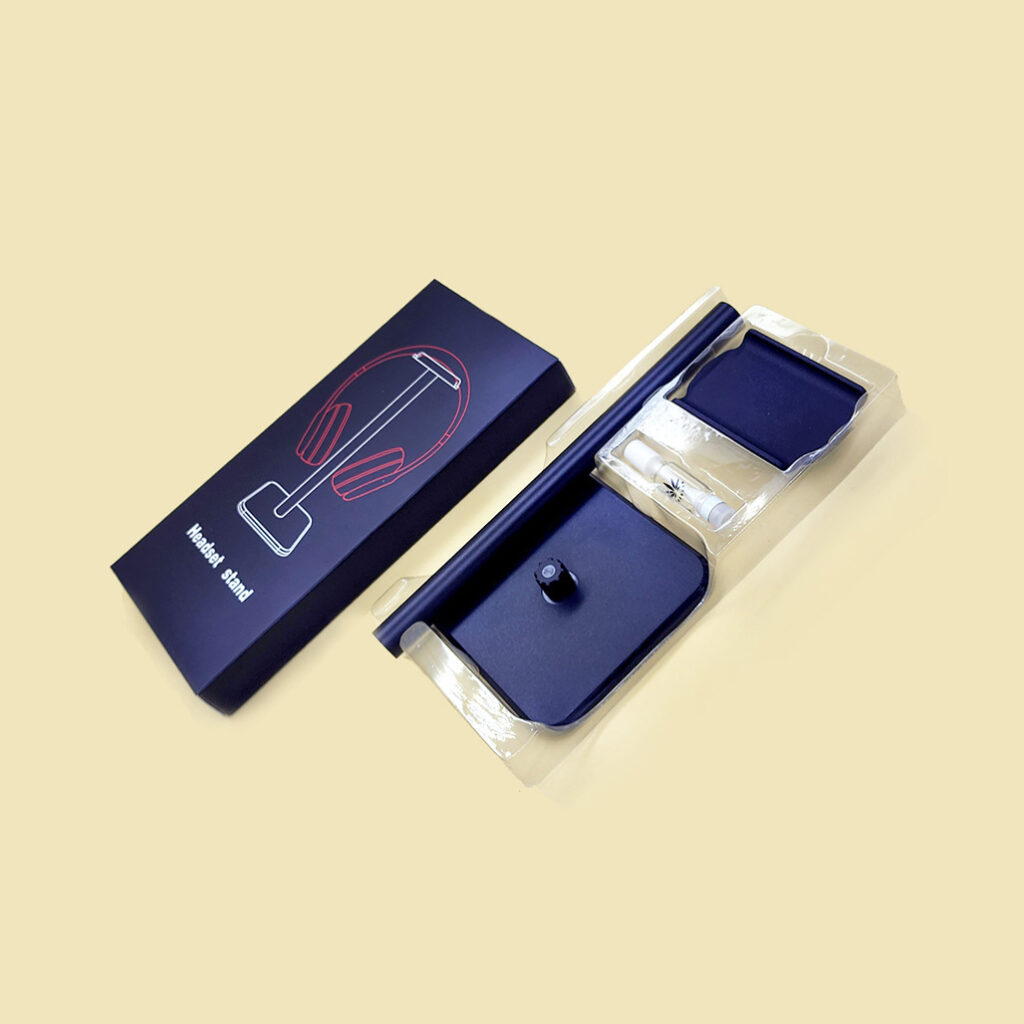
Solution:
1 Increase temperature or vacuum degree;
2. Use curing agent; After vacuum forming, the temperature should be cooled to room temperature or slightly higher before withdrawing from the vacuum.
Phenomenon 4: The surface of the product produced by vacuum forming has pockmarks.
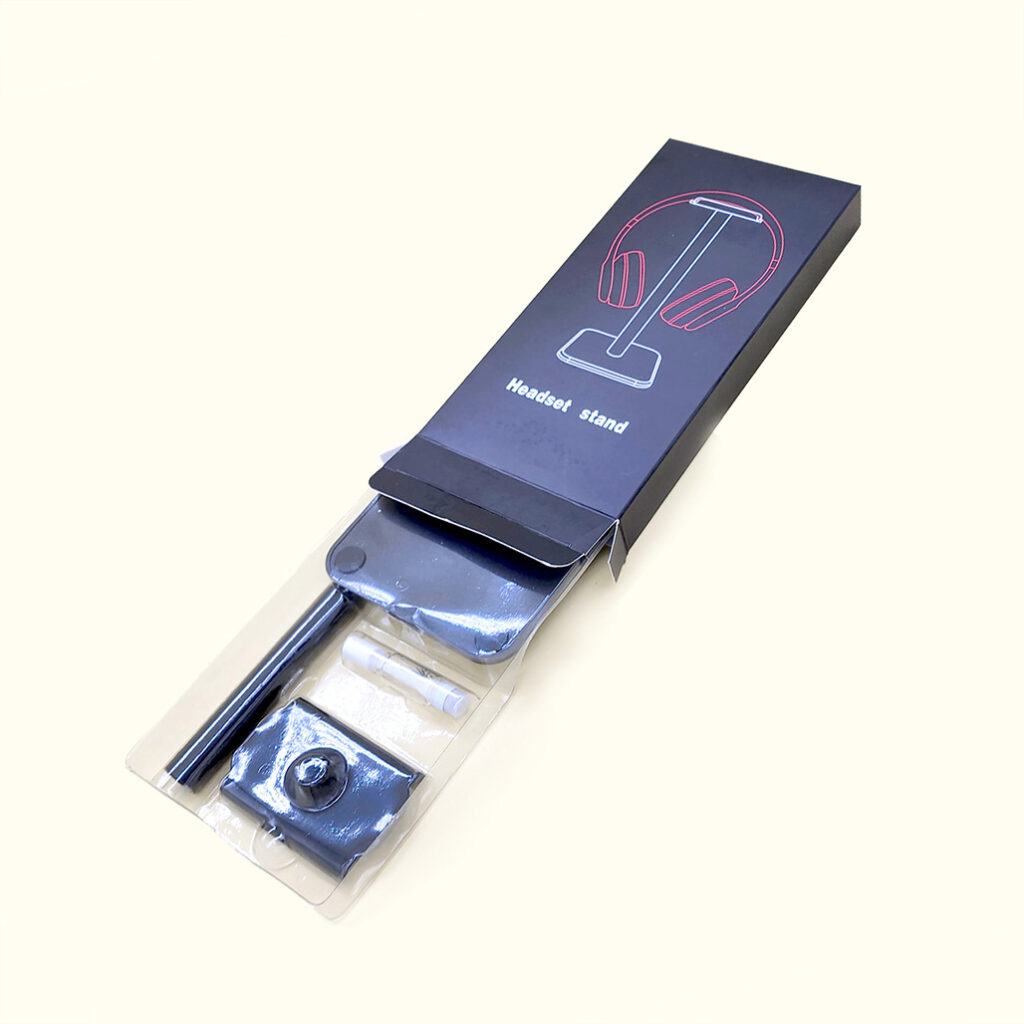
Reason analysis:
1 The particle size of the glue is large, and using thin PVC film can easily produce pitting, which is characterized by uniform dispersion;
2.When using the curing agent, the curing agent is not completely dispersed;
3. The surface of the board is not cleaned thoroughly, or after spraying glue, there is a lot of dust in the workshop, which sticks to it. These rough spots are unevenly dispersed and of different sizes;
4. The viscosity of the glue is too high and the dispersion is uneven;
5. If the viscosity of the glue is too low or the solid content is low, it can cause the board to become fuzzy, and such rough spots usually appear at the edges and corners of the grooves, forming blocks.
6. The air pressure of the spray gun is insufficient, resulting in poor atomization.
7. The glue is not filtered (this situation refers to the situation where a bucket of glue is used to the end, and if there is dirt or film formation inside, a filter screen should be used to filter it).
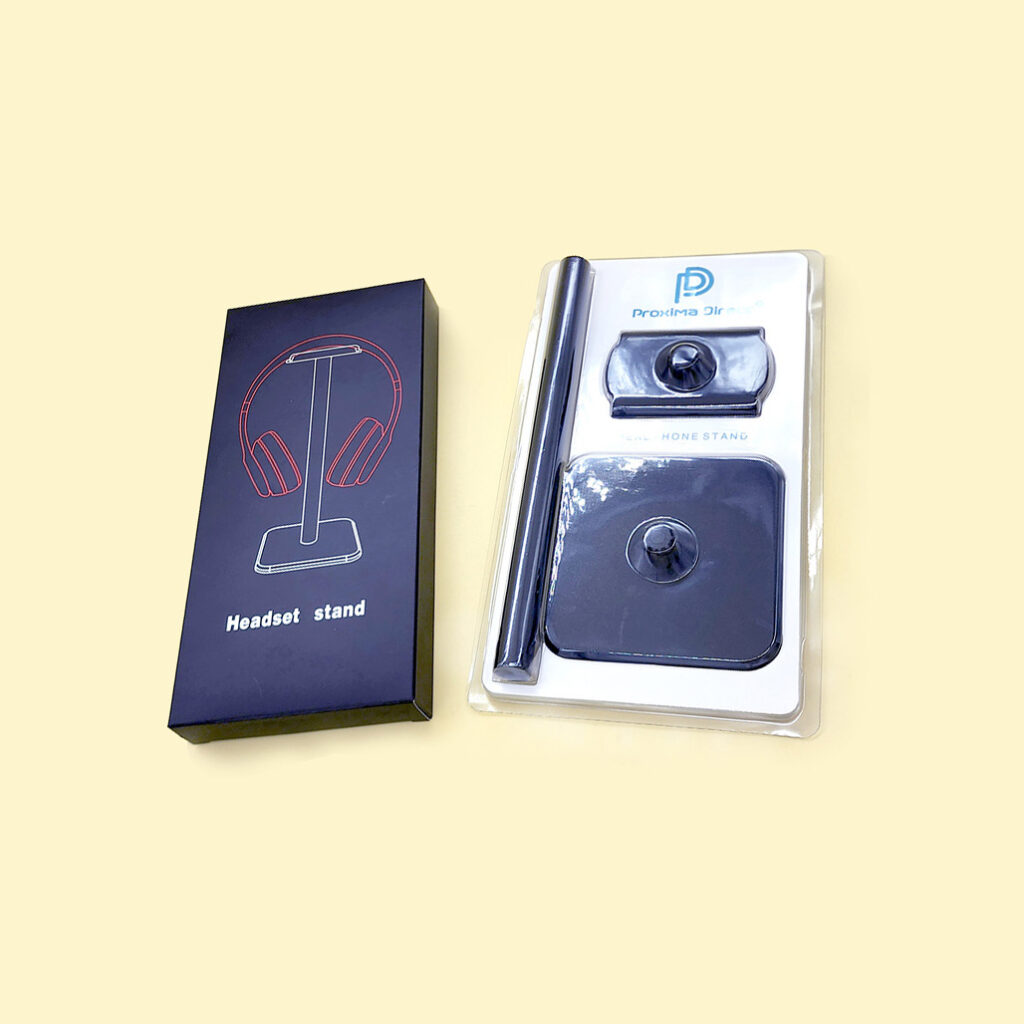
Solution:
1 Choose adhesive with smaller particle size;
2.When preparing the curing agent, extend the stirring time to ensure complete dispersion of the curing agent;
3. Clean the surface of the board before spraying, and separate the spraying workshop separately;
4. Choose glue with appropriate viscosity or glue with high solid content;
5. After the glue dries, it can be sanded with fine sandpaper; 6. Increase the vacuum degree and adjust the atomization effect;
7. When using, filter with a filter.
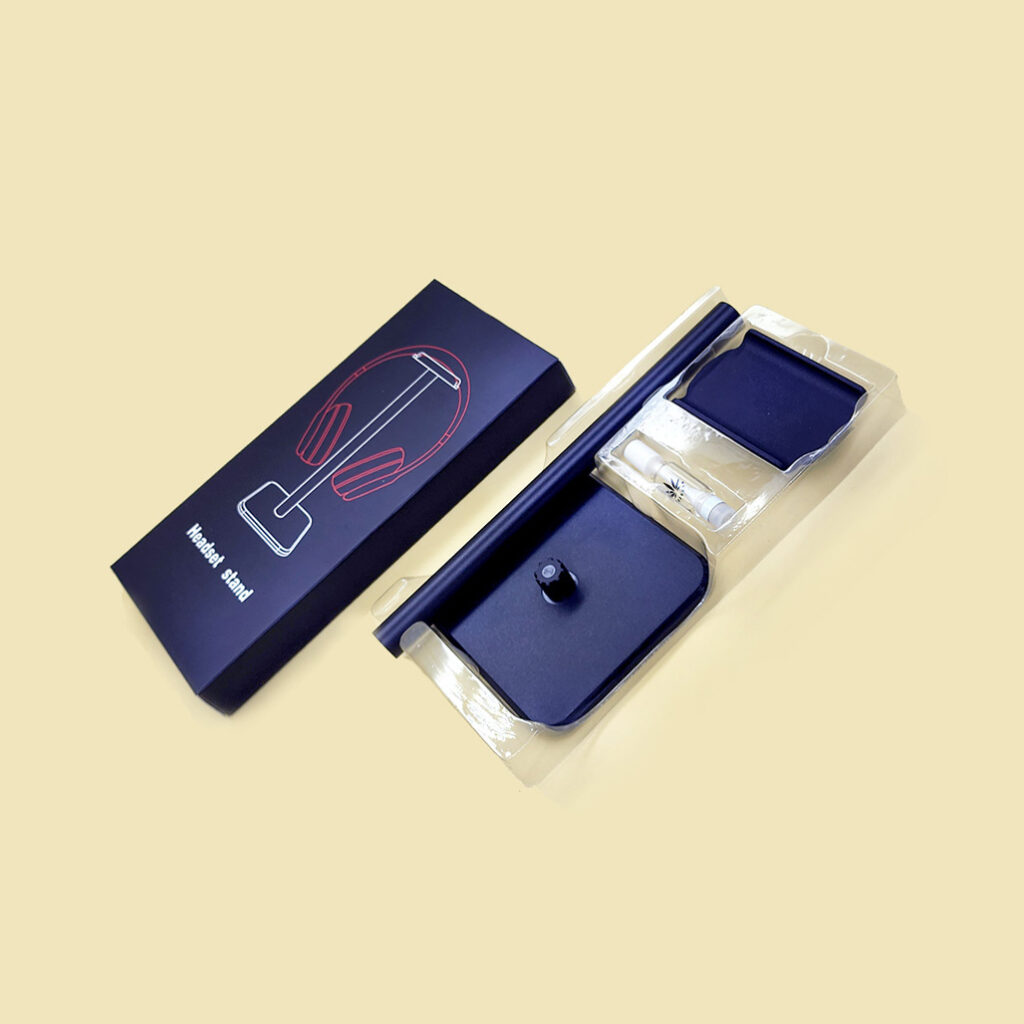
Phenomenon 5: Analysis of the causes of local orange peel production:
1 Excessive spraying of local adhesive;
2. The surface of the board is contaminated with oil, causing shrinkage of the adhesive;
3. The curing agent is not completely dispersed, resulting in shrinkage.
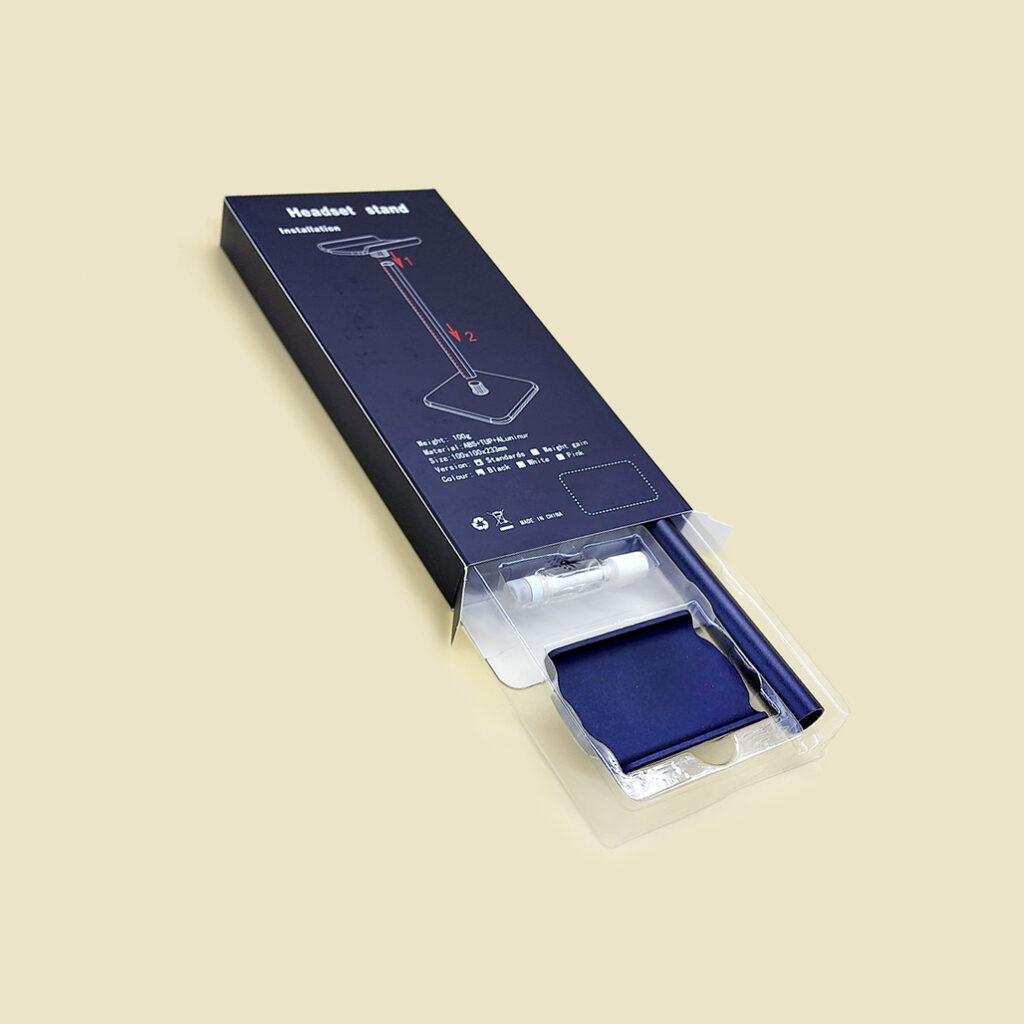
Solution:
1 Spray glue evenly and appropriately;
2. Keep the surface of the board clean;
3. Stir the curing agent thoroughly to disperse it evenly.
Phenomenon 6: Analysis of Wrinkle Causes:
1 The spacing between narrow and long workpieces is too small; 2. The edges and corners around the upper surface of the pad are not chamfered;
3. The distance between the workpiece in both horizontal and vertical directions is not on a straight line, which increases the resistance to air flow;
4. The set temperature is too high;
5. The time to reach the set pressure is too long.
Phenomenon 7: Analysis of Reasons for PVC Surface Whitening:
1 The set temperature is too high;
2. The time to reach the set pressure is too long;
3. The line type is not suitable.

Phenomenon 8: Analysis of the reasons for the edge not being firmly adhered:
1 The quality of the adhesive is poor;
2. The activation temperature of the adhesive is too high;
3. The temperature of the equipment cannot reach the activation temperature required for the edge of the workpiece; 4. The workpiece pad is not suitable;
5. Poor or no PVC backing performance;
6. The adhesive has expired or does not meet the storage requirements;
7. Leakage of glue or improper glue spraying method.

Phenomenon 9: Edge and corner breakage are common problems, such as high or low temperature, time or duration issues. Adjusting the temperature and time will improve.
When there is a quality problem with PVC vacuum formed film, the process or parameters should be adjusted item by item based on the above reasons and recorded.
It is important to avoid adjusting multiple process parameters or processes at the same time, otherwise the true cause of the quality problem will be difficult to identify, and it will also be difficult to establish and adjust process standards for the production environment to provide objective basis.
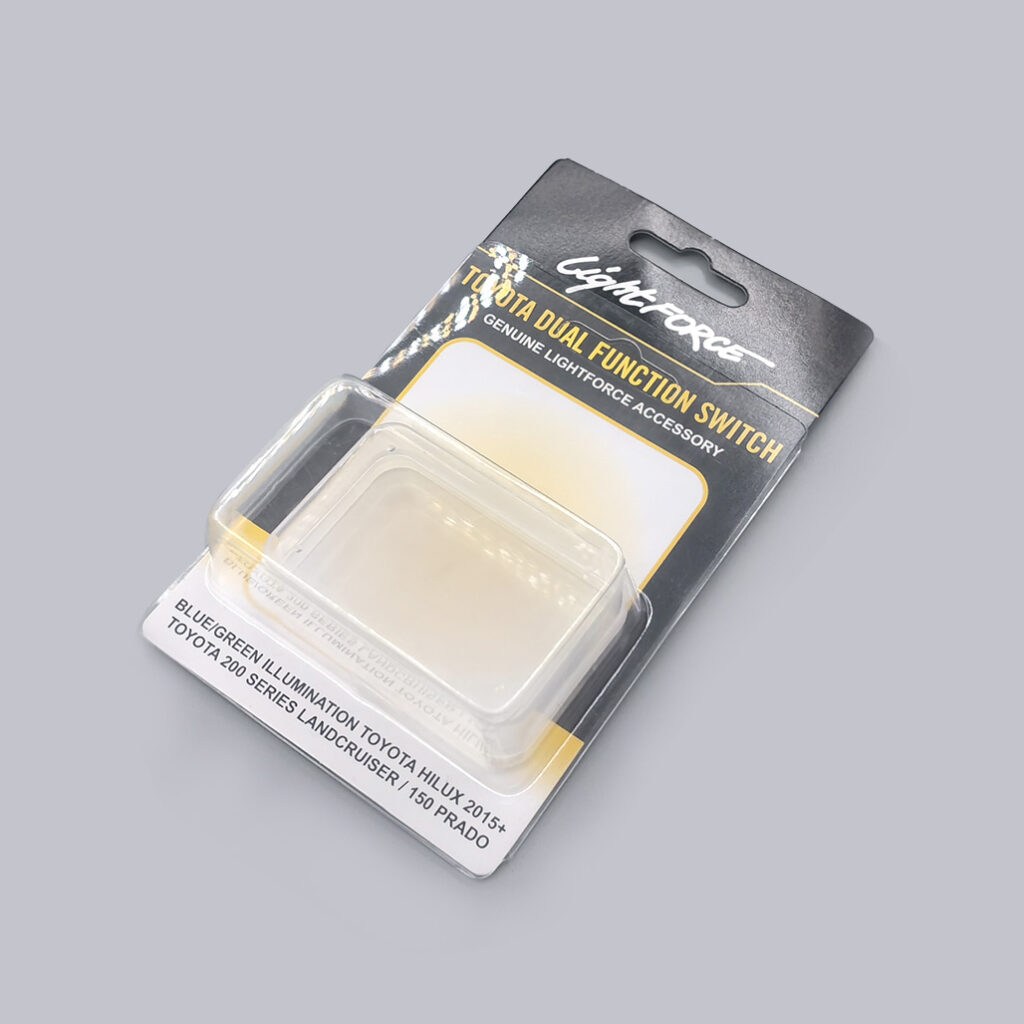
Phenomenon 10: Analysis of Reasons for Poor Adsorption: 1 The coating is too thin and uneven;
- The printing substrate is rough and has too strong absorption;
- The vacuum forming oil is too thin and the vacuum forming force is insufficient;
- Insufficient temperature during heating and sealing;
- Crystallization effect of ink layer;
- The vacuum formed oil has deteriorated due to prolonged storage time.

Solution:
1 Adjust the roller and coating amount;
- Replace the printing substrate or apply primer first;
- Replace the vacuum forming oil or increase the coating amount;
- Increase the temperature during welding sealing;
- Before applying vacuum forming oil, wipe the surface of the printed material or dilute it with 5% lactic acid;
- Replace the vacuum formed oil.
