With the development of environmental protection trends, the requirements for plastic packaging have become increasingly strict. In addition to avoiding use, eliminating “excessive packaging”, and reducing waste generation, it is the primary environmental strategy for plastic packaging. As a good environmentally friendly and green packaging, vacuum forming packaging materials are deeply loved by the public. This article shares relevant knowledge about vacuum forming technology, and the content is for reference by friends who purchase high-quality packaging systems:
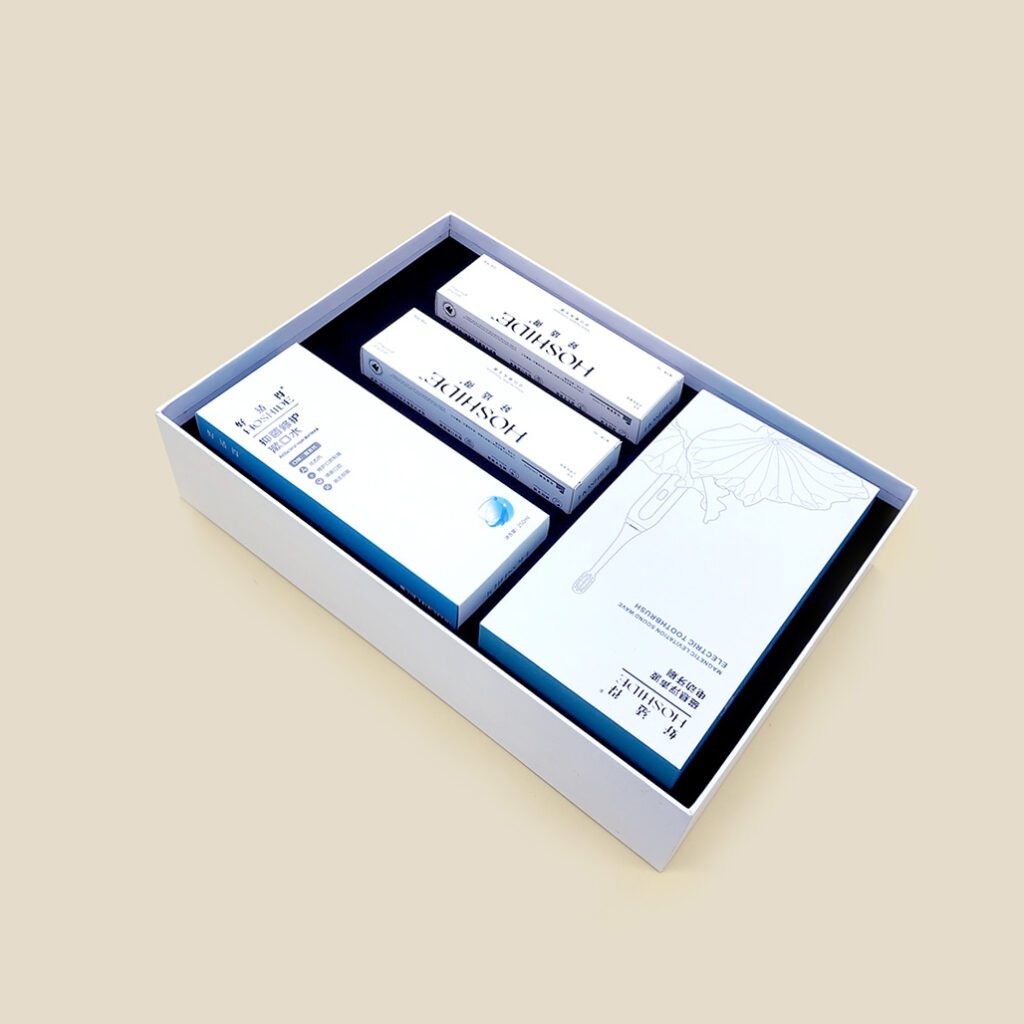
1、 Process Overview
Vacuum thermoforming: The lowest cost and simplest thermoforming process, suitable for materials such as ABS, PET, PP, PC, HIPS, HDPE, PETG, Also known as vacuum molding. Vacuum forming technology is one of the most commonly used forming methods in plastic packaging, which is a forming technology that uses thermoplastic sheets as the forming object. The vacuum molding process was developed in the early 20th century, but its application in industrial production was only after the 1940s, and it only had significant development in the 1960s. Through continuous development and change, the vacuum forming process has achieved high automation and mechanization, and the generation of waste materials is also decreasing.
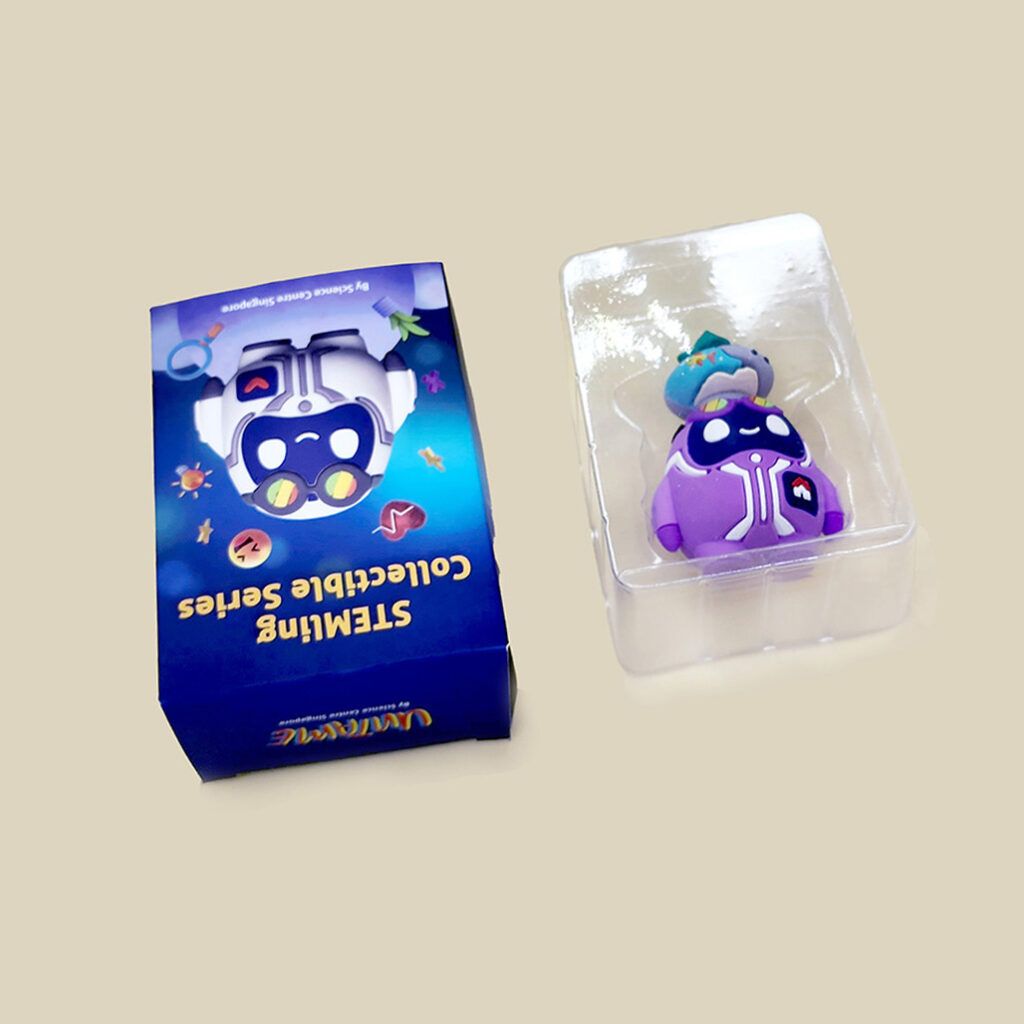
2、 Process principle
A method of manufacturing open plastic shell products using thermoplastic sheets is to cut the plastic sheet into a certain size, heat and soften it, use the pressure difference and mechanical pressure on both sides of the sheet to deform it, apply it to a specific mold contour surface, cool and shape it, and trim the edges to complete the process of vacuum forming products.

3、 Process characteristics
Process cost: processing cost (low medium), single piece cost (low medium)
Environmental protection: Meet the requirements of environmentally friendly and green packaging; Can package any irregular products without the need for additional cushioning materials for packaging
Suitable for mass production and mechanized and automated packaging, facilitating modern management, saving manpower, and improving efficiency.
Quality: determined by actual materials used, pressure, and operating techniques
Speed: On average, 1-8 minutes per cycle
Product features: The packaged product is transparent and visible, has a beautiful appearance, and is easy to sell
Typical products: plastic sheet packaging, disposable plastic lunch boxes, aerospace interiors, etc
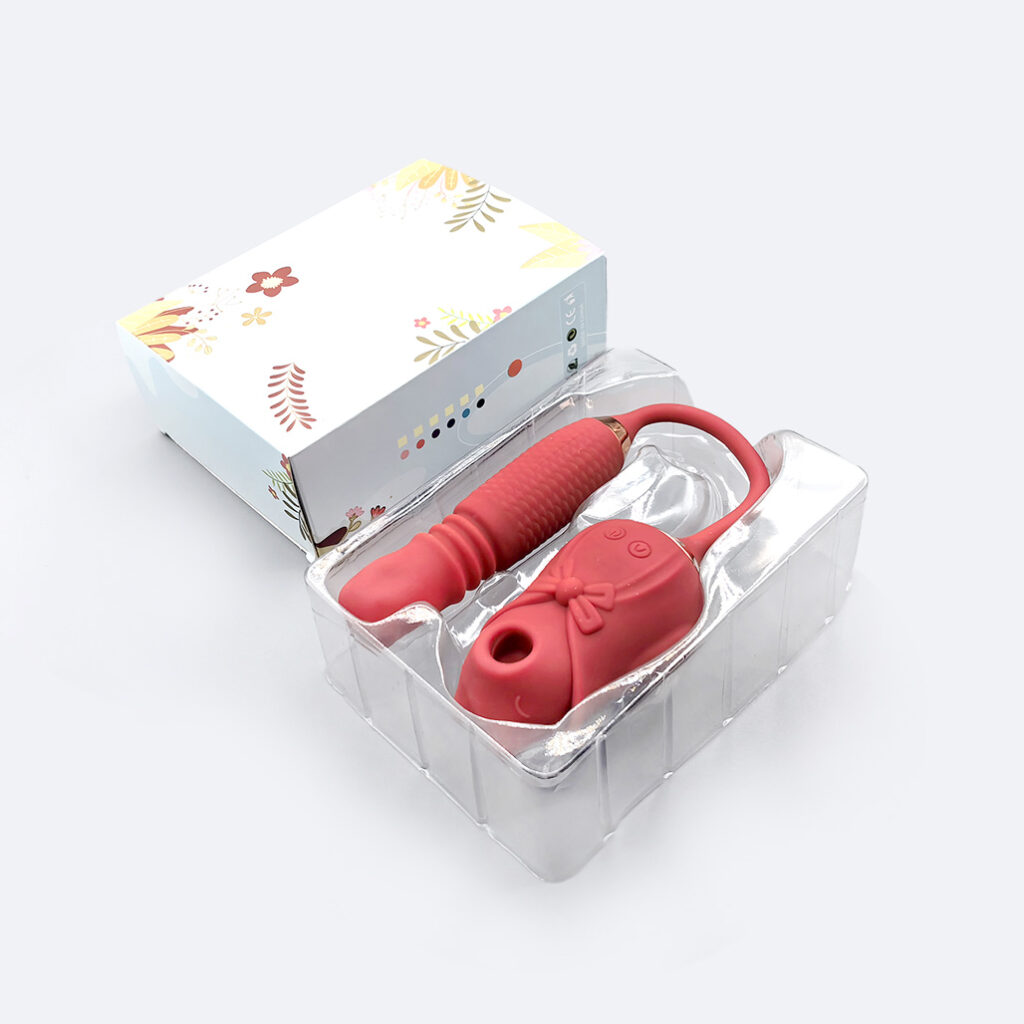
4、 Process equipment
According to the different pressurization methods of vacuum forming, mainstream vacuum forming equipment is mainly divided into the following three categories:
(1) Vacuum negative pressure suction molding machine mainly uses negative pressure suction to make plastic sheets adhere to the mold;
(2) Positive pressure suction molding machine increases the air pressure on the front of the plastic sheet through an air compressor, making the softened plastic sheet adhere to the mold;
(3) Positive and negative pressure suction molding machine is a method of molding softened plastic sheets by creating a strong pressure difference on both sides of the plastic sheet through pressurization and vacuum pumping. These three devices each have their own advantages and disadvantages, and the machine needs to be selected based on the characteristics of the product.
At the same time, the vacuum forming machine is also divided into two categories based on the forming step method:
(1) A one-step molding machine integrates heating, vacuum forming, and die-cutting of plastic sheets, with high production efficiency, suitable for vacuum molded products with low quality requirements;
(2) A two-step molding machine is a machine that separates the heating, vacuum forming process, and die-cutting of plastic sheets, suitable for vacuum forming products with high quality requirements
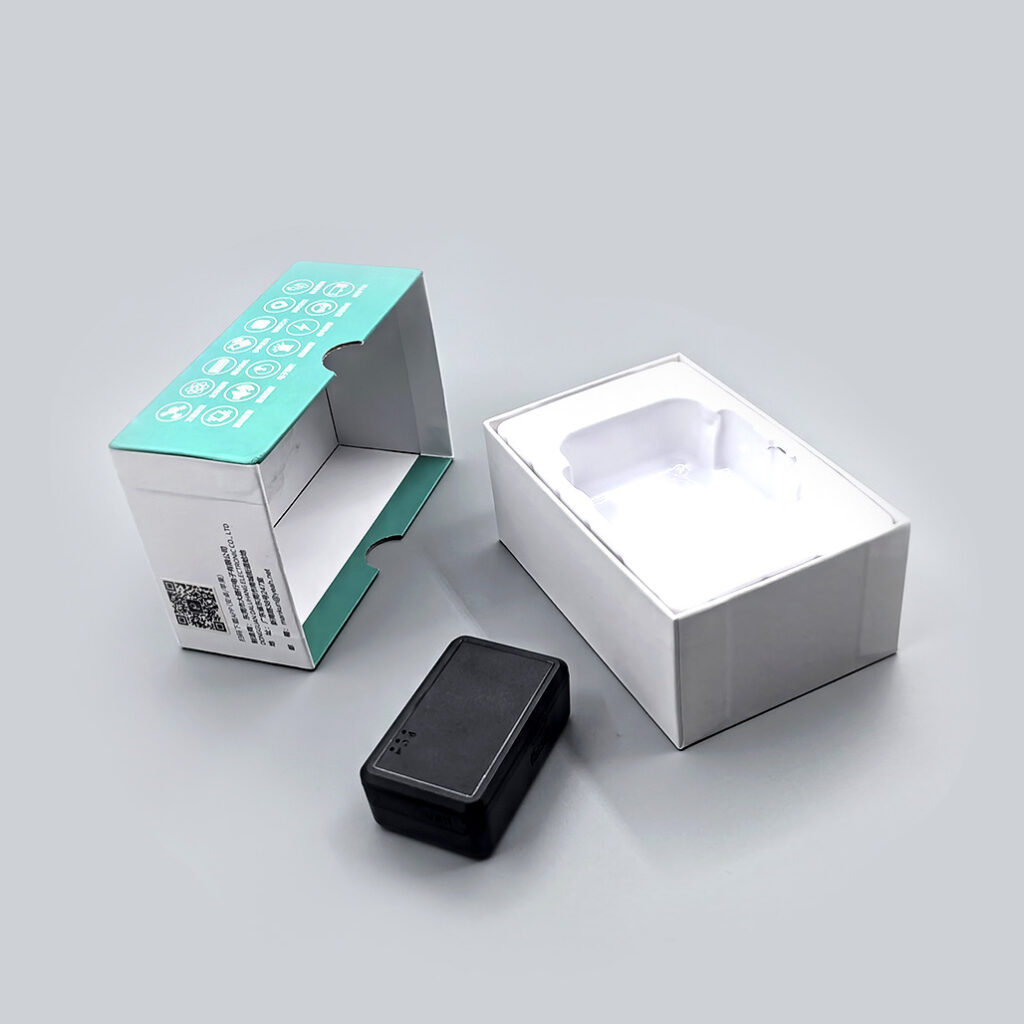
5、 Vacuum molding mold
Vacuum forming molds play a very important role in the quality of vacuum formed products. Vacuum forming molds can be divided into three types: convex molds, concave molds, and convex convex molds. The material of molds can also be divided into gypsum molds, copper molds, hardware molds, etc. based on product design and usage conditions

6、 Application of cosmetic packaging materials
Vacuum molded products are processed using plastic, and the principle of product generation is to heat and soften the flat plastic hard sheet material, then vacuum adsorb it onto the surface of the mold, and then cool it to form. Vacuum molded packaging products mainly include: bubble shells, trays, and vacuum boxes. Mainly plays a role in protecting the inner packaging materials and contents.