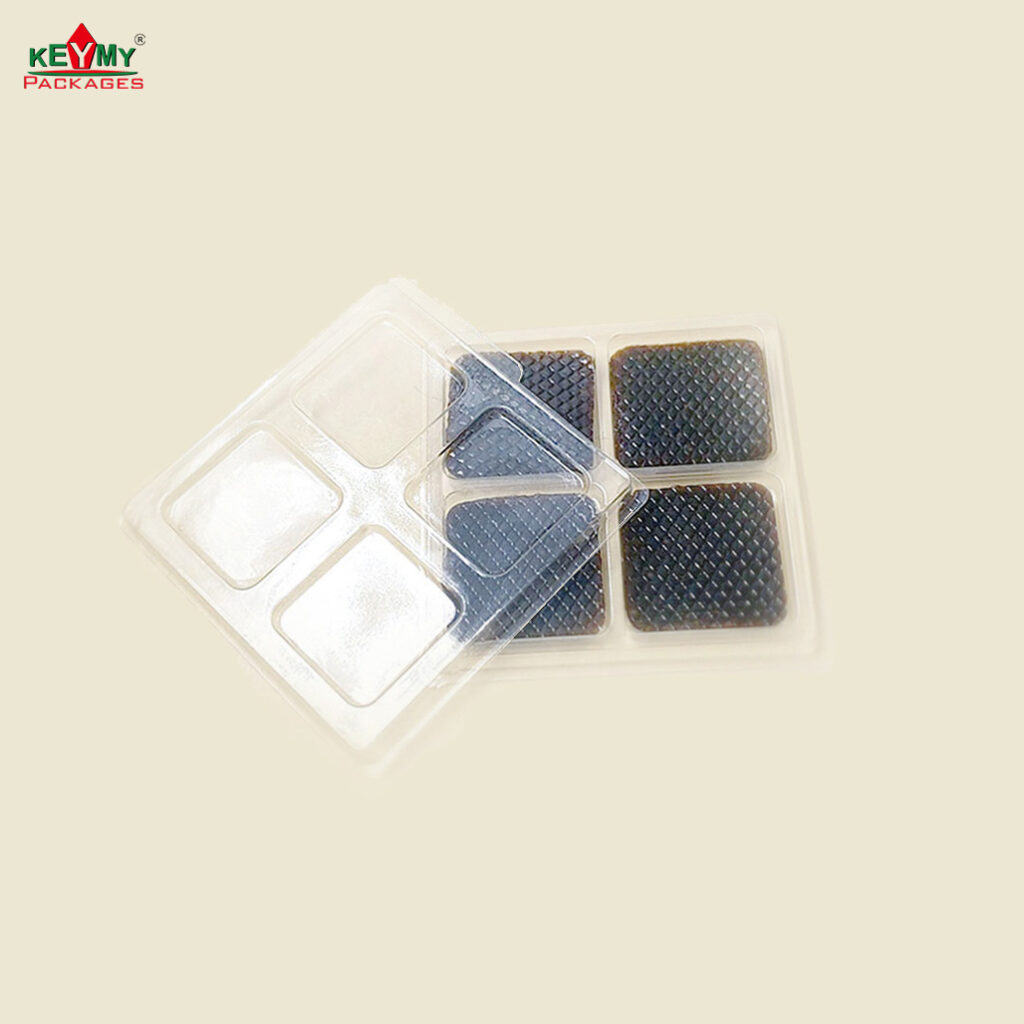
Produce plastic products using vacuum molding technology and package them with corresponding equipment. This process is called vacuum packaging.
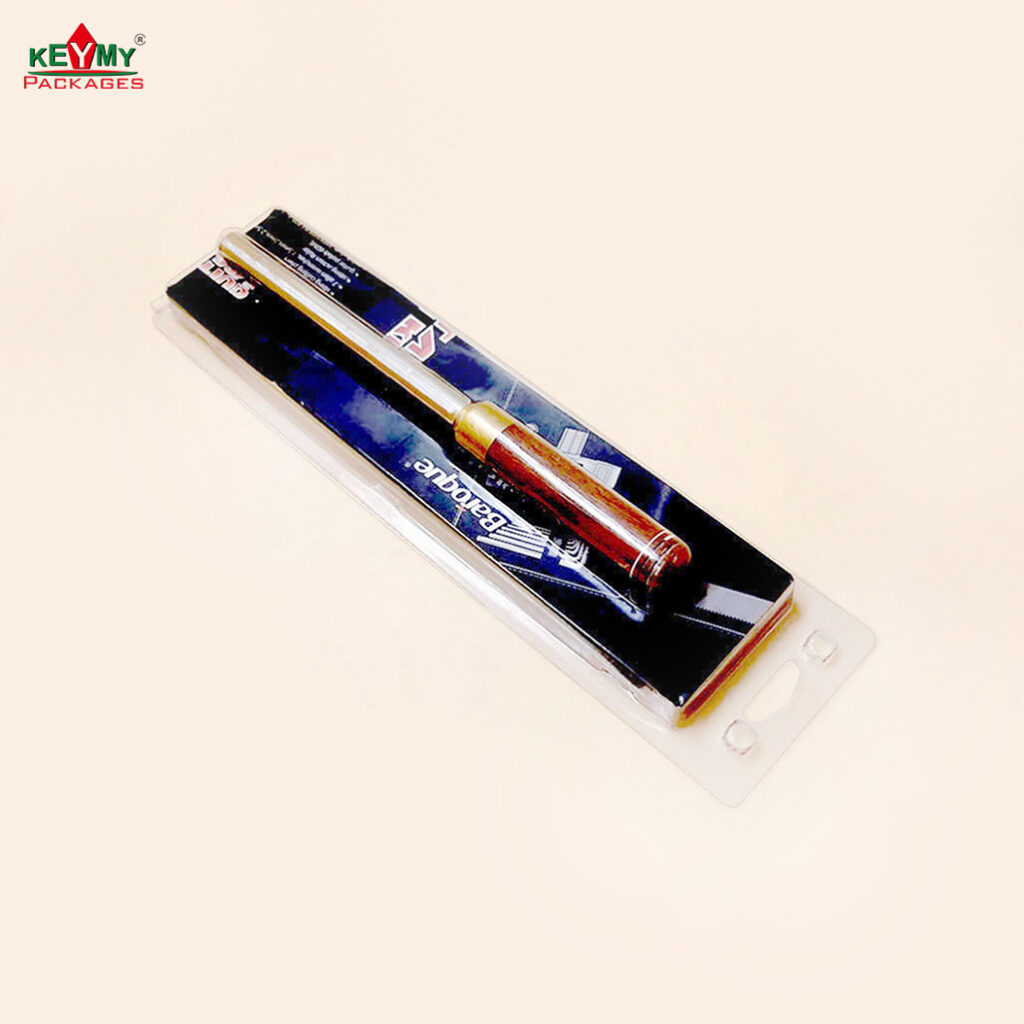
The main advantages of vacuum packaging are saving raw materials, light weight, convenient transportation, good sealing performance, and meeting the requirements of environmentally friendly and green packaging; Can package any irregular products without the need for additional cushioning materials for packaging; The packaged products are transparent and visible, have a beautiful appearance, are easy to sell, and are suitable for mechanized and automated packaging, which is convenient for modern management, saves manpower, and improves efficiency. The vacuum packaging equipment mainly includes: vacuum molding machines, punching machines, sealing machines, high-frequency machines, and folding machines. The packaging products formed by packaging can be divided into: card insertion, card suction, double bubble shell, half bubble shell, half fold bubble shell, triple fold bubble shell, etc.
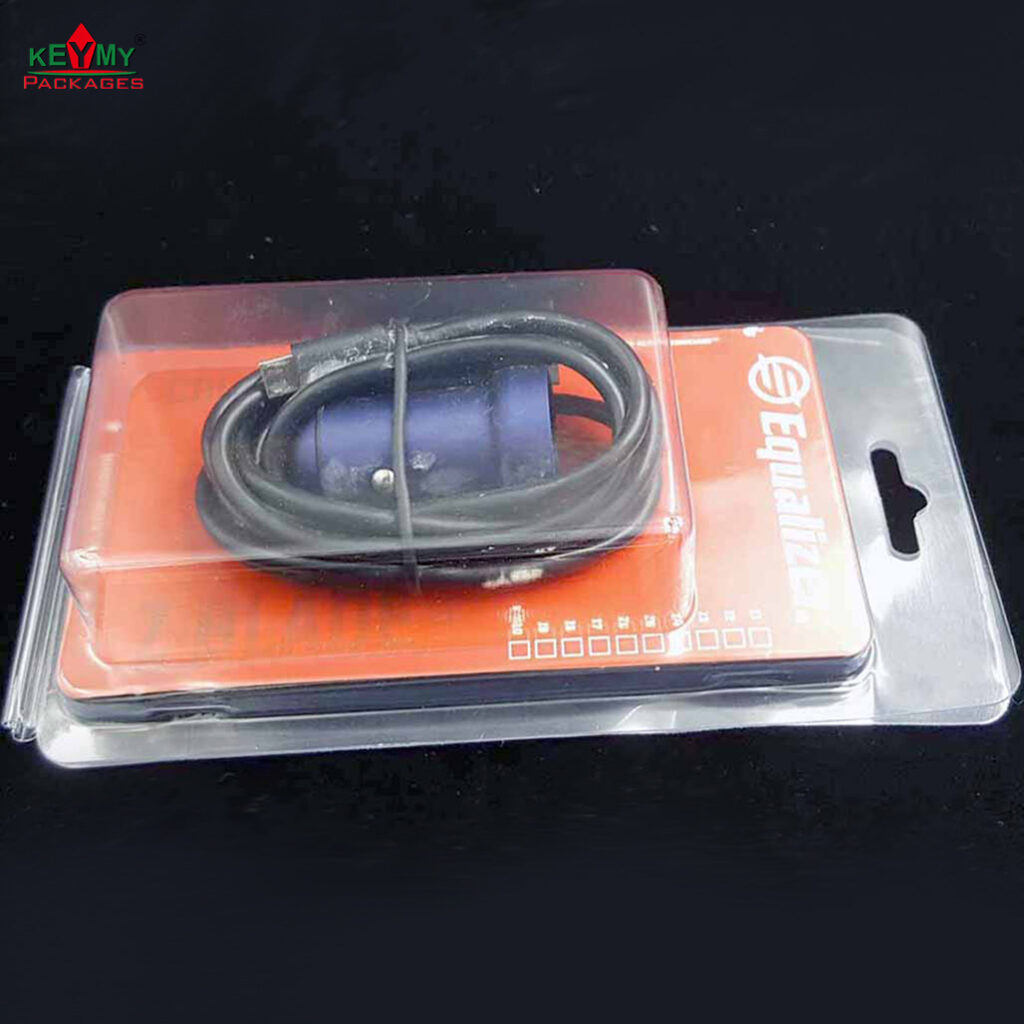
Q&A on Eight Common Knowledge of Blister Packaging

What is suction card packaging? What issues should be noted in suction card packaging?
Card suction packaging refers to the process of heat sealing the bubble shell onto the surface of a paper card with vacuum oil, which is commonly used in supermarket battery packaging. Its characteristic is that it requires vacuum sealing equipment to package the product between the paper card and the bubble shell. The issues that should be noted are: 1. It is required that the surface of the paper card must be coated with vacuum oil (so that it can be thermally bonded with the PVC foam shell); 2. The foam shell can only be made of PVC or PETG sheets; 3. Because the bubble shell only adheres to the surface of the paper card, the packaged product is not easily too heavy.
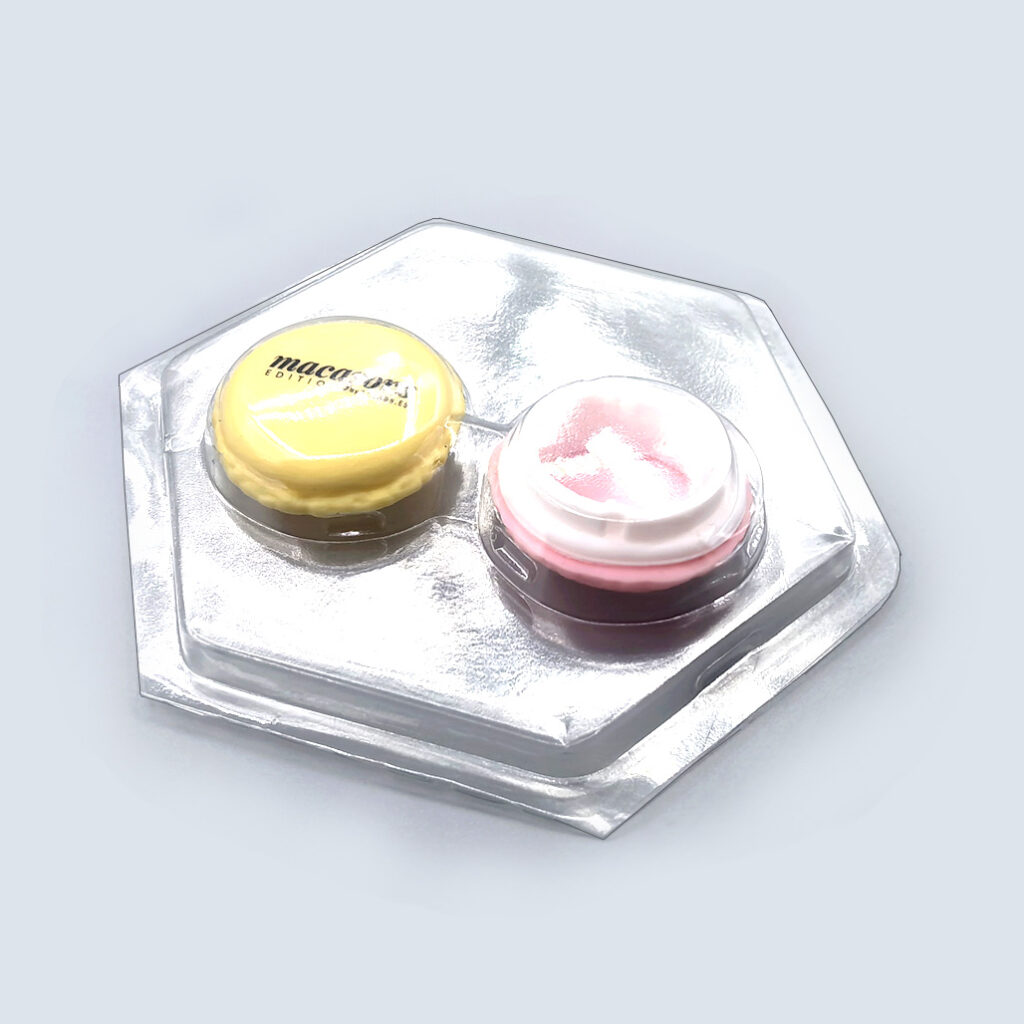
What is card insertion packaging? What issues should be noted in card packaging?
Card insertion packaging refers to a packaging form in which paper cards are inserted together with transparent bubble shells folded on three sides. Its characteristic is that no packaging equipment is required during packaging, and workers only need to place the product, bubble shell, and paper card in place. The issues that should be noted are: 1. The size of the paper card and the folded bubble shell is appropriate. If they are inserted too tightly together, the paper card and bubble shell will deform; If it is too loose, it will easily detach. When the product is too heavy, it is necessary to consider using staples to fix the paper card and bubble shell in a certain position.
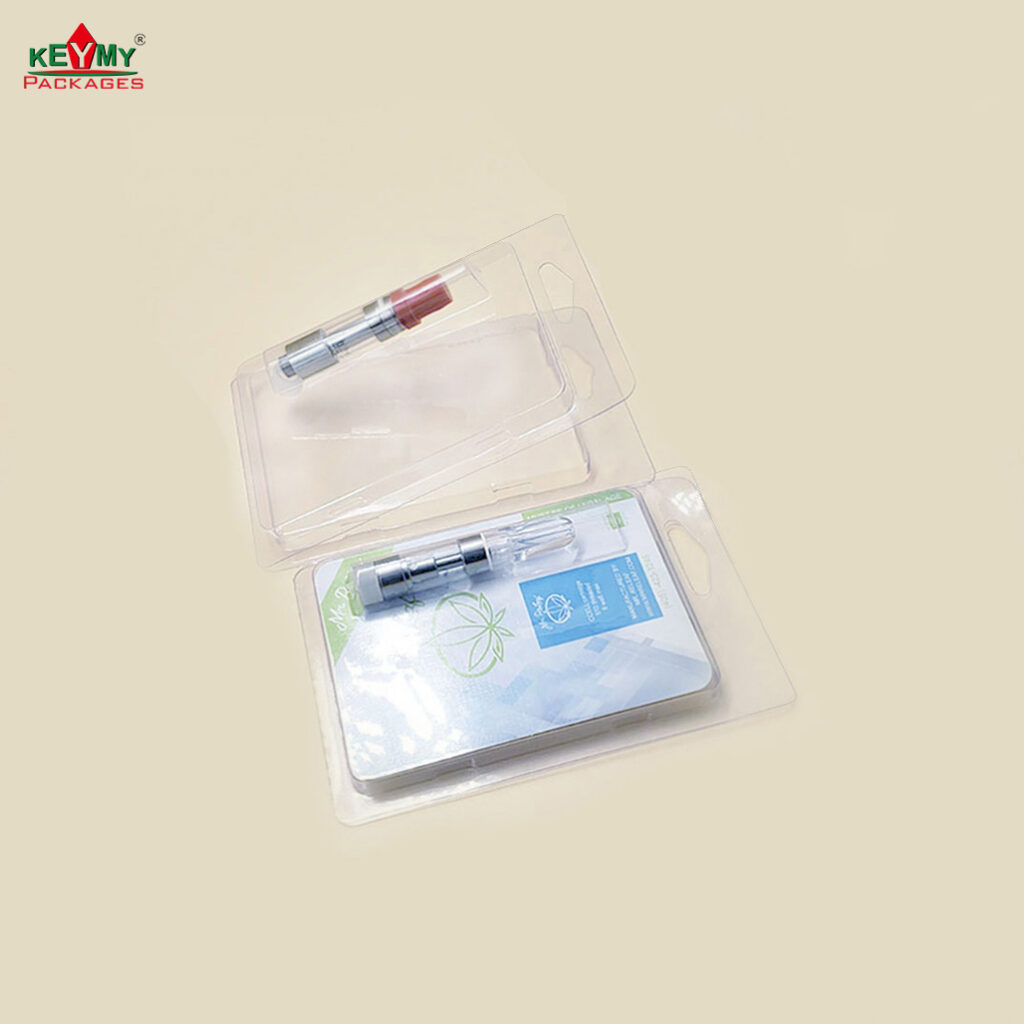
- What are the commonly used plastic sheets for vacuum packaging? What are their characteristics?
Answer: The sheets used for vacuum packaging are called hard sheets or films, and commonly used ones include PET (polyethylene terephthalate) hard sheets, PVC (polyvinyl chloride) hard sheets, and PS (polystyrene) hard sheets. PS hard sheets have low density, poor toughness, are prone to combustion, and produce styrene gas (a harmful gas) during combustion, so they are generally used to produce various industrial vacuum pallets. PVC hard sheets have moderate toughness and are not easy to burn. When burned, chlorine gas is produced, which has a certain impact on the environment. PVC is easy to heat and can be sealed by sealing machines and high-frequency machines. It is the main raw material for producing transparent vacuum products. PET hard sheets have good toughness, high transparency, are easy to burn, and do not produce harmful gases during combustion. They are environmentally friendly materials, but they are expensive and suitable for high-end vacuum molded products. Generally, vacuum molded foam shells in European and American countries require PET hard sheets, but they are not easy to heat seal, which brings great difficulties to packaging. To solve this problem, people composite a layer of PVC film on the surface of PET, named PETG hard sheets, but the price is higher.
What is double bubble shell packaging? What issues should be noted in double bubble shell packaging?

Double blister packaging refers to a packaging form where two blisters are used to package the paper card and the product together. Its characteristic is that it requires a high-frequency machine to seal the edges of the double bubble shell, which has low efficiency and high packaging costs, but the edges are neat and beautiful, and the product has a high-end appearance. The issue that should be noted is: 1. The foam shell can only be made of PVC and PETG film, otherwise it cannot be heat sealed or the heat sealing effect is poor; The quality of the edge of the double bubble shell is determined by the quality of the high-frequency mold.

- What is semi bubble shell packaging? What issues should be noted in semi bubble shell packaging?
The full meaning of semi blister packaging is a double blister packaging with semi exposed products, which refers to the packaging form where two blisters are used to package the paper card and the product together, but the product is partially exposed outside the blister. It is suitable for particularly long products. Its characteristic is that it requires manual cutting of the exposed part of the bubble shell with scissors, and then using a high-frequency machine to seal the edges of the double bubble shell. This has low efficiency and high packaging costs, but it has a good visual effect and can meet the needs of users to directly touch the product when picking products in supermarkets. Attention should be paid to: 1. Products that are prone to getting dirty are not easily packaged in this form; 2. When cutting holes on the bubble shell, attention should be paid to neat edges; The foam shell must be made of PVC or PETG hard sheets.
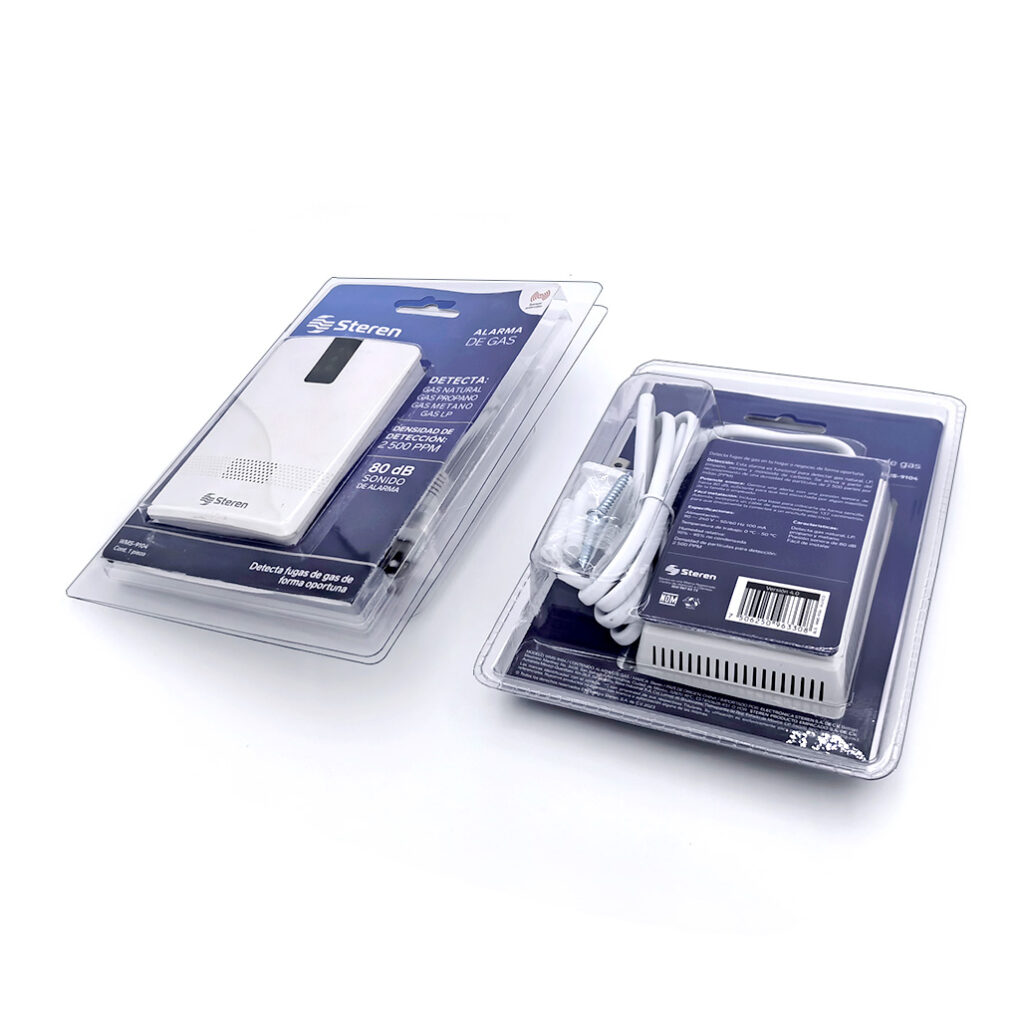
- What is an external semi bubble shell packaging? What issues should be noted for external semi bubble shell packaging?
The full meaning of external semi bubble shell packaging is that the product is completely placed outside the double bubble shell, which only encapsulates paper cards and serves as the bottom support for the product head. The product is connected to the bubble shell with plastic straps. Its characteristic is that it requires a high-frequency machine to seal the edges of the double bubble shell and drill binding holes on it, which has the lowest efficiency and high packaging cost, but can meet the needs of users to touch the product.

- What is folded bubble shell packaging? What should be paid attention to when folding bubble shell packaging?
Folded blister packaging refers to the process of connecting one side of a double blister shell during vacuum molding, and folding it to form the bottom and surface of the double blister shell. Its characteristic is that high-frequency edge sealing technology can be omitted, and a buckle can be made at a certain position of the bubble shell to connect the double bubble shell. If necessary, staples can also be used. In terms of material selection, PET hard sheets can be used to achieve the goal of environmentally friendly materials. Attention should be paid to the following issues: 1. Due to the lack of high-frequency machine edge banding, the edges need to be cut with high quality on the cutting machine; 2. The tightness of the buckle should be moderate.
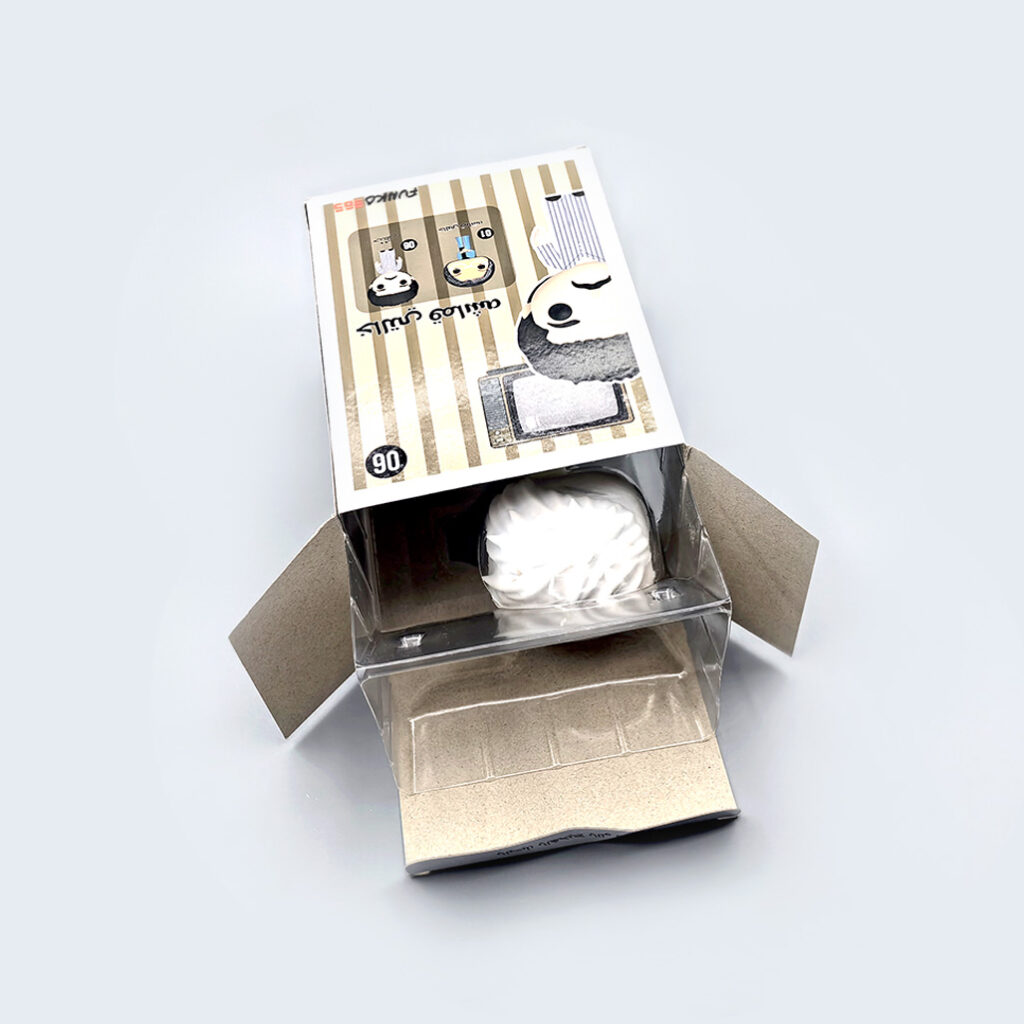
- What is a three fold bubble shell packaging? What should be paid attention to when packaging three fold bubble shells?
Triple fold blister packaging is the process of folding the blister into three sides (front, bottom, and back), forming an additional bottom edge so that the product can stand on a flat surface. Its characteristic is that high-frequency edge sealing technology can be omitted, and a buckle can be made at a certain position of the bubble shell to connect it. If necessary, staples can also be used. In terms of material selection, PET hard sheets can be used to achieve the purpose of environmentally friendly materials, suitable for packaging large-diameter products. Attention should be paid to the following issues: 1. Due to the lack of high-frequency machine edge banding, the edges need to be cut with high quality on the cutting machine; 2. The tightness of the buckle should be moderate
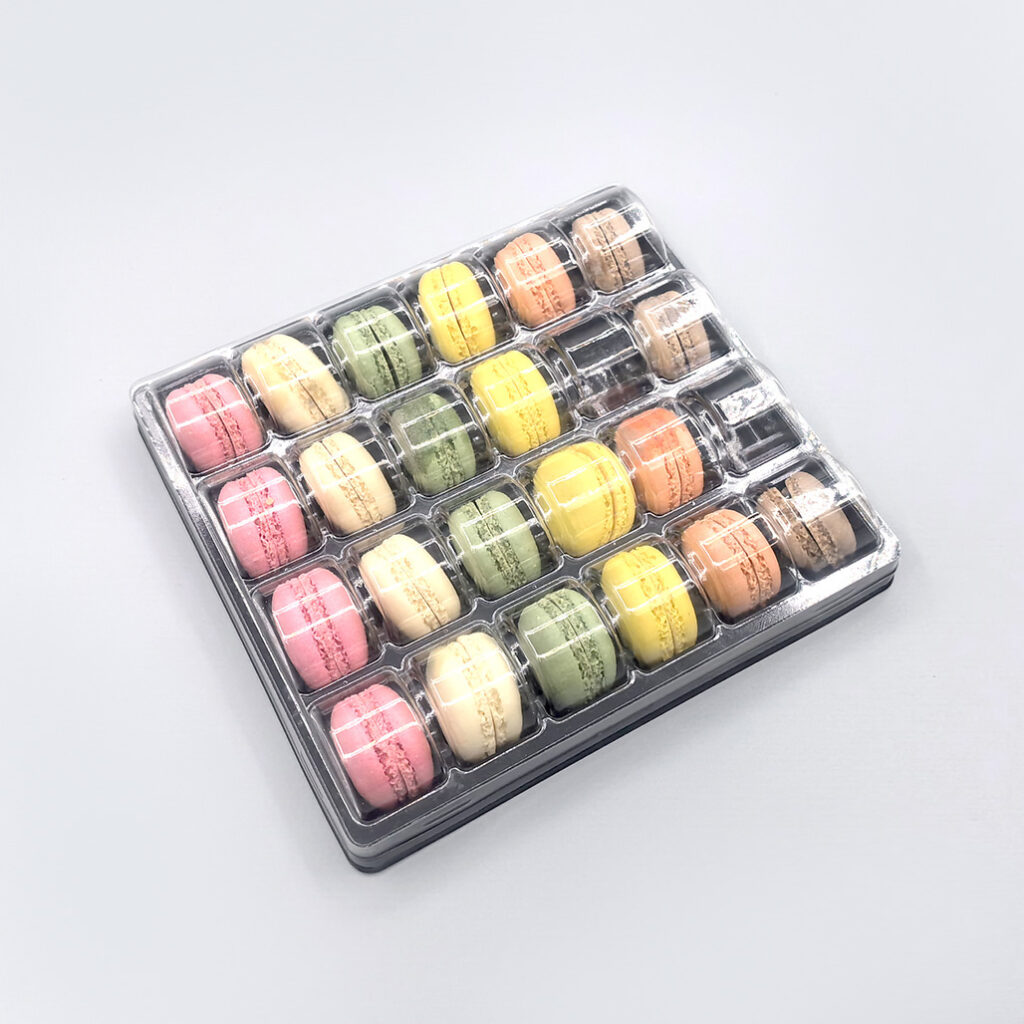