Blistering is a plastic processing technology that mainly involves heating flat plastic hard sheets to become soft, using vacuum adsorption on the surface of the mold, cooling them, and forming them. It is widely used in industries such as plastic packaging, lighting, advertising, and decoration.
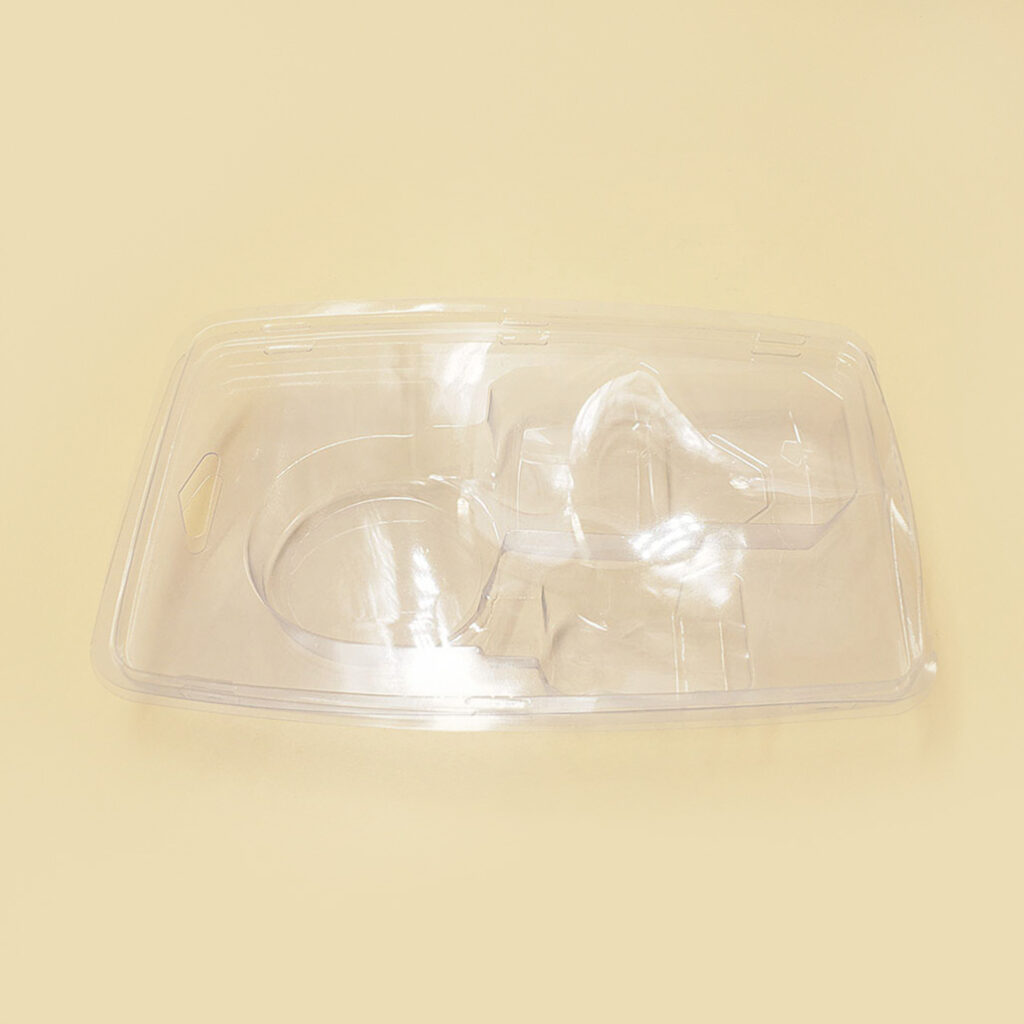
Blister packaging: a general term for plastic products produced using the vacuum molding process and packaged with corresponding equipment. Blister packaging products include: blister shells, pallets, blister shells, etc.
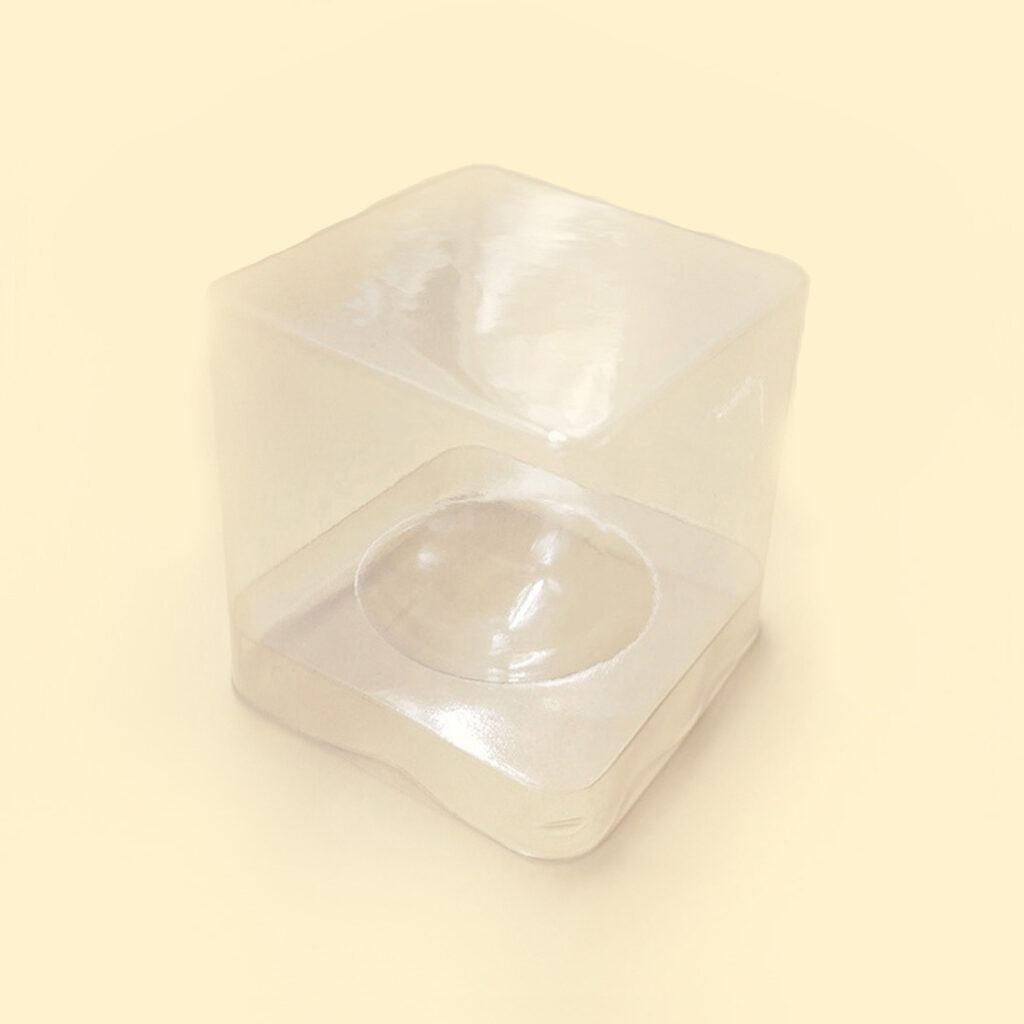
Step 1: Receiving orders and preparing materials. Understand customer needs and take on orders. After the factory receives the order, material preparation is carried out according to customer needs, with the materials generally being PET and PVC.
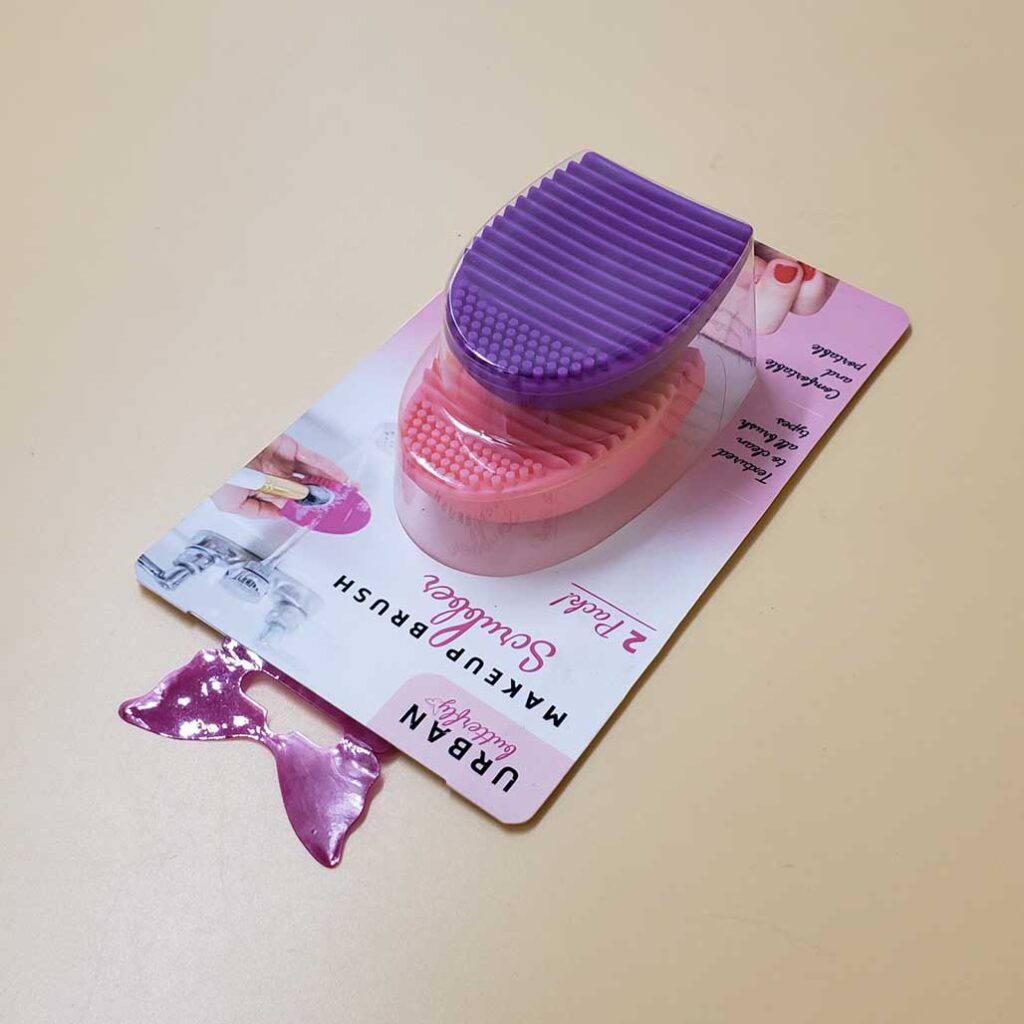
Step 2: Design draft confirmation. Confirm the details of the order with the customer and ask them to provide a design draft or design according to their needs (graphic design).

Step 3: Ink printing. After the design draft is confirmed, the factory will print a floor plan on PET or PVC boards. This process currently includes automatic printing and semi-automatic printing. Only one color can be printed at a time, and the factory I have studied can accept orders for up to seven or eight colors. The more colors there are, the longer the production time and the higher the cost, because each printing of a color requires cleaning the machine equipment and re applying ink, which will result in time and ink loss.
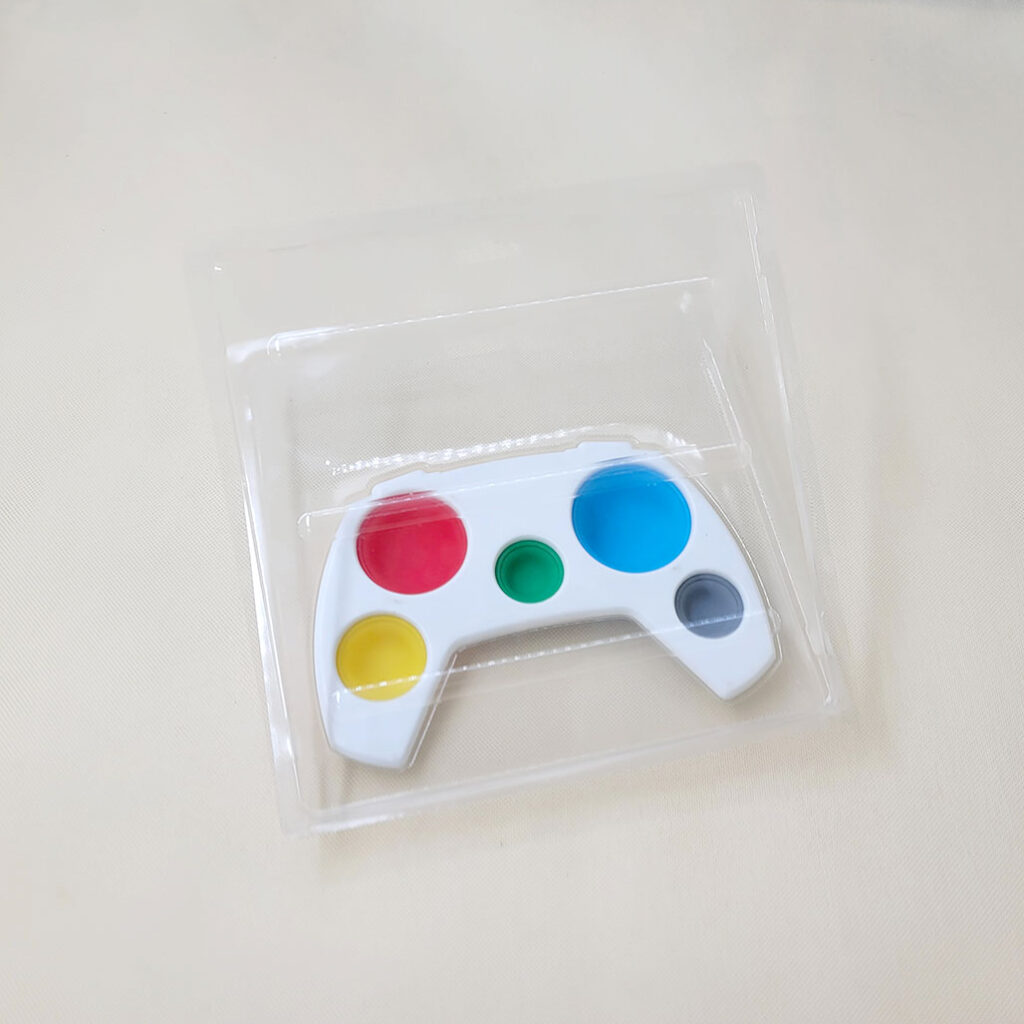