Vacuum forming process is a hot forming processing method. A method of manufacturing open shell products using thermoplastic sheets. Cut the plastic sheet into a certain size and heat it to soften.
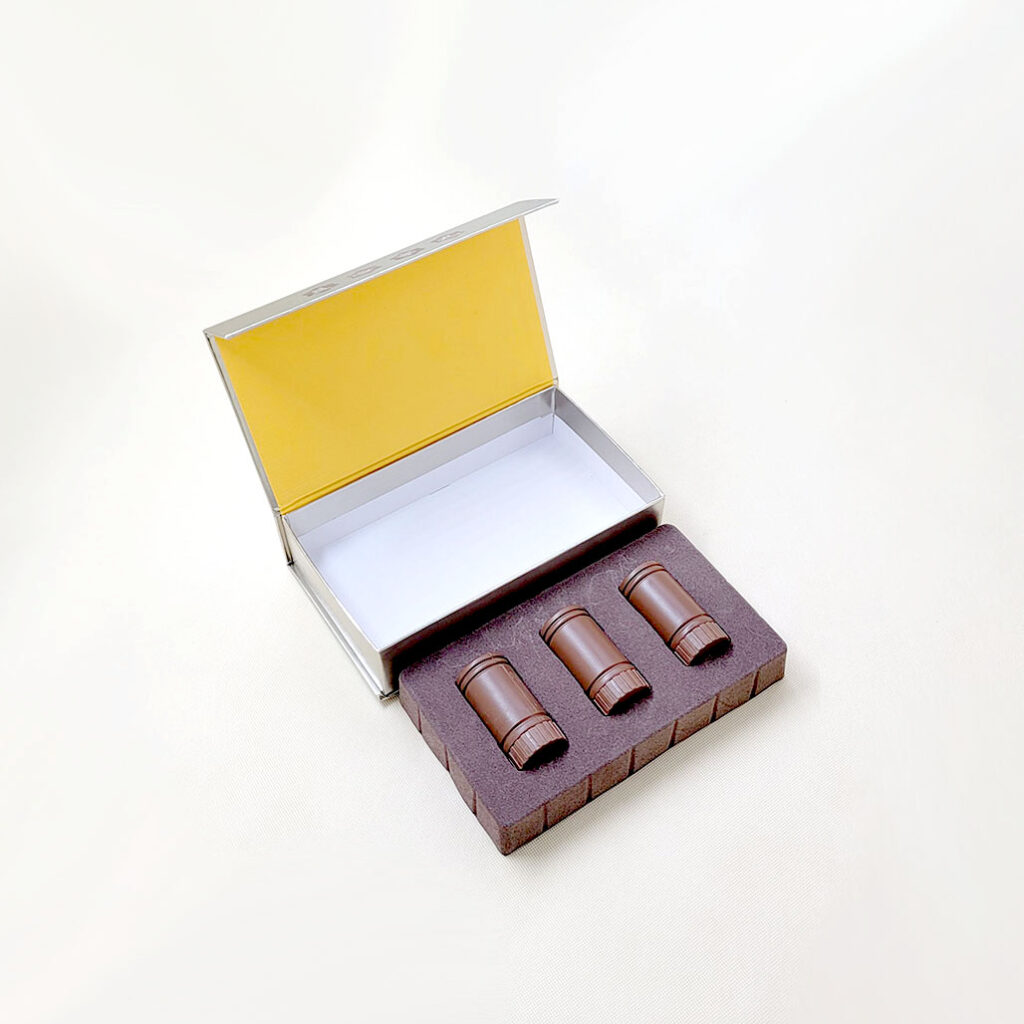
With the help of the pressure difference or mechanical pressure on both sides of the sheet, deform it and cover it on a specific mold contour surface. After cooling and shaping, trim the edges. Vacuum forming is a forming method that relies on vacuum force to cause the sheet to stretch and deform.
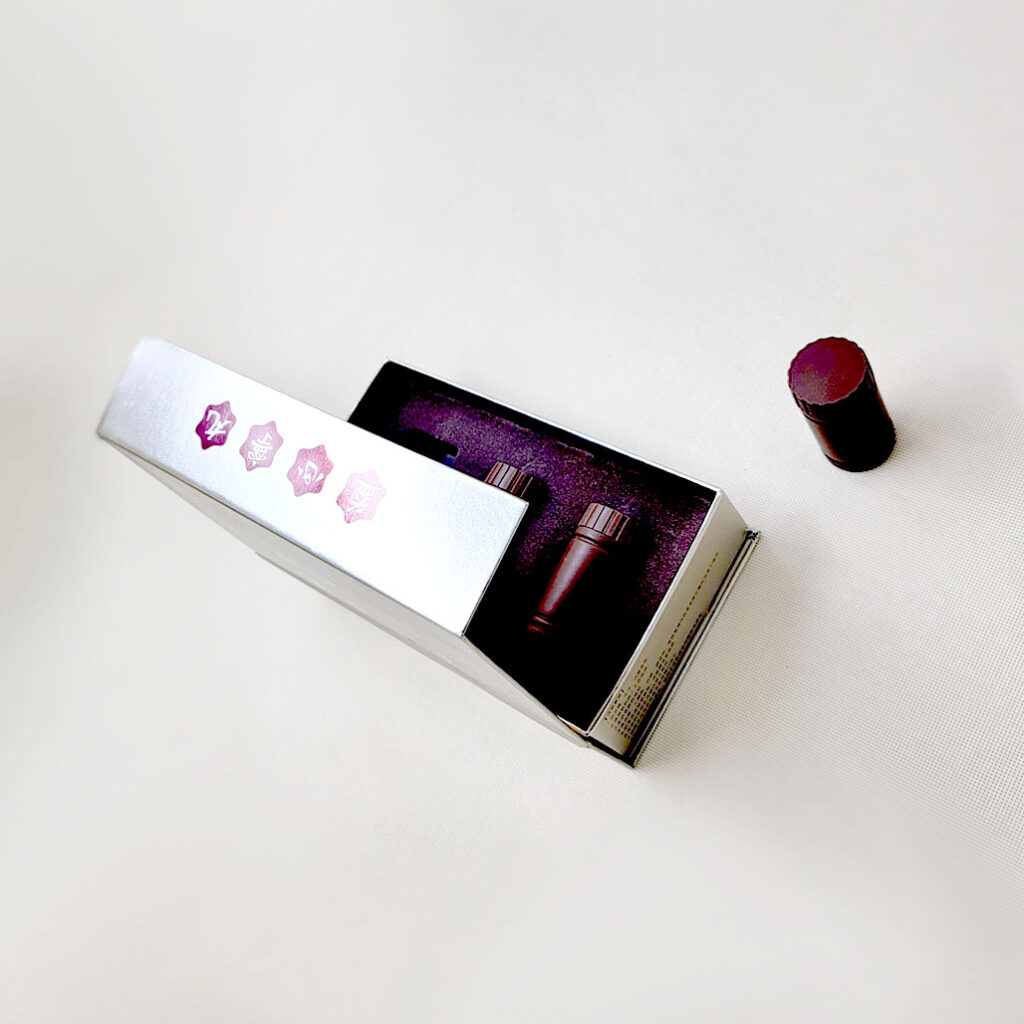
Vacuum force is easy to achieve, master, and control, so simple vacuum forming is the earliest and currently the most widely used hot forming method.
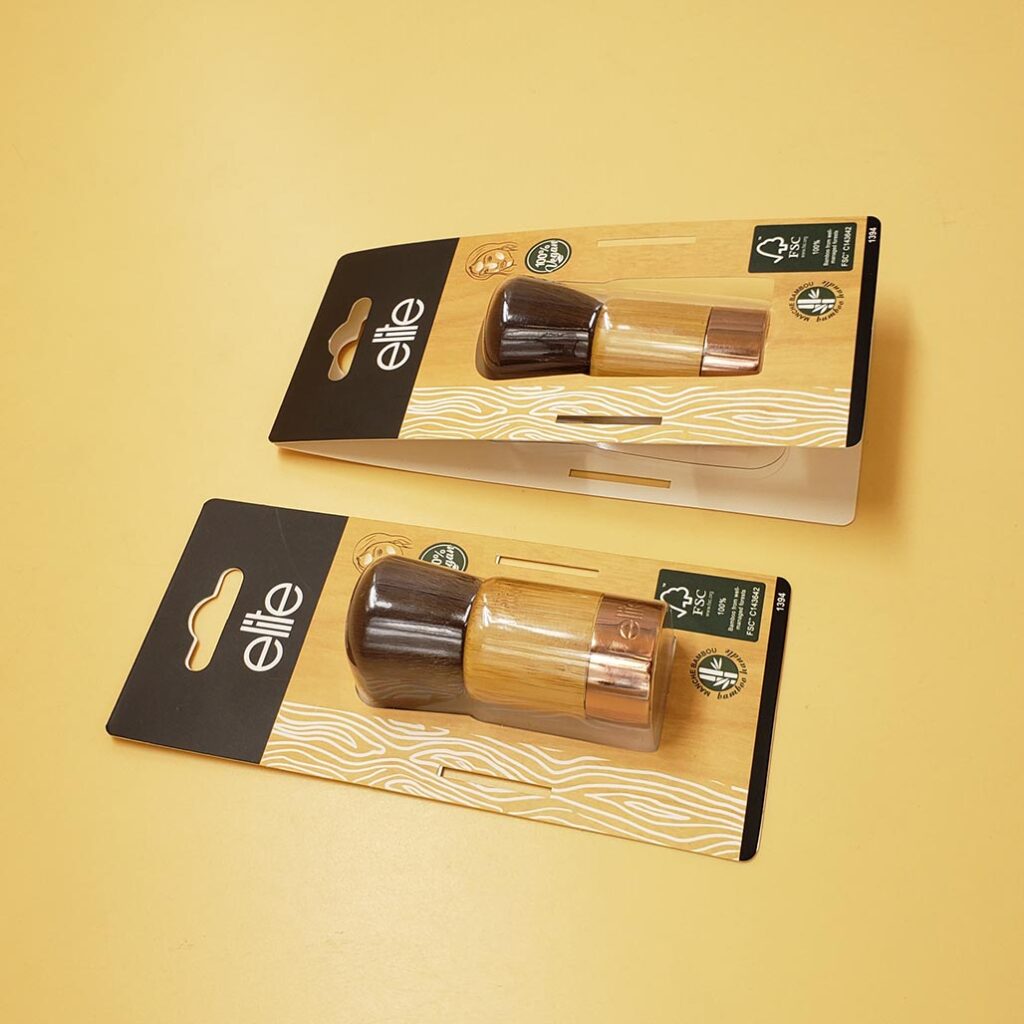
Common sheet materials
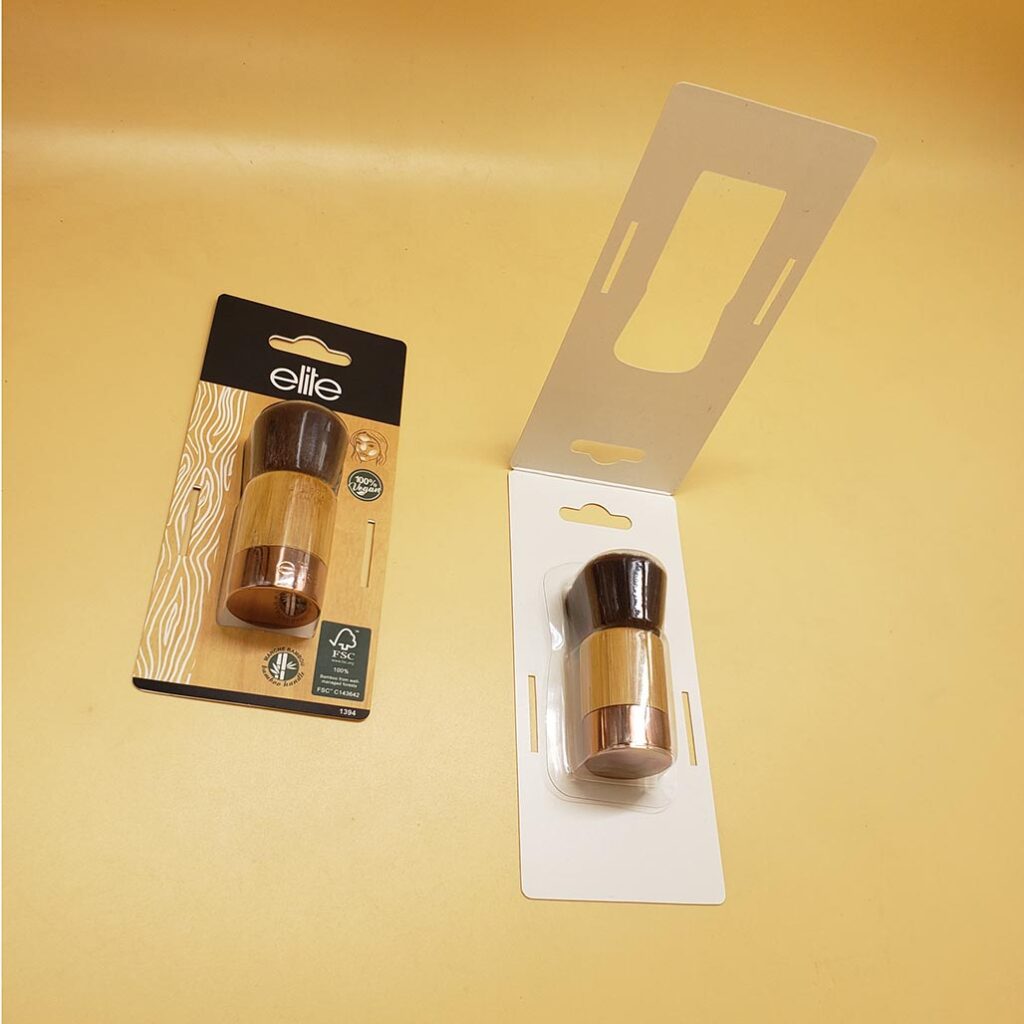
PVC: The most commonly used vacuum plastic material, with soft texture, strong toughness, and good plasticity, can be made into transparent and various colors. Transparent PVC is commonly used to package products such as electronics, cosmetics, toys, and gifts.
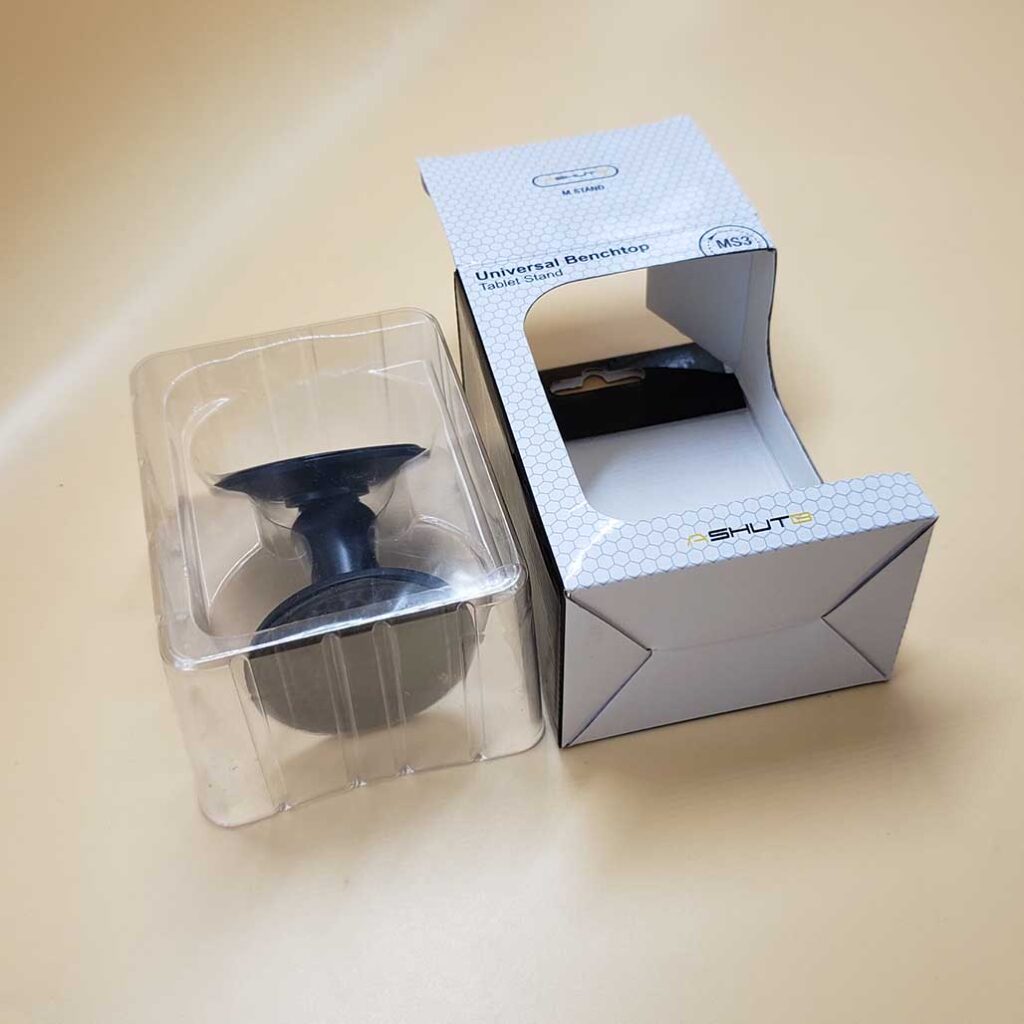
PET (A-PET): Hard, tough, high strength, bright surface, environmentally friendly and non-toxic, with transparent and multi colored sheets. The disadvantage is that PET is difficult to heat seal at high frequency and is much more expensive than PVC. This material is often replaced by users who demand high-end and environmentally friendly products.
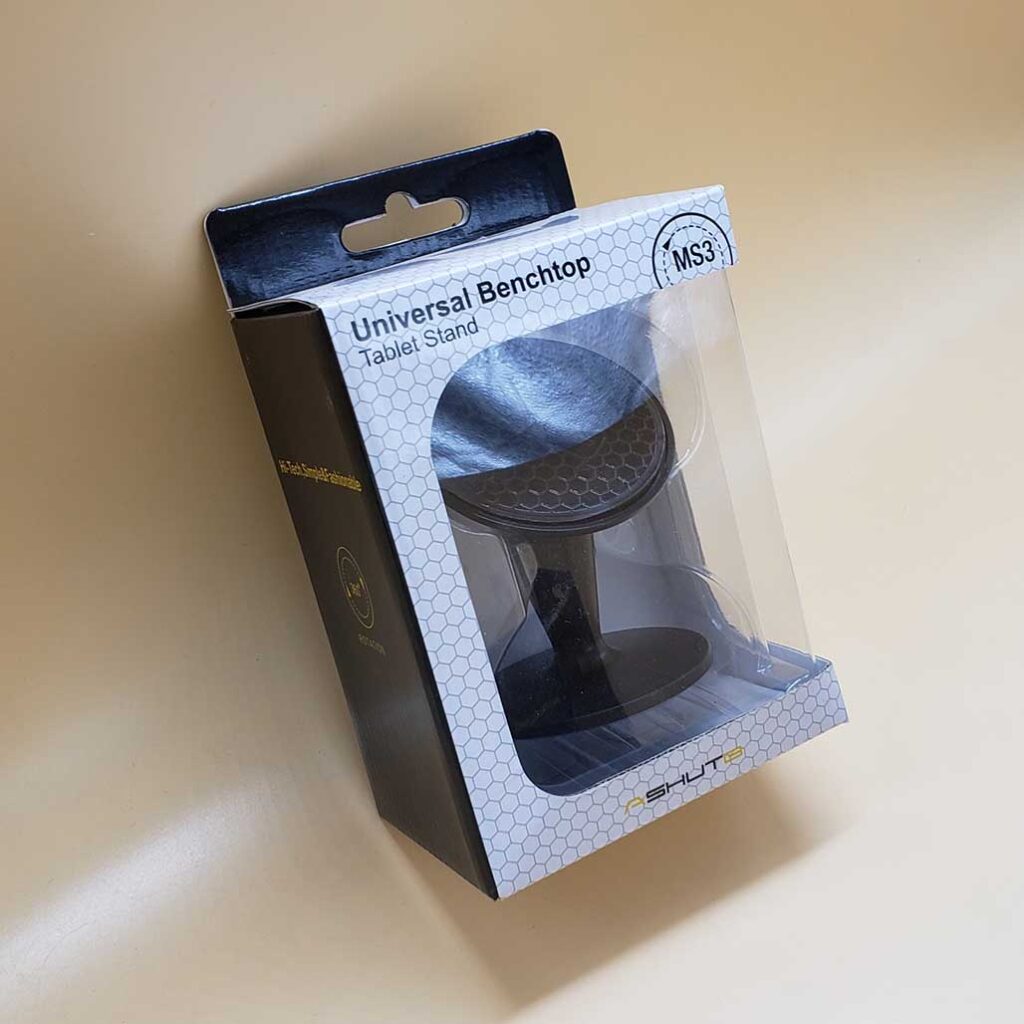
PS: Low density (light weight), environmentally friendly and non-toxic, very good plasticity, poor toughness and easy brittleness, and cannot be made into transparent materials. Therefore, it can only be made into bottom support vacuum plastics, which are prone to cracking and are not suitable for recycling.
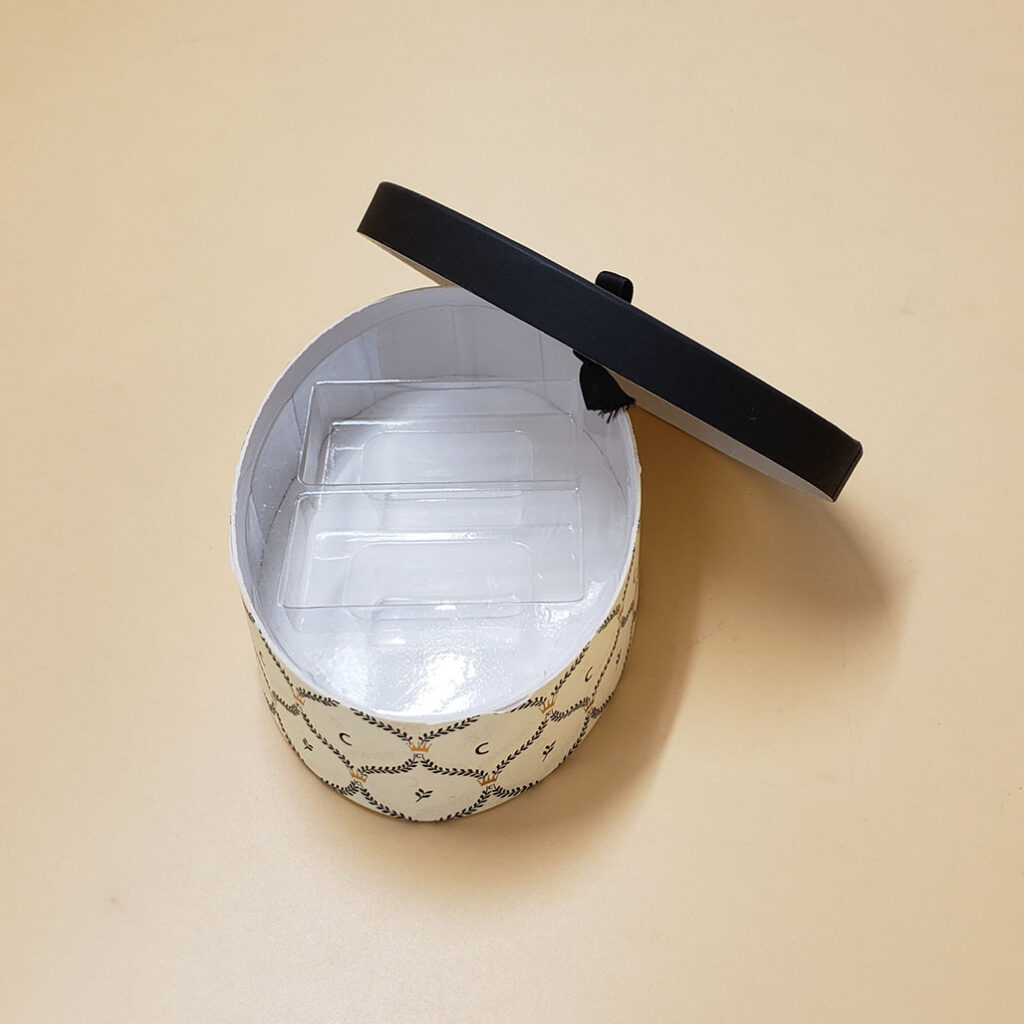
PP: The material is particularly soft, has good toughness, is environmentally friendly, non-toxic, and resistant to high temperatures. It is often used as packaging for dining utensils or other high-temperature products; But its plasticity is poor, processing difficulty is high, surface glossiness is poor, and the color will become lighter during processing.
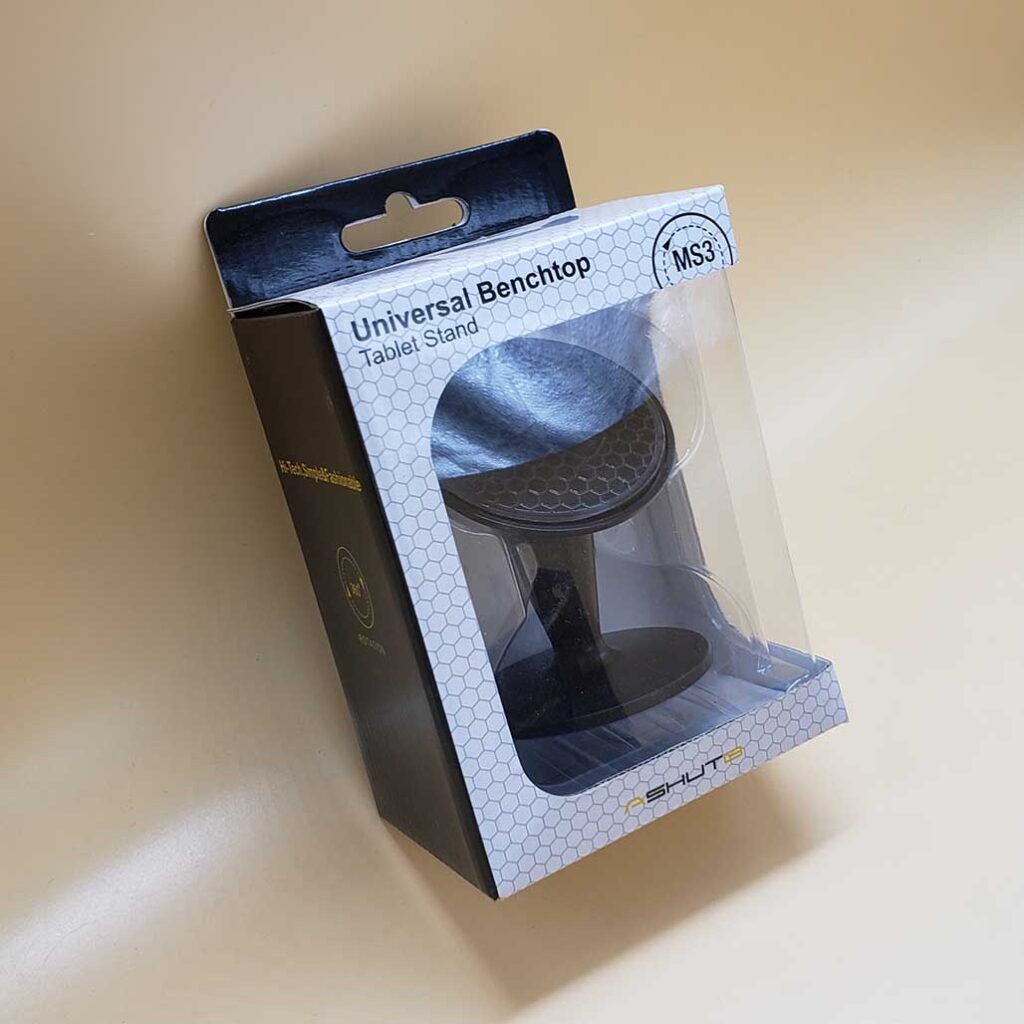
PET-G: Its physical properties are similar to A-PET, but it can be thermally bonded at high frequencies, and its price is 80% more expensive than A-PET
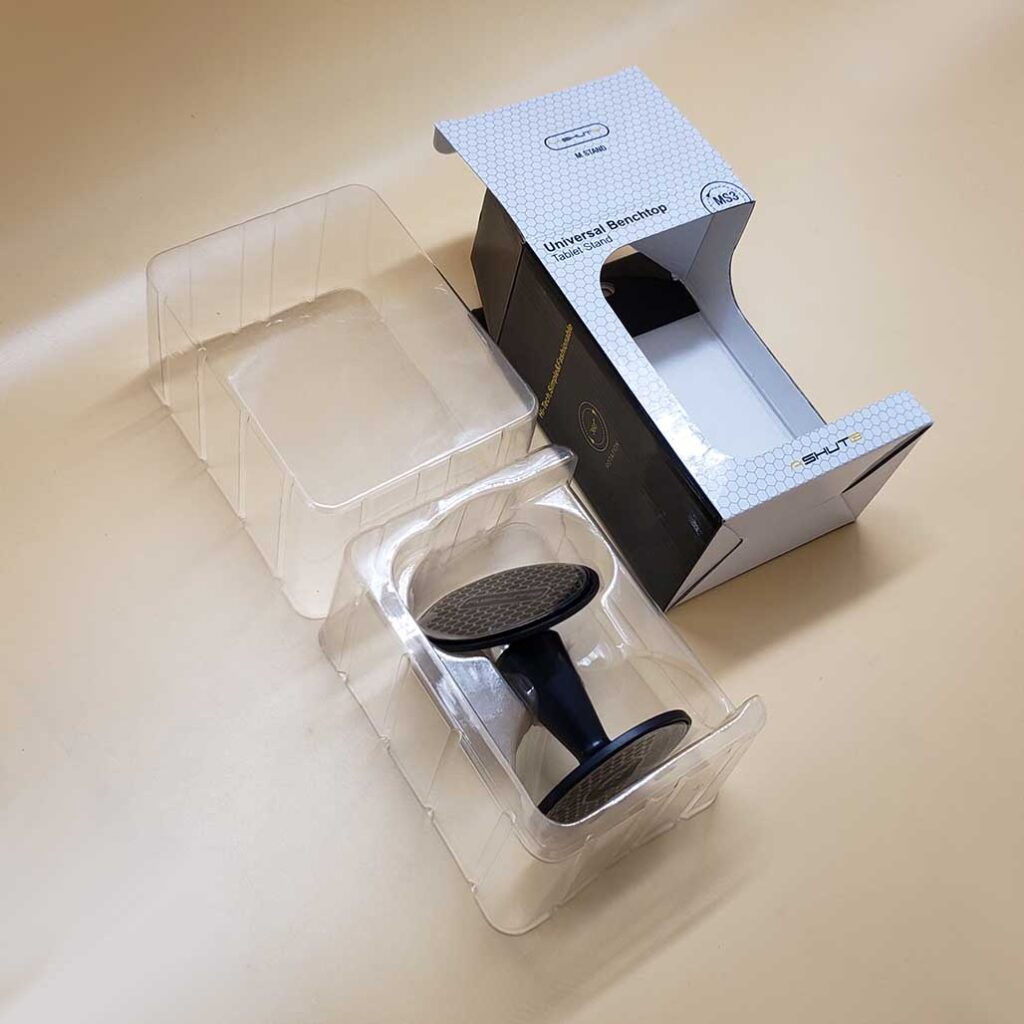