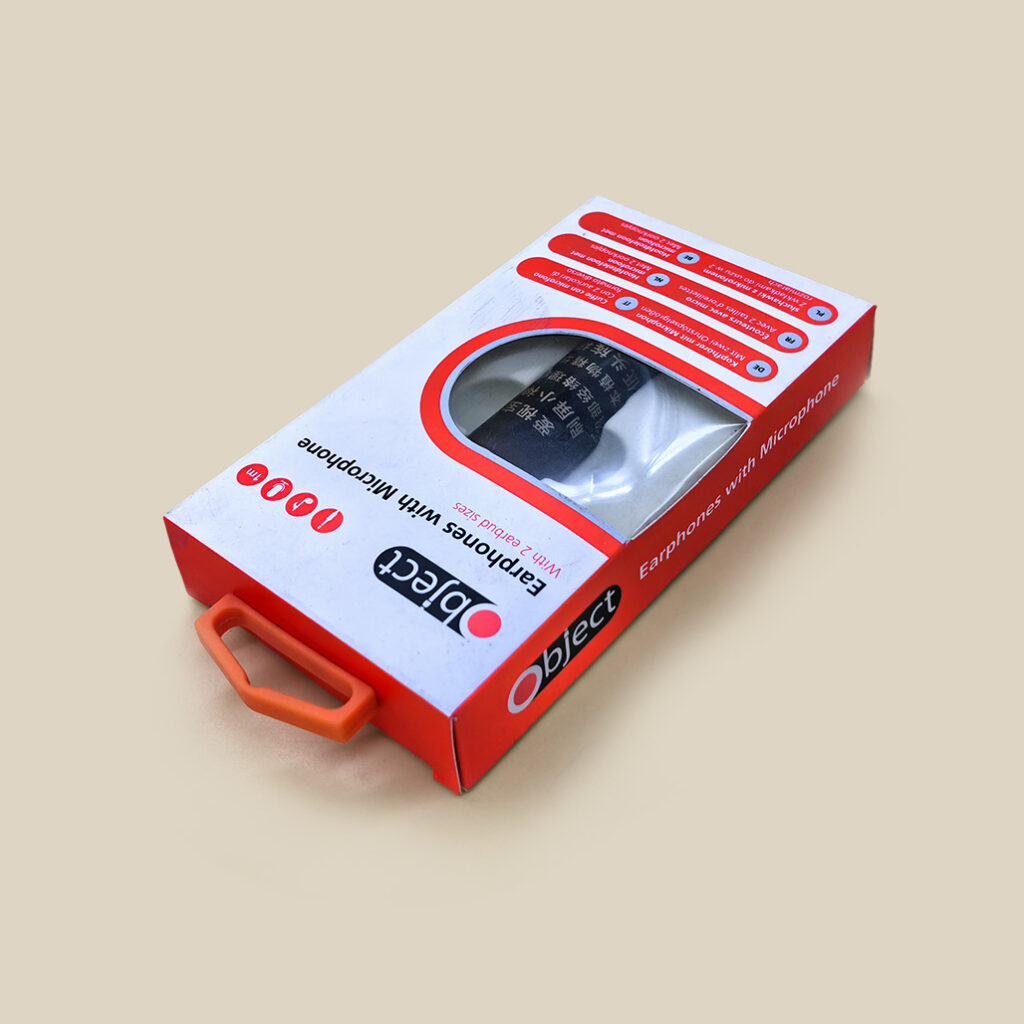
Vacuum forming is a plastic processing technology, which mainly involves heating flat plastic hard sheets to become soft, using vacuum adsorption on the surface of the mold, cooling and forming them. It is widely used in plastic packaging, lighting, advertising, decoration and other industries.
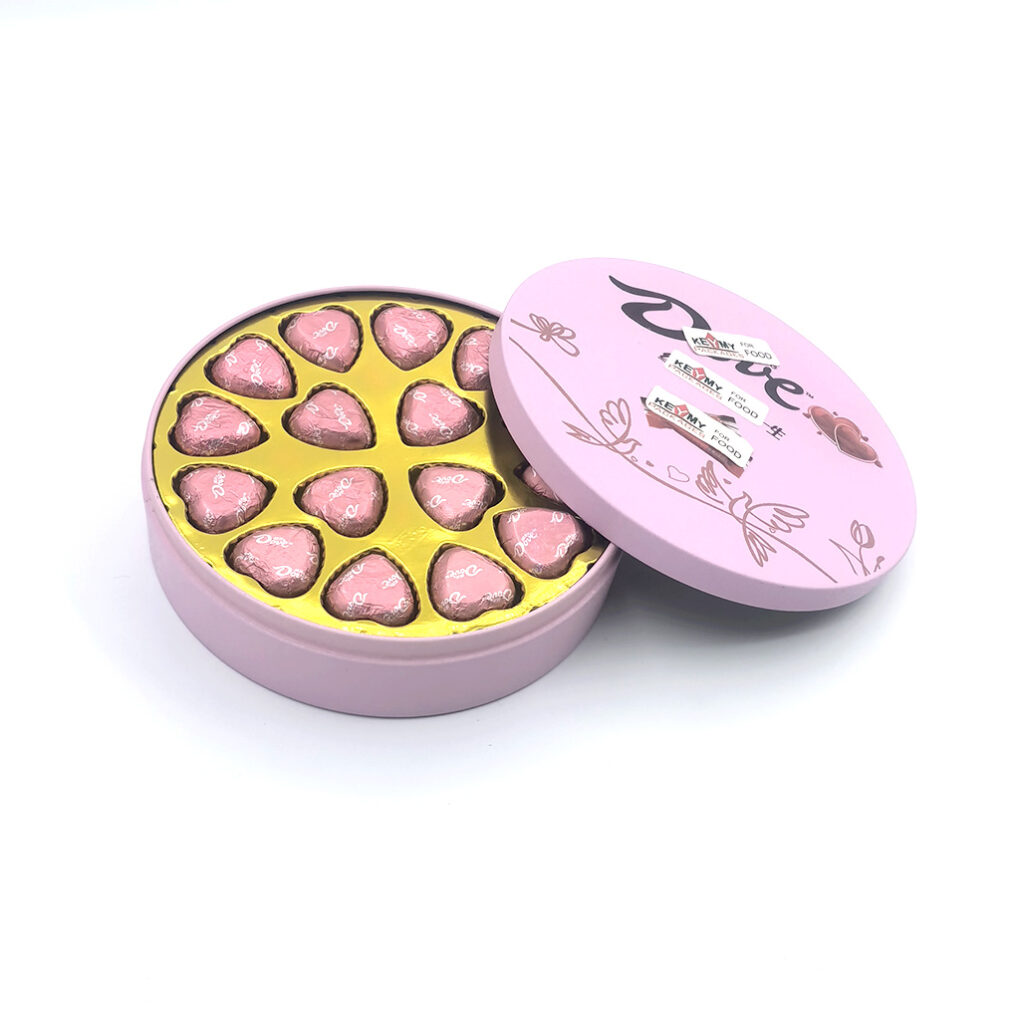
Blister packaging: a general term for plastic products produced using the vacuum molding process and packaged with corresponding equipment.
Blister packaging products include: blister shells, trays, blister boxes, and synonyms include: vacuum covers, blister covers, etc.

The main advantages of vacuum packaging are saving raw materials, light weight, convenient transportation, good sealing performance, and meeting the requirements of environmentally friendly and green packaging; Can package any irregular products without the need for additional cushioning materials for packaging; The packaged products are transparent and visible, have a beautiful appearance, are easy to sell, and are suitable for mechanized and automated packaging, which is convenient for modern management, saves manpower, and improves efficiency
The vacuum packaging equipment mainly includes: vacuum molding machine, punching machine, sealing machine, high-frequency machine, and folding machine.
The packaging products formed by packaging can be divided into: card insertion, card suction, double bubble shell, half bubble shell, half fold bubble shell, triple fold bubble shell, etc.
Common raw materials for vacuum boxes:
The main raw materials for vacuum boxes include PVC, PS, PP, PET, PETG, as well as materials such as flocking, anti-static, and conductive.
Specific production process:
1: Mold making and processing.
2: After the mold is completely dried, perform softening treatment.
3: Place the softened plastic sheets together with the wooden cabinet in a vacuum chamber, activate the suction switch to clean the air inside the vacuum chamber, and wait for the plastic sheets to cool down to obtain the same concave packaging or process mold as the mold.
4: Bubble shell: Using vacuum molding technology to make transparent plastic hard sheets into specific convex shaped transparent plastic, covering the surface of the product to protect and beautify the product. Also known as bubble hood or vacuum hood
5: Tray: also known as plastic inner tray, uses vacuum molding technology to make plastic hard sheets into specific grooves of plastic, and places the product in the grooves to protect and beautify the product.
6: Flocking inner tray: It is a type of blister tray made of special materials, which glues a layer of plush material on the surface of ordinary plastic hard sheets to give the tray a plush texture, used to improve the quality of packaging products.
7: Anti static tray: It is a vacuum tray made of special materials, with a surface resistance value of less than 10 to the 11th ohm. Mainly used for blister trays in electronic and IT products.
8: Vacuum forming mold: The mold used for vacuum forming production has the lowest cost, which is gypsum mold, followed by electroplated copper mold, and the most expensive is aluminum mold. The mold is coated with small holes, which are used for vacuum adsorption and heating of hard sheets to form vacuum molded products.
9: Vacuum forming: It is commonly known as vacuum forming, which uses a vacuum forming machine to adsorb the heated and softened plastic hard sheets onto the surface of the mold, and after cooling, form a concave convex shaped plastic.
10: Vacuum cutting: After vacuum forming, plastic products are cut into individual pieces using a punching machine to cut large sheets of material into individual products.