- Blistering: A plastic processing technology that mainly involves heating flat plastic hard sheets to soften them, using vacuum adsorption on the surface of the mold, cooling them, and forming them.
- Blister shell: Using vacuum molding technology, transparent plastic hard sheets are made into transparent plastic with specific raised shapes, which is covered on the surface of the product to protect and beautify it.
- Vacuum tray: also known as plastic inner tray, uses vacuum molding technology to make plastic hard sheets into specific grooves of plastic, and places the product in the grooves to protect and beautify the product
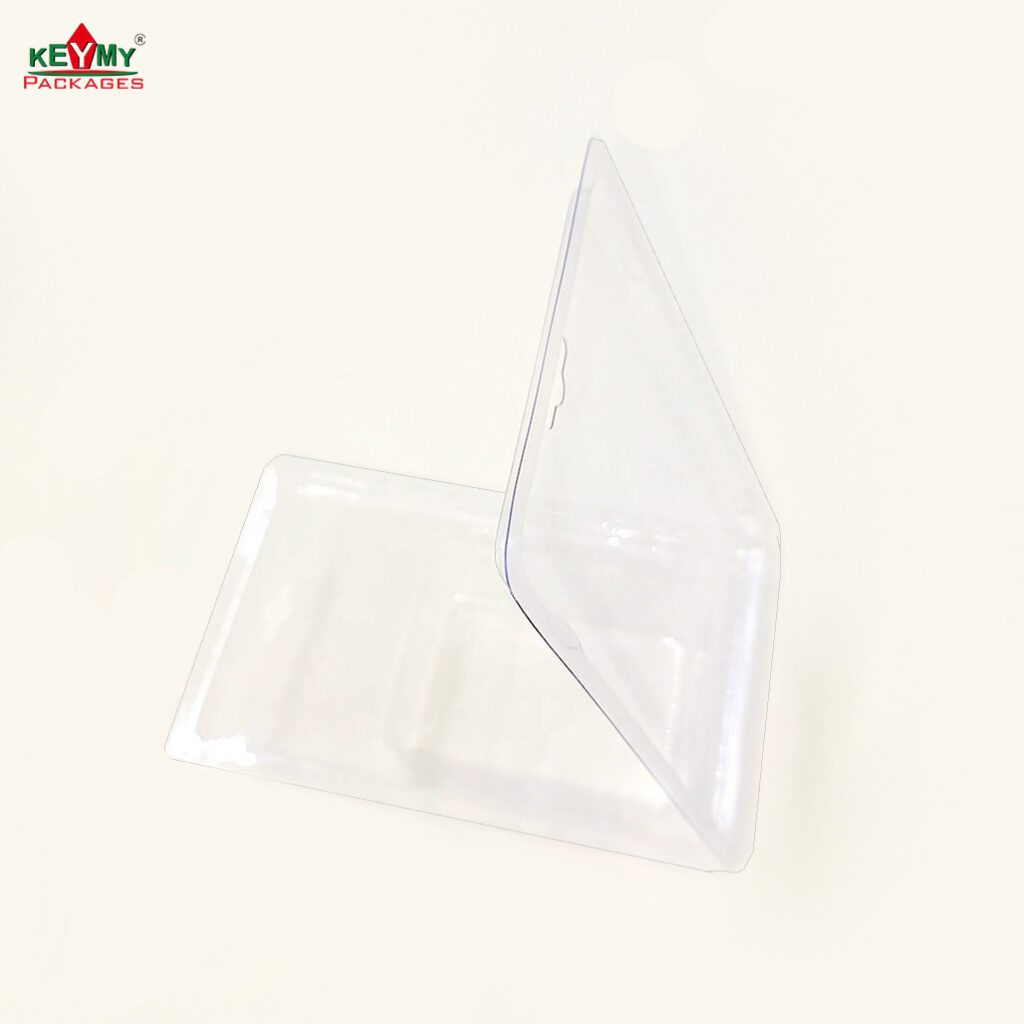
- Flocking blister: It is a type of blister tray made of special materials, which glues a layer of plush material on the surface of ordinary plastic hard sheets, giving the tray a plush texture and improving the quality of packaging products.
- Vacuum forming: It is commonly known as vacuum forming, which uses a vacuum forming machine to adsorb the heated and softened plastic hard sheets onto the surface of the mold, and after cooling, form a concave convex shaped plastic.
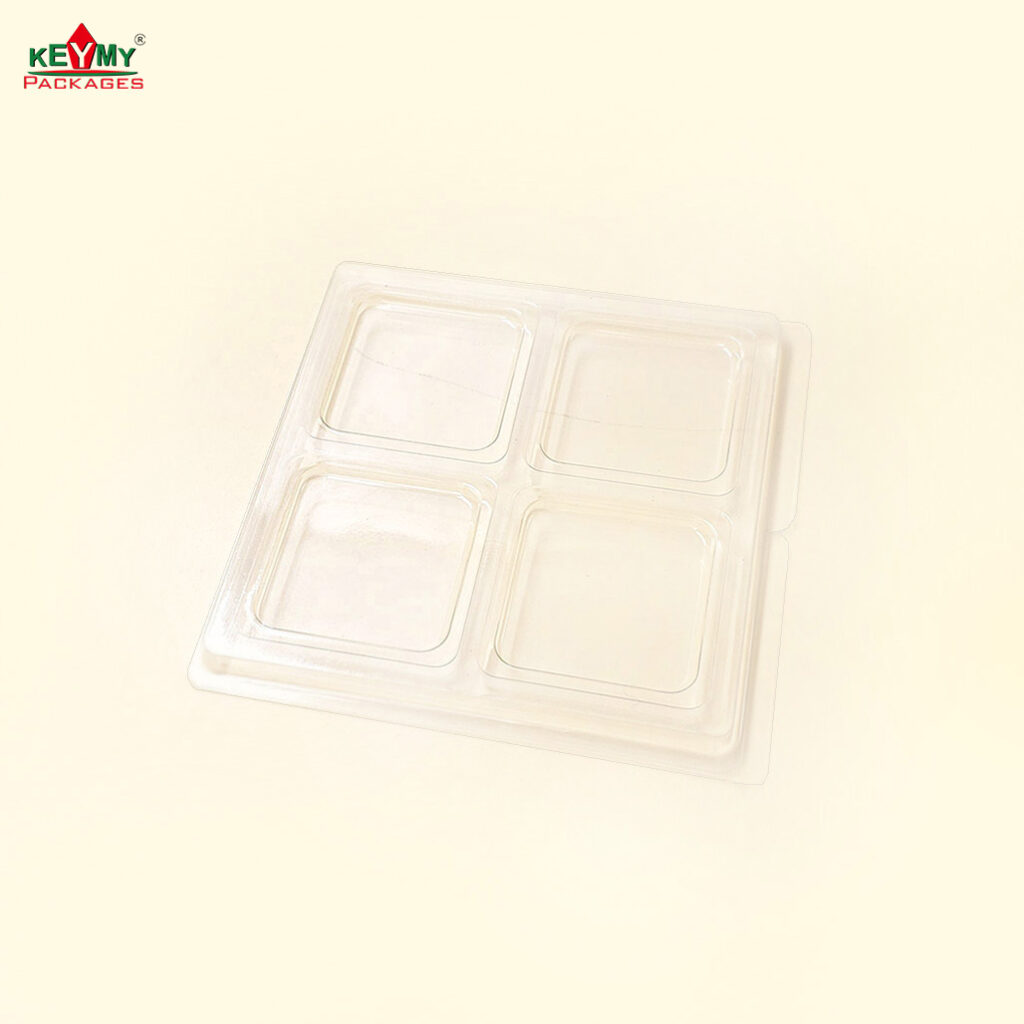
- Vacuum cutting: After vacuum forming, plastic products are cut into individual pieces using a punching machine to cut large sheets of material into individual products.
- Blister Folding: There is a type of blister packaging called card insertion packaging, which requires folding the three edges of the blister to the back using a folding machine, so that in the next packaging process, the paper card can be inserted into the folding edge to form a card insertion packaging.
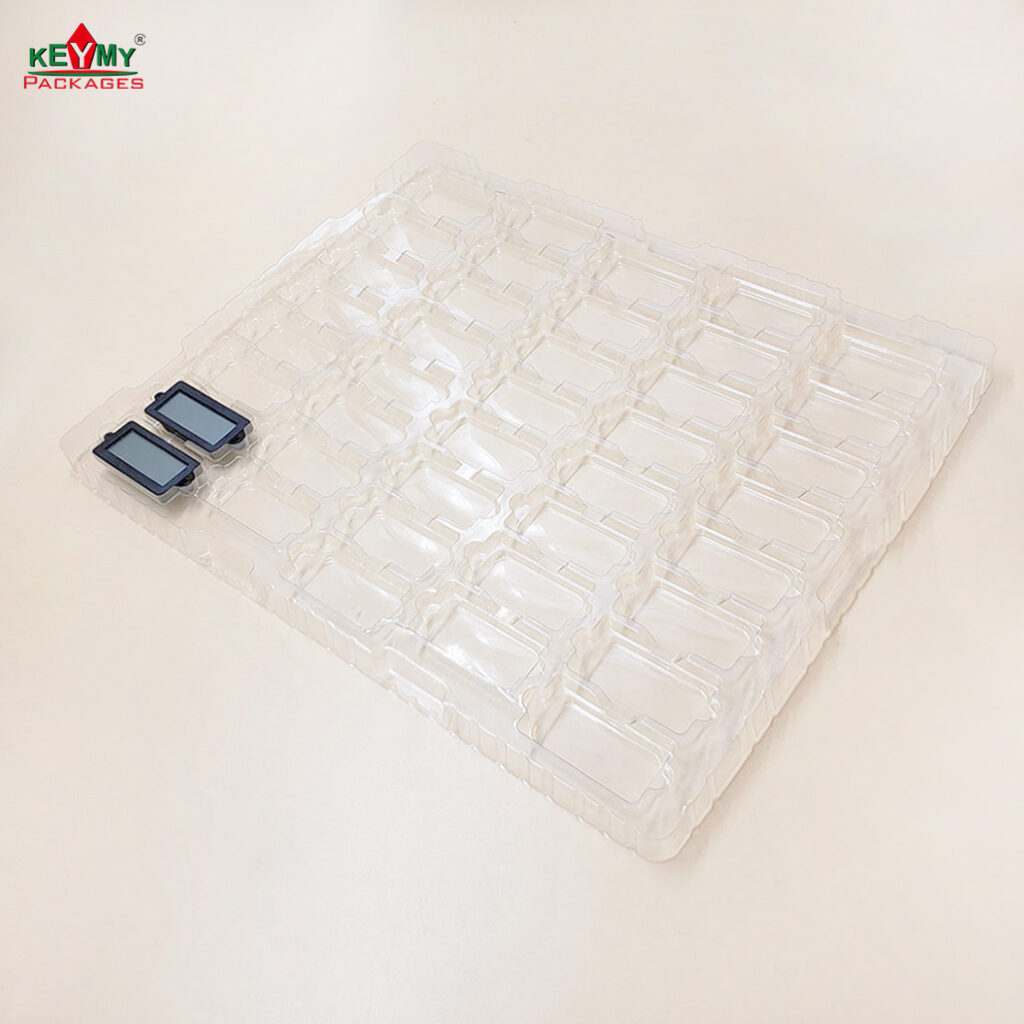
- Vacuum sealing: It is a vacuum sealing process that uses a sealing machine to heat seal paper cards coated with vacuum oil and bubble shells together to form vacuum packaging, also known as paper plastic single-sided hot pressing.
- High frequency blister sealing: It is a blister packaging process that uses a high-frequency machine to generate high frequencies and bond the blister shells together to form a double blister shell packaging, also known as high-frequency double-sided heat sealing.
- The relevant molds for the blister cover (bubble shell) are mainly made of yellow blister hand board gypsum powder. If drawings are provided, the stone sound material is processed by milling machine and hand to complete the mold production according to the drawing data and requirements; If a physical object is provided, first use manual mud to complete the contour of the mold, vacuum form it into a true hollow cover, then reproduce the stone sound mold, and modify the mold: it takes about 2-4 days to complete: gypsum mold is easy to make, and the time is short, which is conducive to modifying the product packaging. The price is lower, but the durability is lower.
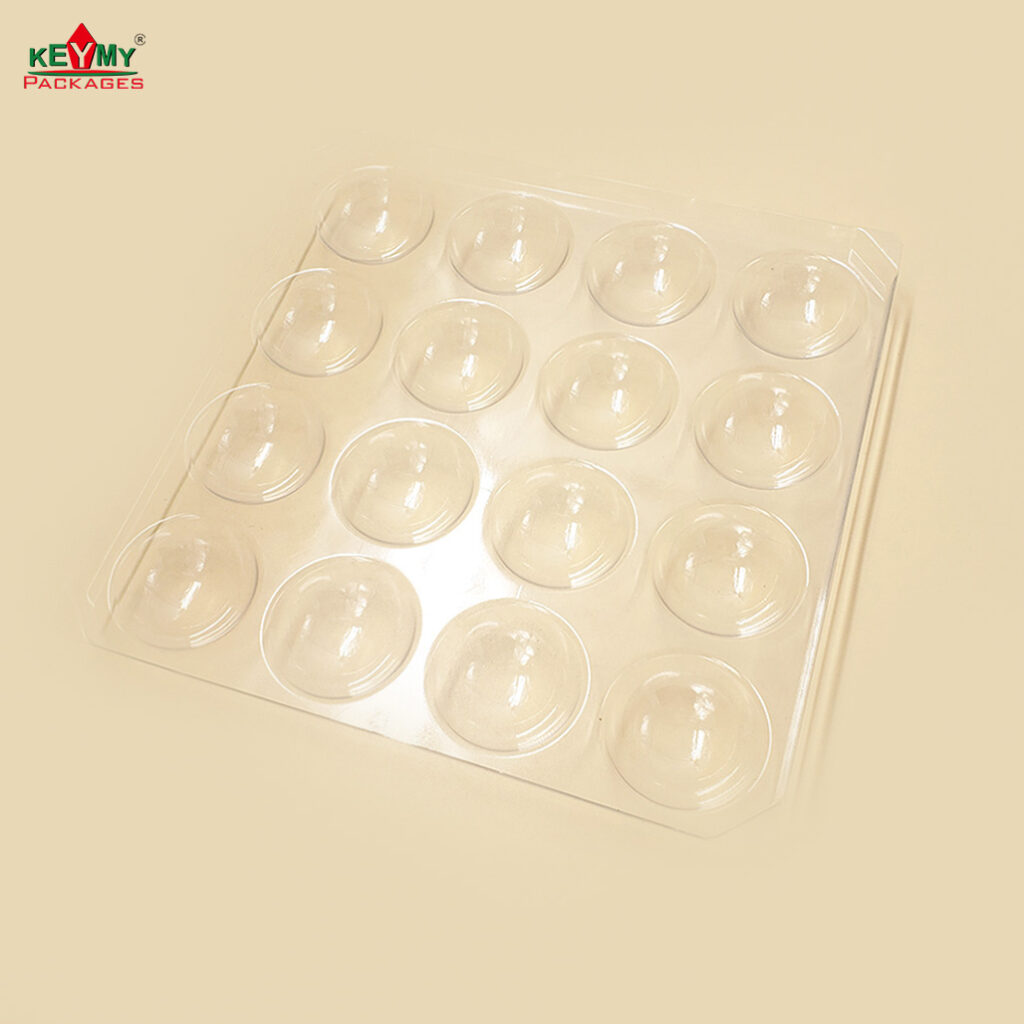
- After a period of use, it is more prone to damage, and the transparency of the produced product is poor; Mainly suitable for products with low requirements for first board confirmation and outer packaging transparency. Rubber molds are usually made according to product design requirements, and then a gypsum mold is used to produce a vacuum cover. Special high-temperature resistant resin materials are injected into the vacuum cover, and after the mold is completely dry, drilling is carried out and completed; Approximately 3-5 days required: Resin molds are more expensive than copper molds and stone palace tools, but their usage level is comparable to copper molds and they are more durable. They can solve some technical problems that copper molds and gypsum molds cannot handle, such as water marks on the product wall. Using such tools can have better results; Mainly, it is suitable for products that meet the requirements of electronics, toys, pharmaceuticals, food, and automotive boutiques.
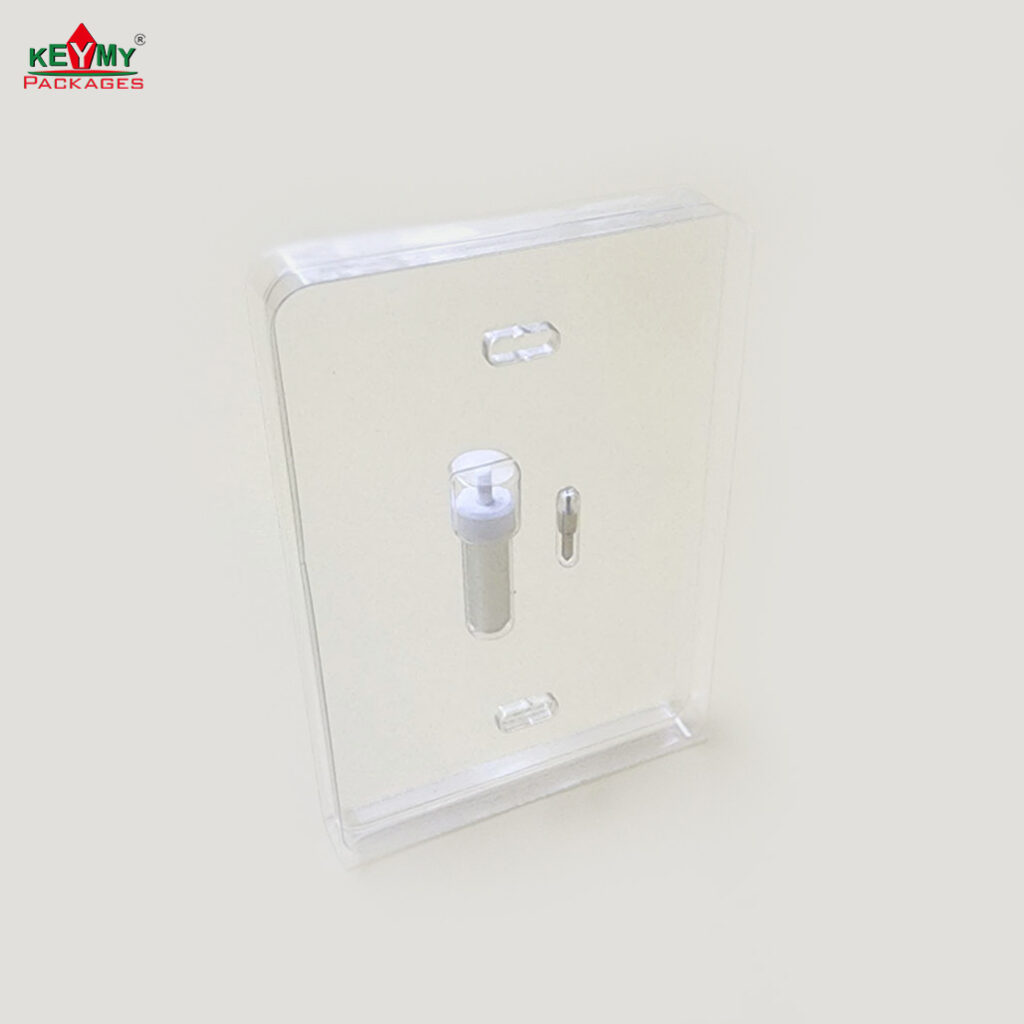