
2 Operating procedures

2.1 Requirements for the use of suction plastics
Absorbent plastic is a two-component adhesive with an activation temperature of around 60 degrees. The storage environment temperature must be between 5 ℃ and 30 ℃, and temperatures below 5 ℃ can cause flocculation. The rubber bucket should not be placed directly on the ground, but on wooden brackets, especially in winter. The validity period of the suction plastic is 6 months from the date of leaving the factory, without opening the original packaging.

The ratio of the main agent to the curing agent is 20:1. When mixing the main agent with the curing agent, the main agent should be kept in a stirring state. The curing agent should be slowly added and stirred for at least 3 minutes. The amount of glue prepared each time should be ensured to be used up within 4 hours. After mixing the glue, the glue bucket should be tightly covered.

2.2 Gluing process requirements:
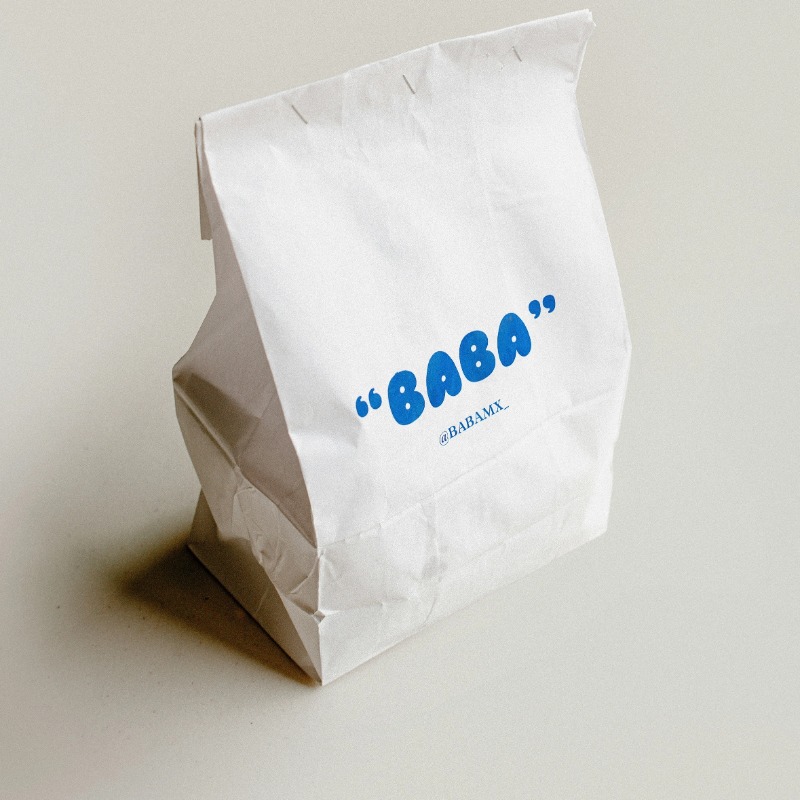
2.2.1 The spraying sequence is end face – front line – front+line – end face, and the flat part can be sprayed once; Two coats of spray are required at the end face and flat line.

The activity time after mixing the main agent and curing agent is 4-6 hours. The workpiece that has been sprayed with glue should be processed within 4 hours to achieve the best bonding effect. Otherwise, due to the cross-linking reaction of the adhesive, the activation temperature needs to be increased. Although the bonding effect is good from the appearance, the temperature resistance has significantly decreased. If the adhesive is sprayed again, adhesive marks will appear on the surface of the PVC film.
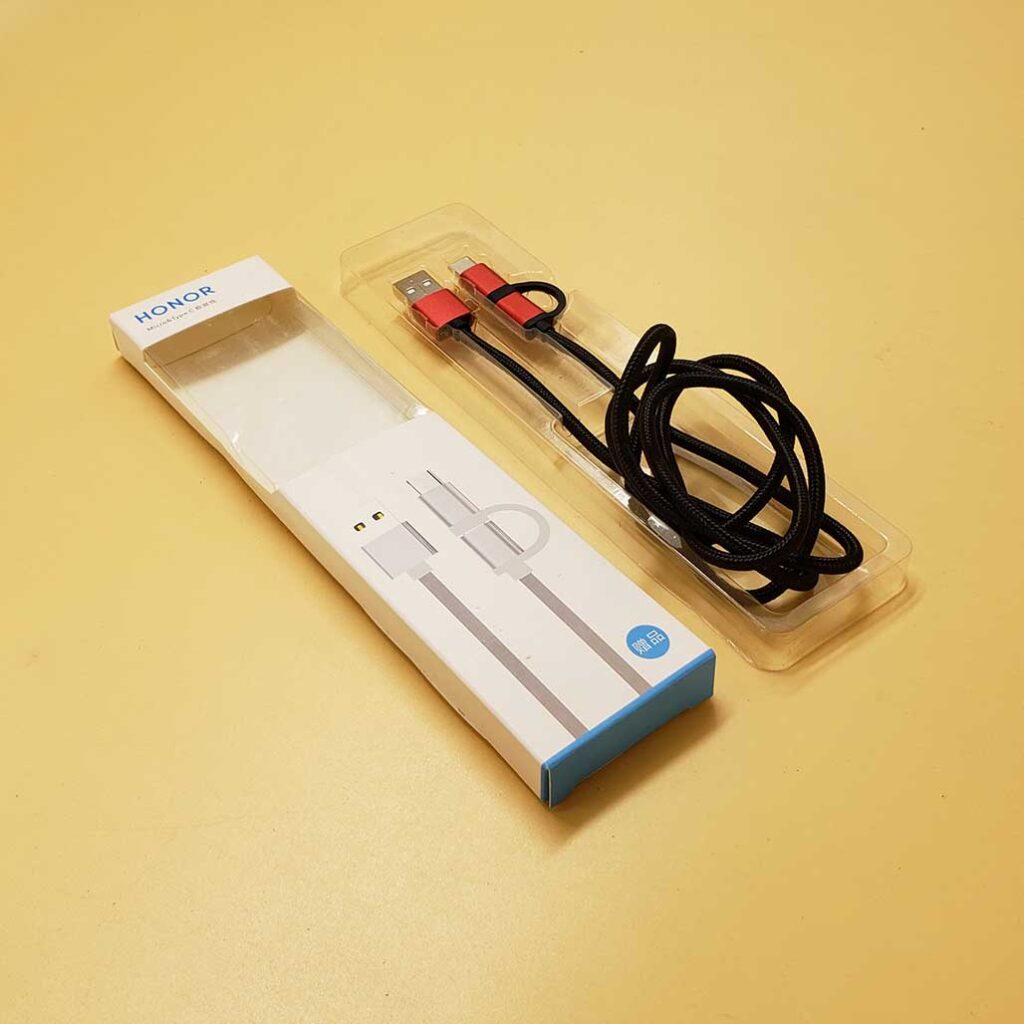
2.2.3 After spraying, the surface turns white and dry, and does not stick to the hands or has obvious adhesive film gloss after drying. The drying time is 30-50 minutes (depending on the temperature, humidity, and spraying quality of the environment).

2.2.4 The commonly used fan should be aligned 1.5-2.0 meters away from the workpiece to blow away humid air, in order to avoid PVC bubbles caused by high humidity in the workpiece.
In winter, in order to increase the temperature of the workpiece, a small insulation room can be used to heat the workpiece to 20-25 ℃ (temperature exceeding 35 ℃ is prohibited, otherwise the workpiece will deform). Glue spraying should be carried out on a water curtain machine in an environment not lower than 16 ℃.

2.2.6 Glue spraying operators should wear masks to protect their physical health.

2.3 Use of silicone film in vacuum molding machines
Select different thicknesses of silicone film based on the characteristics of the workpiece line shape, such as arc value, edges, width and depth of the line shape, etc.
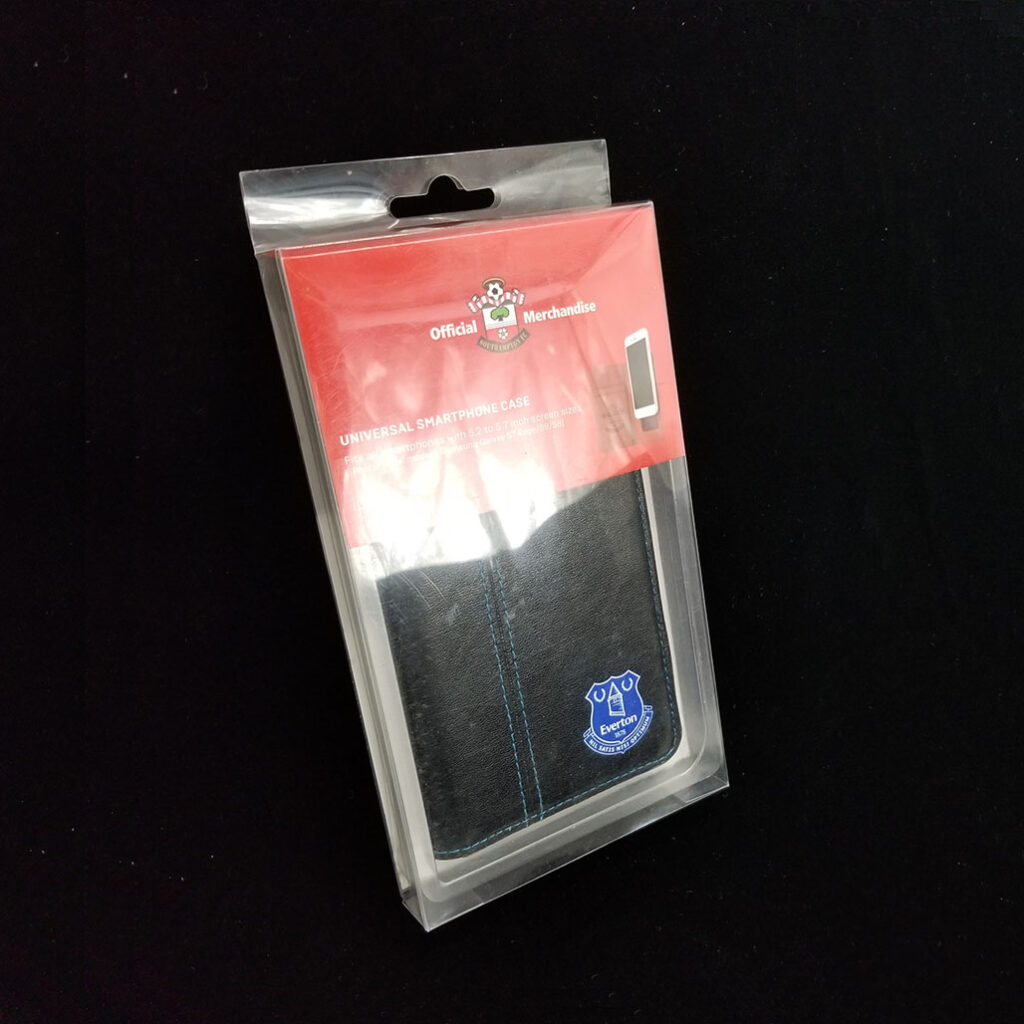
Due to frequent heating and stretching, the sagging of silicone film will increase. It should be installed in a timely manner according to the degree of sagging of silicone film to reduce sagging.

In order to extend the service life of the silicone film and prevent quality issues with the workpiece, the direction of use of the silicone film should be regularly changed, such as changing from the front end to the back end and from the left end to the right end.
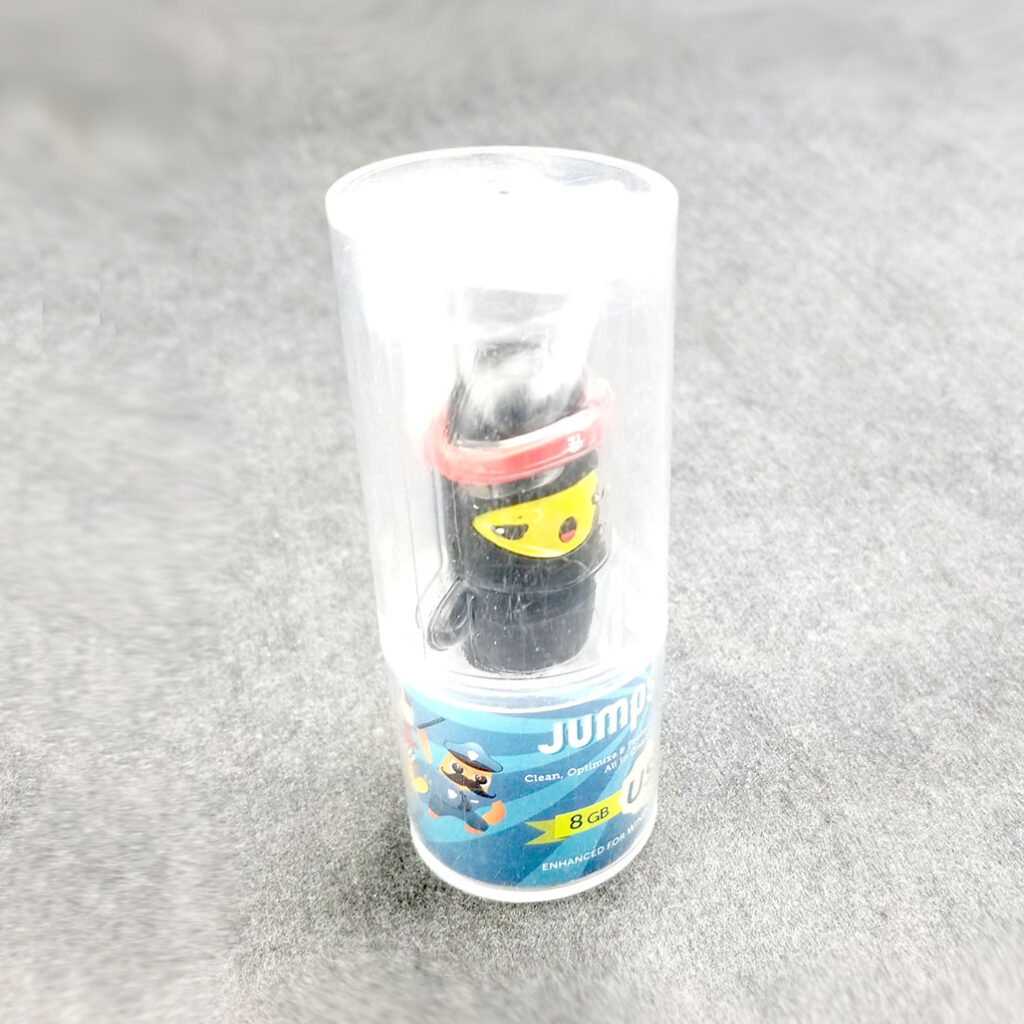
If there are holes or short cracks at the corners of the silicone film, it can be repaired using silicone and a film repair machine. When repairing, compact the top with a flat heavy object. After drying for 24 hours, use 240 # sandpaper to level the repaired area and it can be used normally.

2.4 Setting of process parameters
2.4.1 Distance between membrane pressure workpieces: For narrow and long workpieces with a width less than 10cm, the distance between workpieces shall not be less than 8cm; Width greater than 10cm
