Vacuum forming, also known as vacuum hot pressing, is based on the principle of pulling rolled sheets into an electric furnace oven and heating them to a softened state. Then, while they are hot, they are pulled up to the top of the vacuum forming mold. The mold is moved up and vacuumed, and the softened sheets are adsorbed onto the surface of the mold. After cooling and forming, they are allowed to harden. The final formed sheet is automatically pulled to the storage box, and the pneumatic cutter separates the formed and unformed sheets, thus completing the entire process.
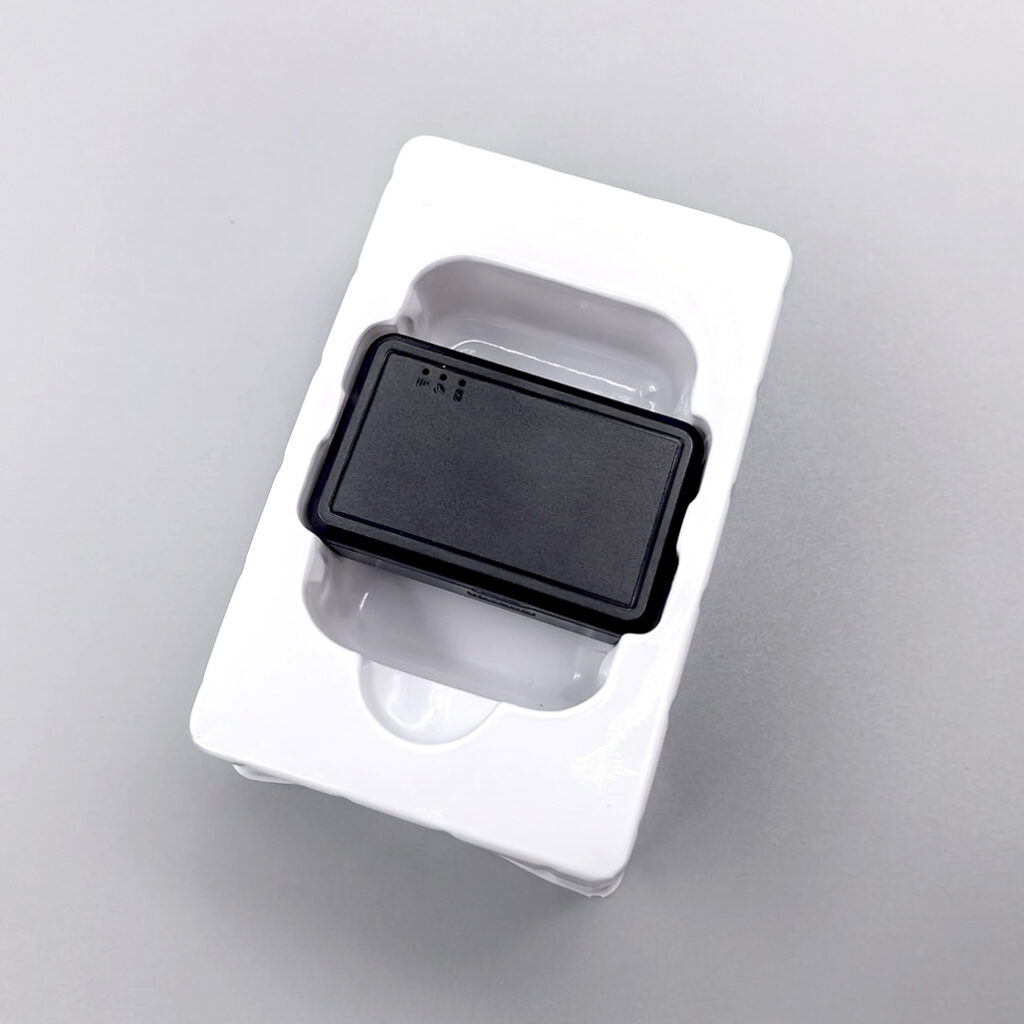
In addition to raw materials, the molding mold is a very important part of the entire vacuum forming process. The selected mold material and mold opening method vary depending on the product.
picture

1、 Vacuum forming of concave molds
The sheet is fixed around and sealed above the mold cavity, heated to soften, and then the air in the mold cavity is extracted to form a vacuum, allowing the sheet to tightly adhere to the mold cavity under high pressure and form. After cooling and shaping, compressed air is introduced through the lower air hole to make a vacuum box. Vacuum forming of concave molds is suitable for vacuum boxes with small depth. If the product is too high or too deep, the sheet material is prone to excessive stretching, resulting in a thin bottom.

2、 Punch vacuum forming
The sheet is clamped above the mold cavity, heated to soften, and the material is covered on the convex mold like a tent, which is cooled and loses its thinning ability. The edges and edges of the sheet are tightly attached to the convex mold to reduce thickness and form. Punch vacuum forming is commonly used for products with high hardness requirements at the bottom of vacuum boxes, and the dimensional accuracy of the inner surface after forming is relatively high.
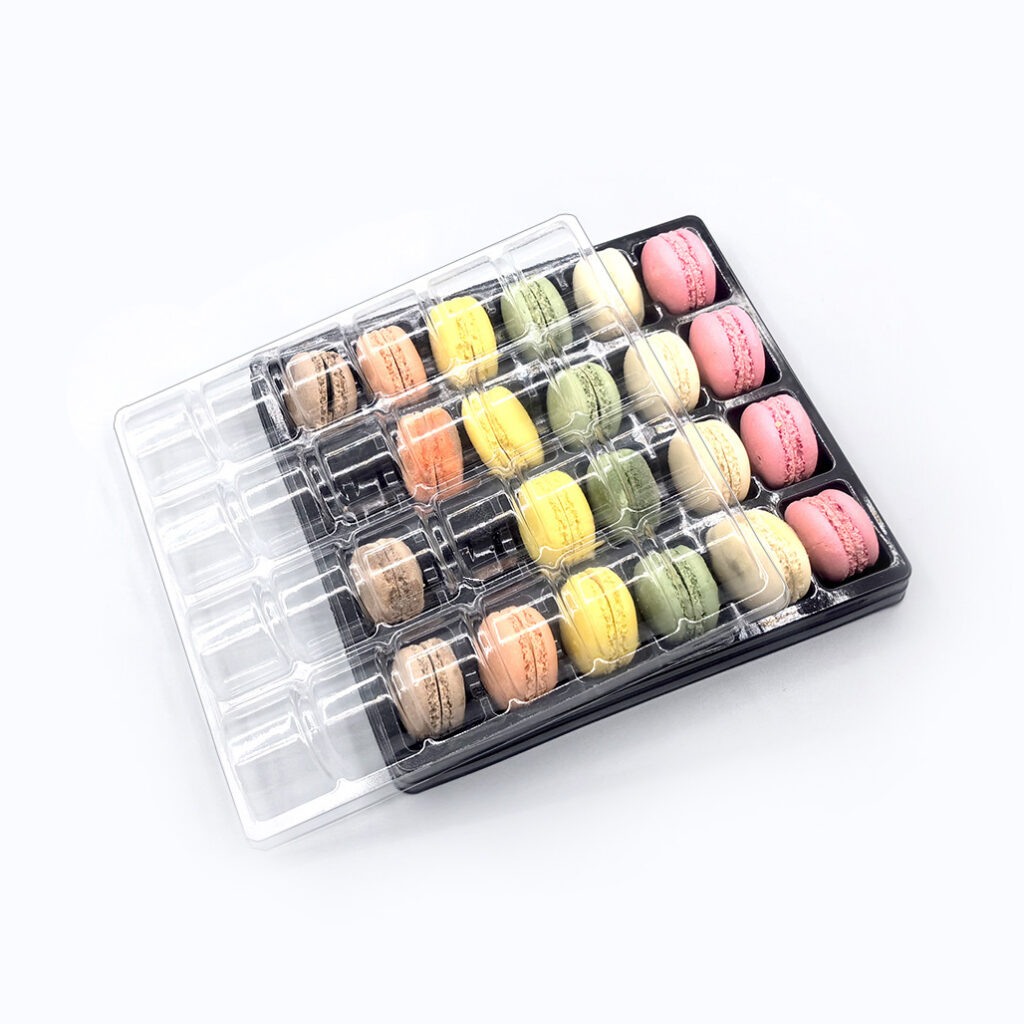