01

Overview of vacuum molding process
Vacuum forming technology is one of the most commonly used forming methods in plastic packaging, which is a forming technology that uses thermoplastic sheets as the forming object.
The vacuum molding process was developed in the early 20th century, but its application in industrial production was only after the 1940s, and it only had significant development in the 1960s. Through continuous development and change, the vacuum forming process has achieved high automation and mechanization, and the generation of waste materials is also decreasing.
In the past decade, we have continuously improved our vacuum molding equipment, improved the temperature control and transmission methods of vacuum molding machines, and solved the technical problems of high tensile and high-precision vacuum molding products. Especially for PET products, their high tensile, high transparency, high uniformity, high impact resistance, and high precision have been improved. At the same time, we have overcome the technical difficulties of vacuum molding 0-degree demolding and expanded the application fields of vacuum molding technology. In the development of materials with high and low temperature resistance, the problem of vacuum molded pallets in high and low temperature environments has been solved

Vacuum forming process is a method of film hot forming, which involves passing thermoplastic masterbatch through a film extruder to produce thermoplastic sheets. Plastic sheets are used as raw materials for vacuum molded products. After heating and softening, they are deformed and attached to the pre made mold contour surface using the pressure difference or mechanical pressure on both sides of the sheet. They are cooled and shaped by air or cooling media, and then cut and trimmed to complete the process of vacuum molded products.
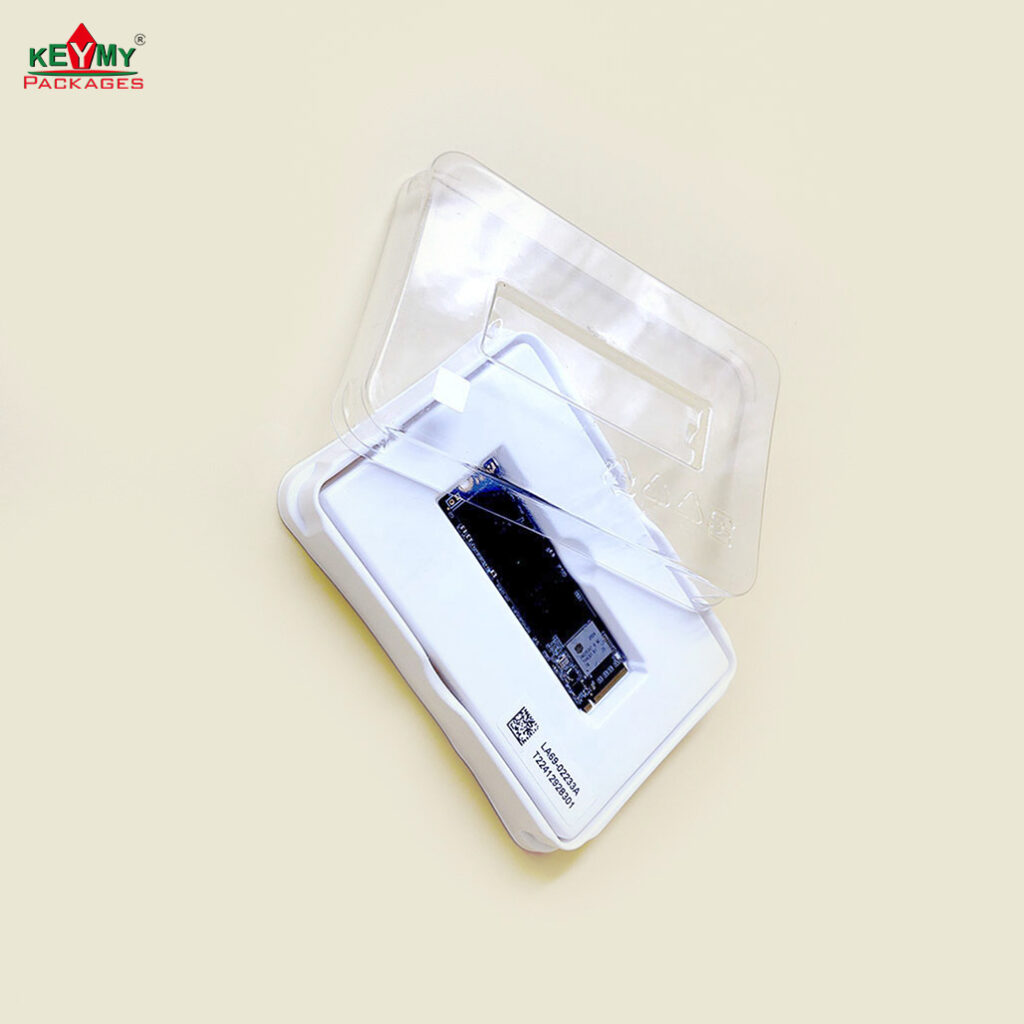
Classification of vacuum molding equipment
After years of evolution and improvement, vacuum molding machines are mainly divided into three types based on different pressurization methods. Firstly, vacuum negative pressure vacuum molding machines mainly use negative pressure suction to make the film adhere to the mold. 2、 Positive pressure suction molding machine uses an air compressor to increase air pressure on the front of the film, allowing the softened film to adhere to the mold. 3、 Positive and negative pressure suction molding machine is a method of shaping softened film by creating a strong pressure difference on both sides of the film through pressurization and vacuum pumping. These three devices each have their own advantages and disadvantages, and the machine needs to be selected based on the characteristics of the product.
There are two types of molding machines. One step molding machines integrate film heating, vacuum forming, and die-cutting processing, with high production efficiency and suitable for vacuum molded products with low quality requirements; The two-step molding machine separates the film heating, vacuum forming process, and die-cutting processing, making it suitable for vacuum forming products with high quality requirements.
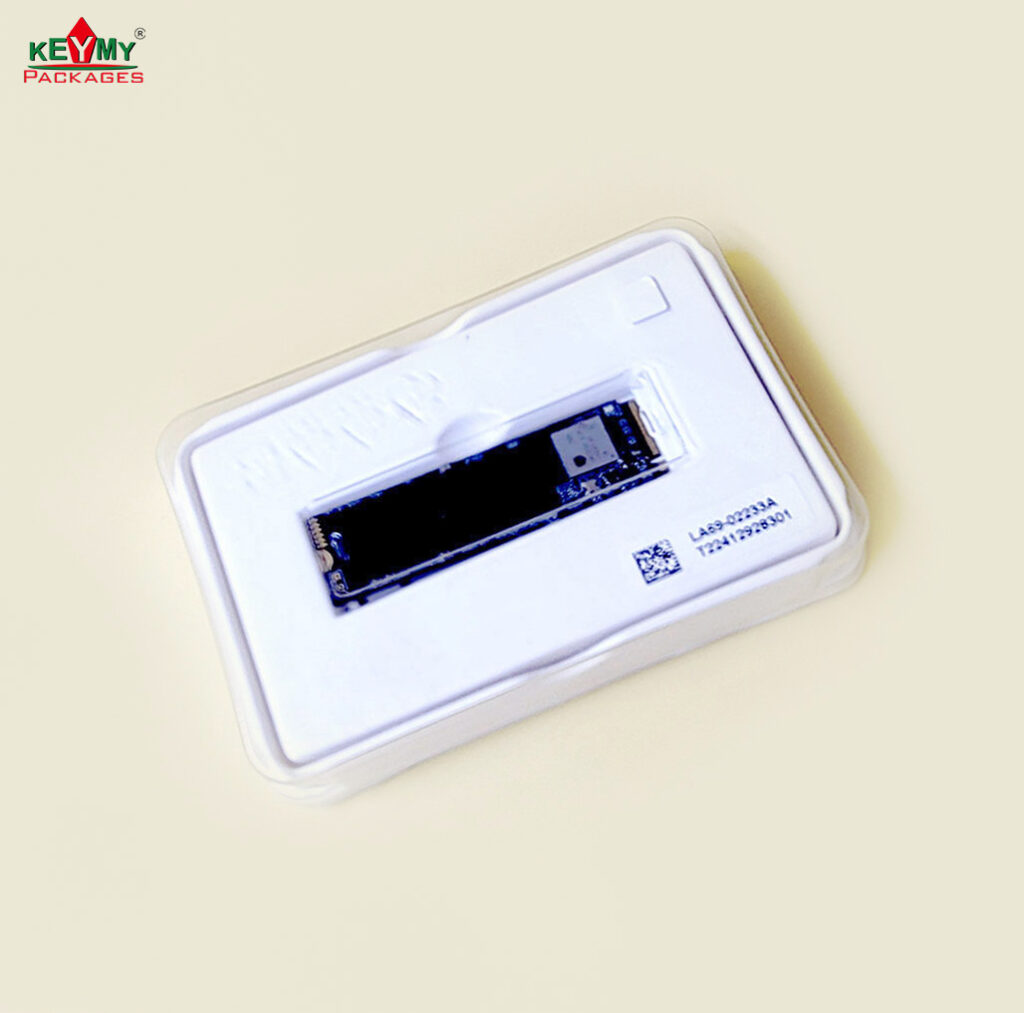

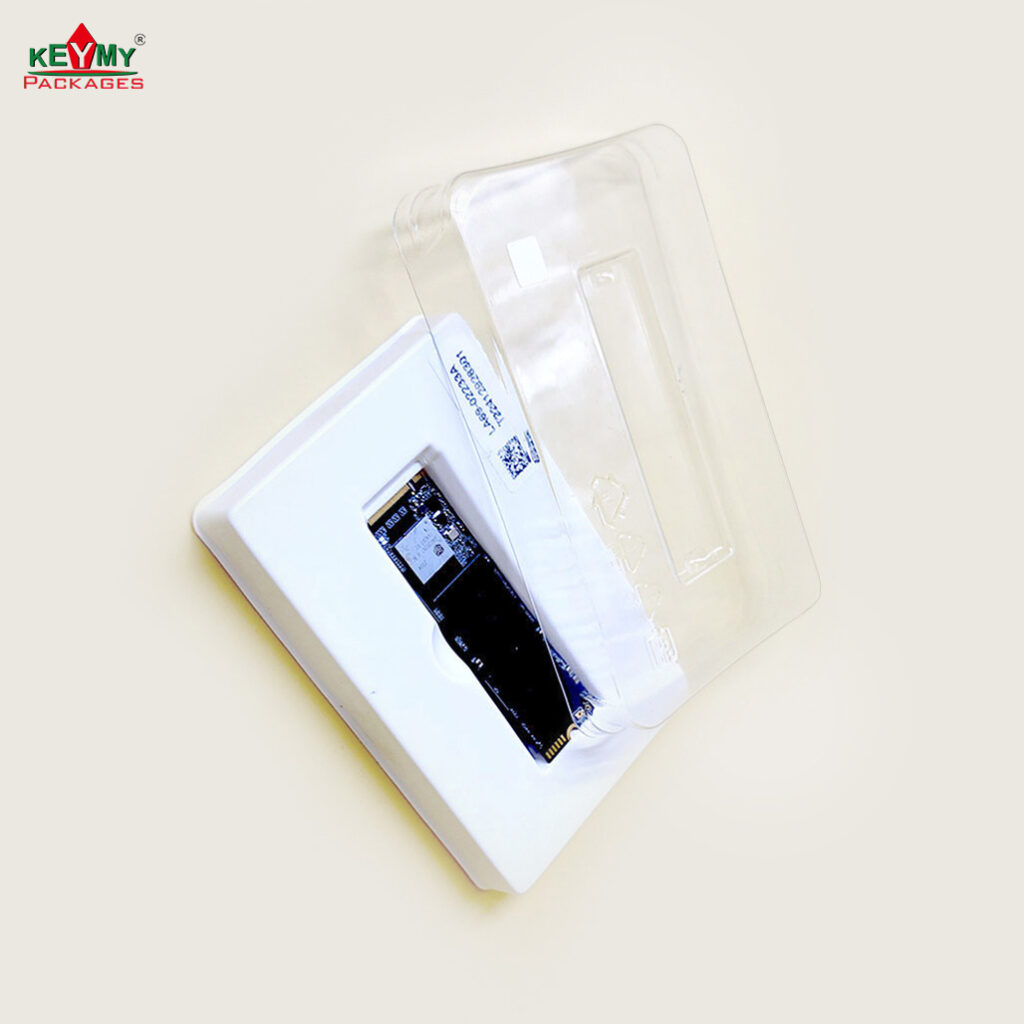