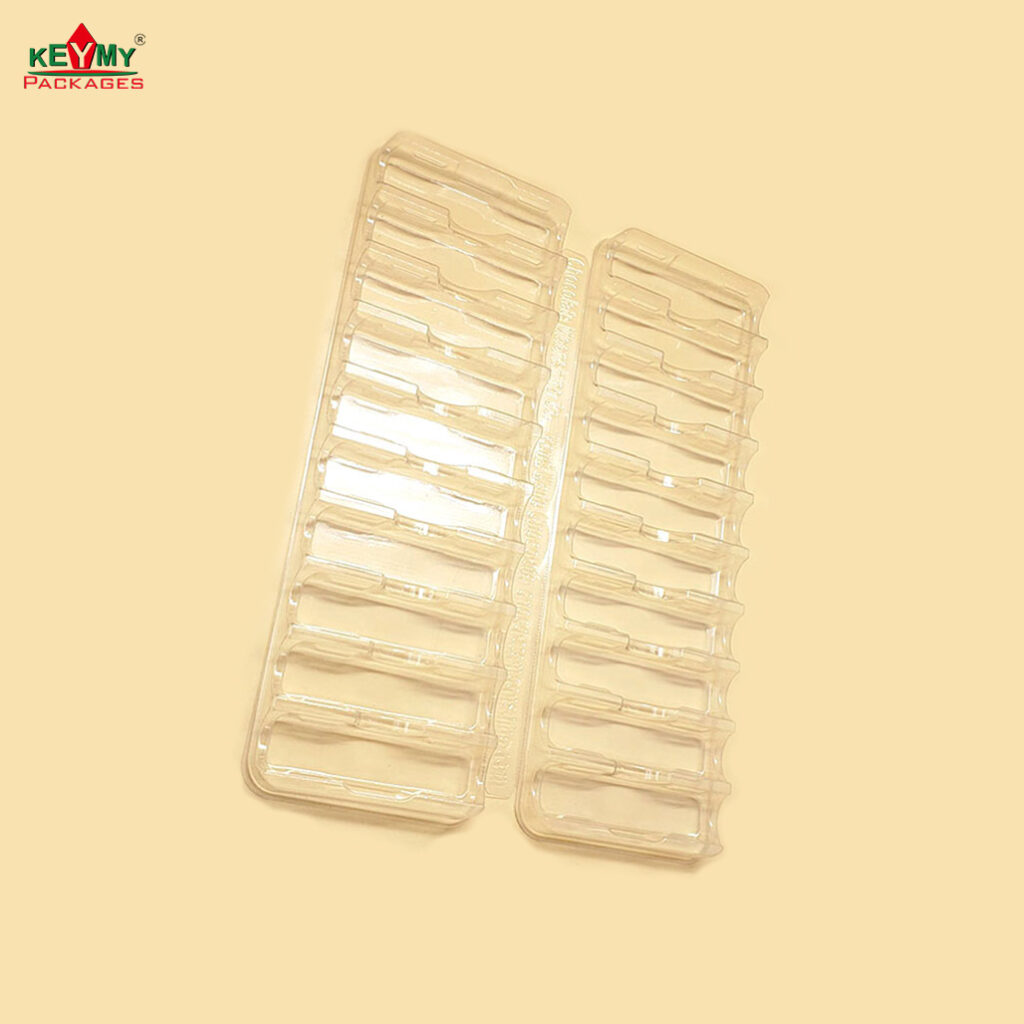
Vacuum molded products are processed using plastic, and the principle of product generation is to heat and soften the flat plastic hard sheet material, then vacuum adsorb it onto the surface of the mold, and then cool it to form. Vacuum molded products are widely used, mainly in industries such as electronics and appliances, food, hardware tools, cosmetics, toys, daily necessities, medicine, health products, automobiles, stationery, cultural and sports products, etc.
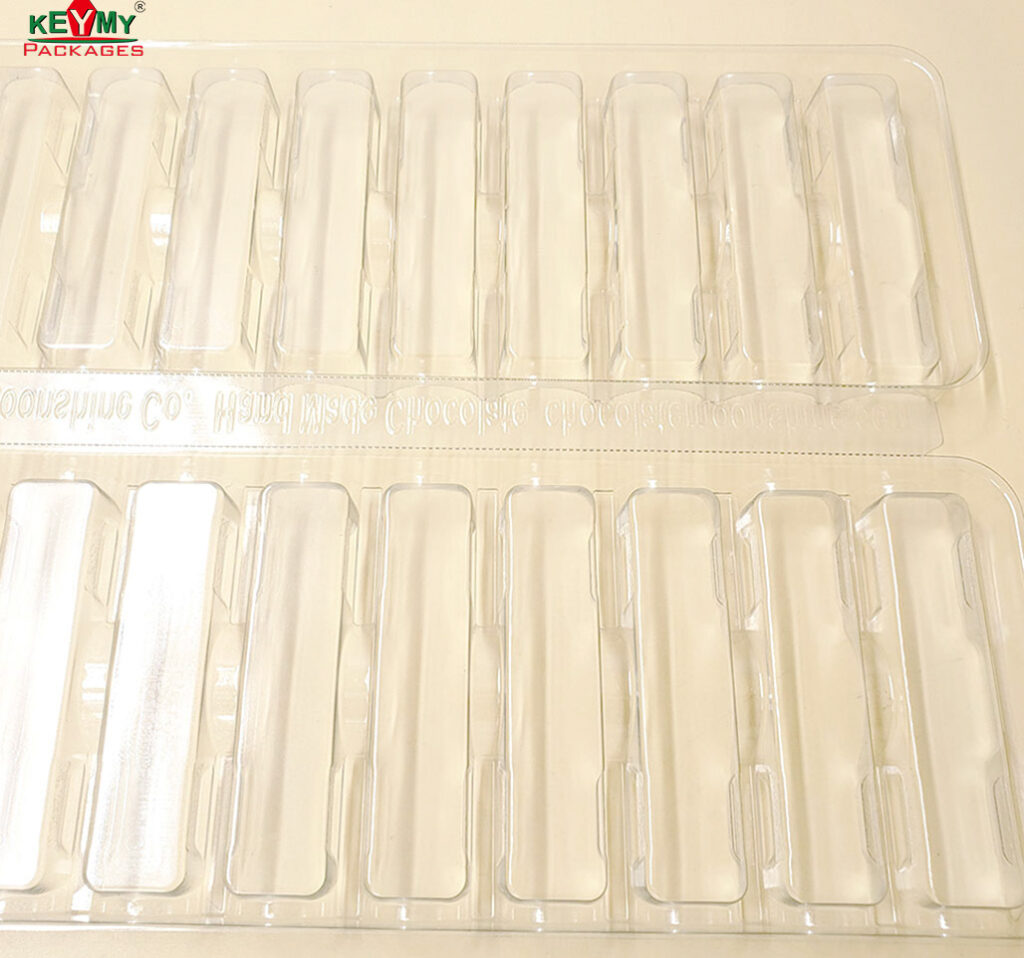
1、 Classification of blister packaging
Blister packaging: a general term for plastic products produced using the vacuum molding process and packaged with corresponding equipment. The packaging products formed by packaging can be divided into: card insertion, card suction, double bubble shell, half bubble shell, half fold bubble shell, triple fold bubble shell, etc. Blister packaging products include: blister shells, trays, blister boxes, and synonyms include: vacuum covers, blister covers, etc.
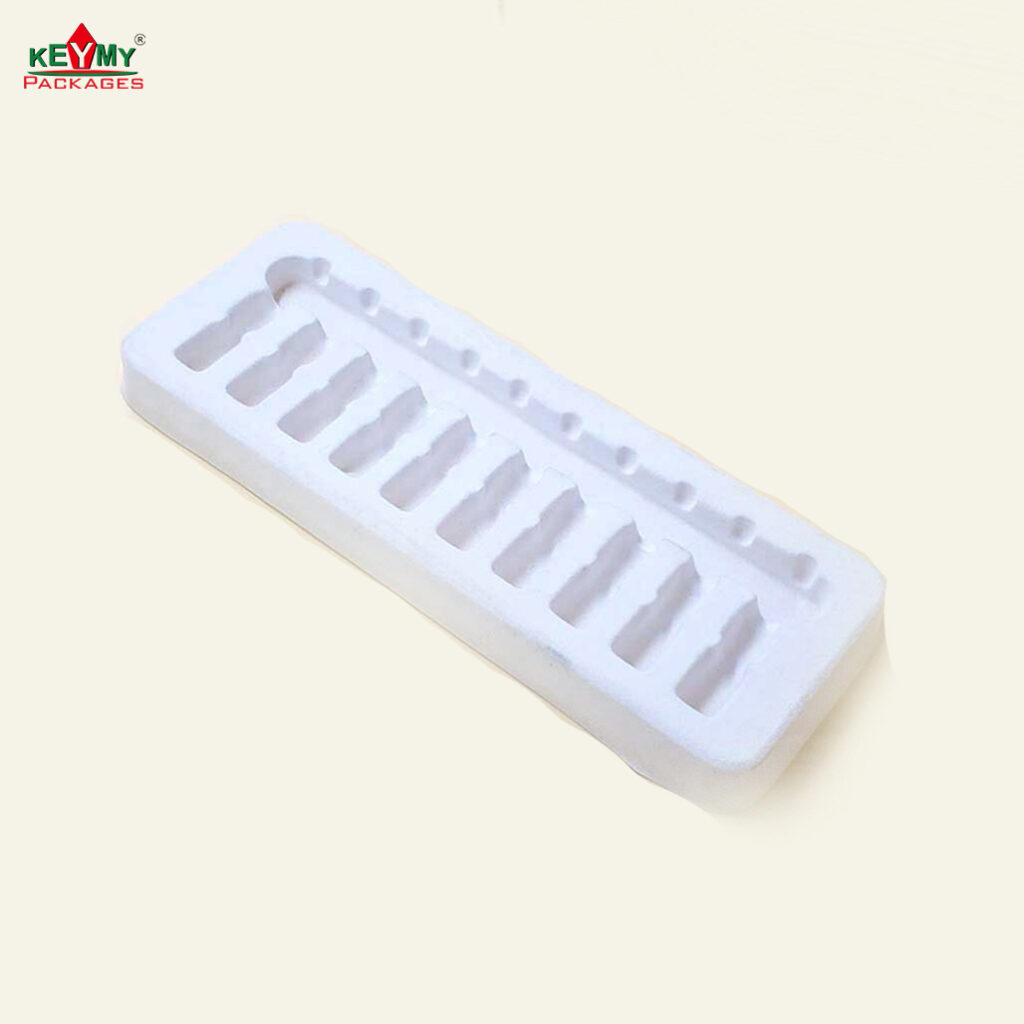
Blister shell
Using vacuum molding technology to make transparent plastic hard sheets into transparent plastic with specific raised shapes, covering the surface of the product to protect and beautify the product. Also known as bubble hood, vacuum hood, or plastic face mask. According to the different forms of bubble shells, they can be divided into single bubble shell, double bubble shell, plug-in bubble shell, and suction bubble shell

Blister box
It is a type of vacuum molded product with a lid and a bottom. The bottom and lid connected together are called folding vacuum molded boxes, while the bottom and lid separated are called bottom cover vacuum molded boxes.

Blister shaped “tray”
Also known as plastic inner support, it uses vacuum molding technology to make plastic hard sheets into specific grooves of plastic, and places the product in the grooves to protect and beautify the product.
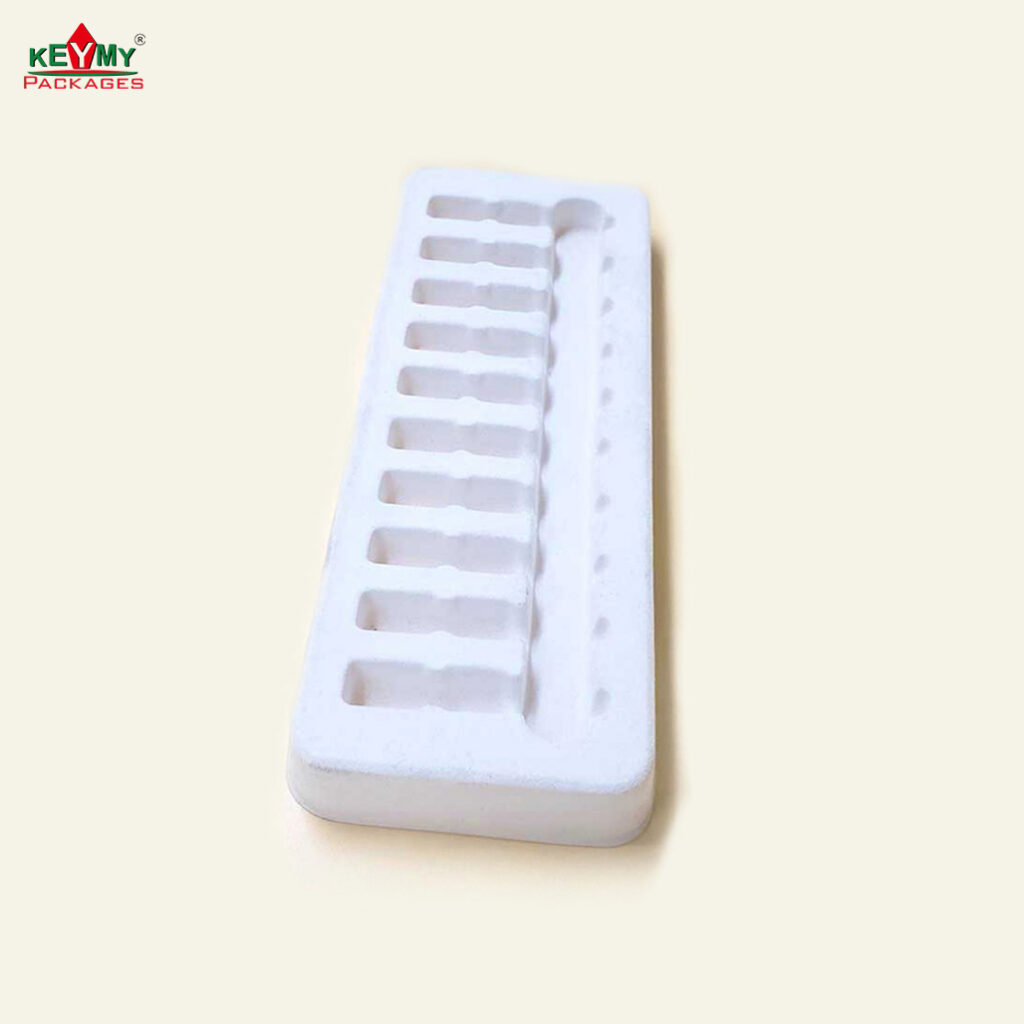
Flocking inner support
It is a type of blister tray made of special materials, which glues a layer of plush material on the surface of ordinary plastic hard sheets, giving the tray a plush texture and improving the quality of packaging products.

Anti static tray
It is a vacuum tray made of special materials, with a surface resistance value of less than 10 to the 11th ohm. Mainly used for blister trays in electronic and IT products.
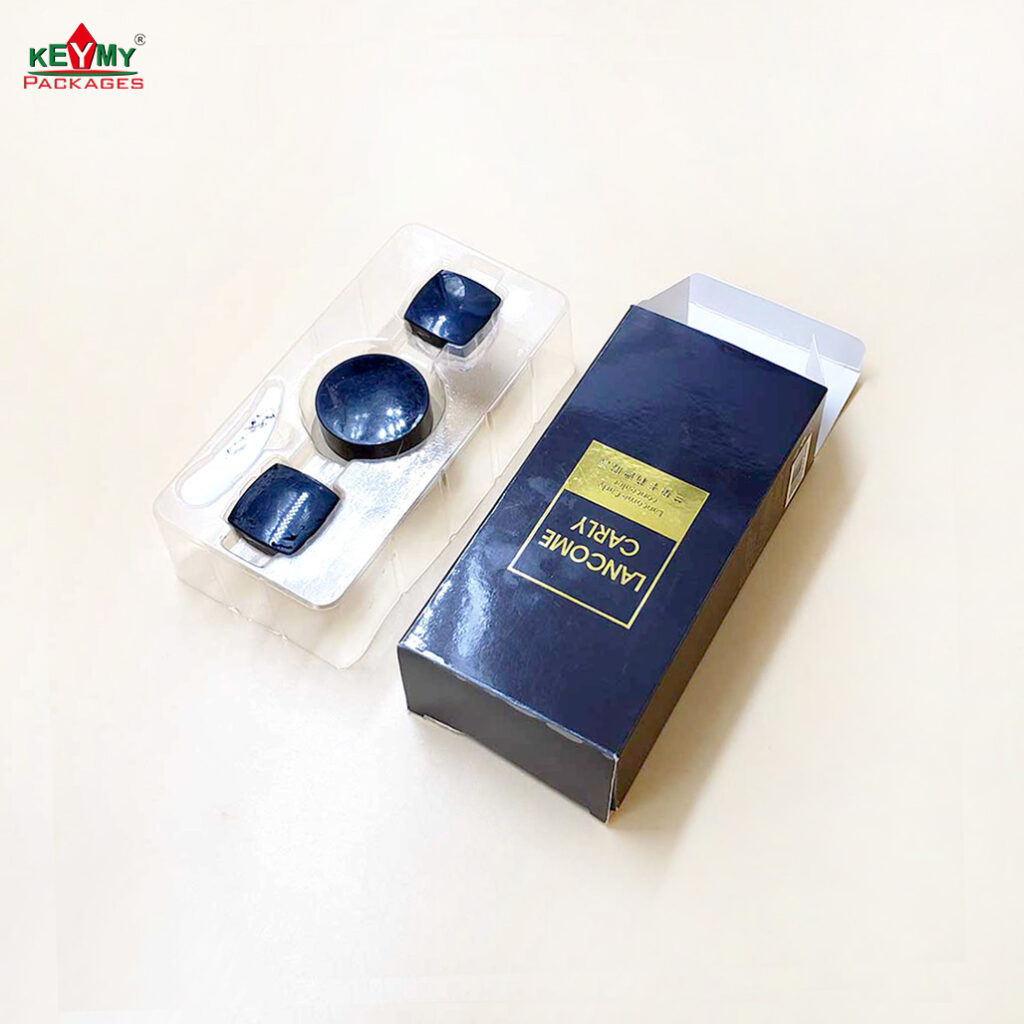
Vacuum molding “mold”
The lowest cost mold used in vacuum forming production is gypsum mold, followed by electroplated copper mold, and the most expensive is aluminum mold. The mold is drilled with small holes for vacuum adsorption and heating of hard sheets to form vacuum molded products.
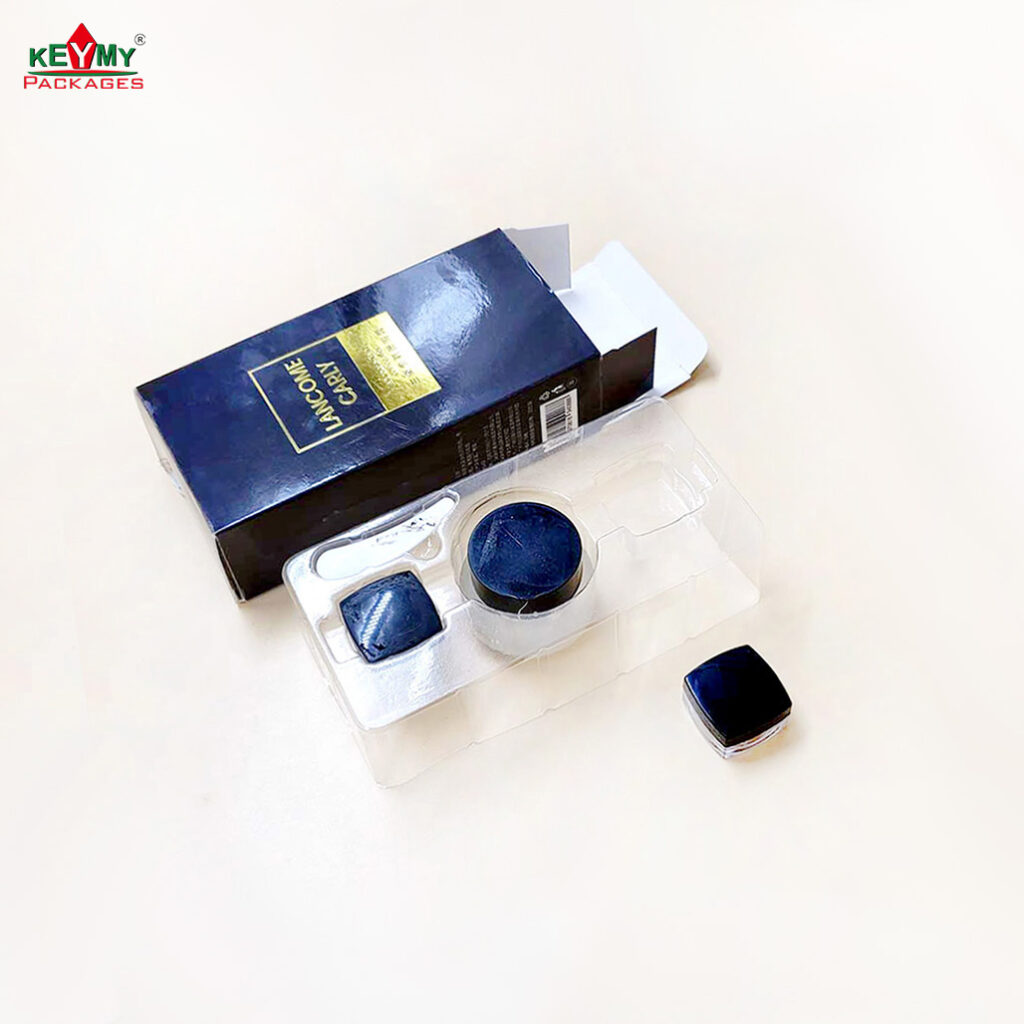